Who Handles Maintenance At Your CDMO? You Should Know

By Louis Garguilo, Chief Editor, Outsourced Pharma
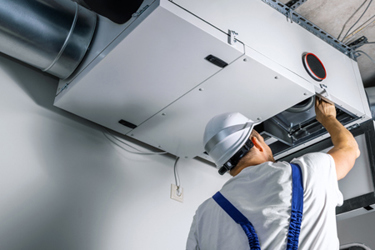
After 30 years at Merck, Charlie Hoff for the past 15 has been performing integrated facility maintenance for other organizations, and increasingly for CDMOs.
For Hoff, it’s been a combined 45 years of big-ticket thinking:
- Computerized Maintenance Management Systems (CMMS) to track assets from lab to manufacturing;
- Integrated Facilities Management (IFM) combining processes and technologies under the direction of a single team, and including supplier relationships and real estate management;
- Mechanical / Electrical Systems (M&E), including instrument/equipment installations and calibrations.
Then there are the more “mundane” services (until something goes awry), such as:
- Janitorial
- Cafeteria
- Pest Control
Hoff, an SVP and Account Executive / Life Sciences Contract Organizations Leader at JLL, provides thoughts on what you should know about who maintains your CDMO's’ facilities, as well as a window into what’s happening in the world of maintenance at large.
CDMOs Provide Economic Advantages
Hoff says he was lucky to have held several positions at Merck before and after getting into maintenance. They provided him a well-rounded perspective on biopharma facility operations.
Over his career, he’s supported the maintenance (and construction) of everything from pilot plants to office buildings, but there’s an interesting dynamic when it comes to CDMO facility maintenance.
Their customers include a component of cost savings in their rationale for outsourcing. CDMOs must be capable of maintaining labs and facilities “efficiently and productively so those clients can in fact tabulate a certain cost advantage.”
One way to do that is by outsourcing facility services (so they can focus on you and your programs.)
“CDMOs are there to provide an economic advantage to the drug sponsor. They can do that by the better utilization of their facilities,” says Hoff.
CDMOs, says Hoff, should “habitually try to figure out how to skinny down sunk costs within that facility overhead. For us, as a maintenance service organization, we help them do that, and on behalf of their customers.”
Ironically, at times the way his organization saves CDMOs money is to eliminate some of their outsourcing.
“CDMOs, and sponsor alike, may have taken outsourcing too far, hiring a variety of third parties for what we consider “out tasking.” (More on this later in part two)
Therefore, when a CDMO outsources to Hoff’s maintenance management team, that team in-sources many of the services that had been spread around to various external partners.
In our parlance, JLL takes on a one-stop-shop for maintenance model.
Improving Maintenance Services
A market gyration generating new CDMO clients for Hoff is the increase in CDMOs purchasing former pharma facilities that were outsourcing maintenance services to JLL.
But along with that organic movement, CDMOs themselves have begun to further explore maintenance options, particularly the larger service providers.
“CDMOs get siloed,” Hoff says. “They buy up companies that stay siloed – ‘This is my site and this is how we run it.’ In many cases, they actually don't even talk to one another.”
Hoff is hired to think more holistically, even “out of the box” on maintenance-policy integration.
“For example,” he says, “I identify experts from one site and say, ‘Hey, can you help out another site or help develop a program for the overall account?’”
“I'm bringing talent to the facility and project where it is needed. Our CDMO clients don’t necessarily think that way. Perhaps they do in the operations world, but not consistently in the maintenance world.”
I’ll bet it comes to readers as no surprise to hear of certain siloization at big CDMOs even on the maintenance side of their business, not dissimilar to your experiences on the operations side.
This lack of facility-to-facility coordination, which Hoff reminds me would drive down costs if done properly, goes on despite global CDMOs advertising to the very opposite: Working with us, you get the benefits of a network of sites, redundancy, and risk mitigation.
“I am not going to comment on the operations side,” says Hoff. “I'm only saying what I see from a maintenance perspective. Obviously, CDMOs are doing a lot right on the business side for customers.
“I’m just saying they could get better at maintaining their facilities, and I think that's why they bring us in.”
The FDA And Pest Control?
Big Pharma outsources manufacturing to Big CDMO, who is increasingly outsourcing maintenance to Big Maintenance (such as JLL).
Some may feel left out.
But according to Hoff, all sizes of pharma and CDMO – and sponsors – can take advantage of better maintenance.
Let’s entertain a case study.
A seal breaks on a large-scale vessel. Miniscule pieces of rubber and plastic enter a batch (or two). (If you are surprised, dear reader, yes, this does happen.)
Upon the news, the sponsor hops on a flight to the facility or if that isn’t possible, a video call.
In short order, the customer is in a conference asking, How could that happen? What will you do ensure it doesn’t happen again?
Is Hoff and company there as well?
“Absolutely,” he answers. But to be clear, he adds, each CDMO client of his may handle this differently.
“If it’s an on-site meeting, we may be in the same room or in a back room providing them documentation and other assistance, but we’re always involved, whether we have a CAPA assigned to us directly or we’re working within their TrackWise system [digital quality ecosystem] or more generally.”
“Recently,” he adds, “I had a team sitting in front of the FDA with a CDMO, talking about temperature excursions, because actually, we are the experts doing the work.”
“And by the way,” Hoff says sneaking us back to pest control, “with the FDA, it’s highly likely maintenance quality can lead to questions regarding pest control.”
“I mean it is a big deal – and it is usually outsourced. I consider pest control more of a ‘hard service’ and treat it as a program not just a contract because it's so critical.”
“Regulators come in and they want to know pest control details and protocols, and related training records.”
Nobody’s suggesting the regulators are the pests, but Hoff is suggesting you should be aware of the facility maintenance prowess at your CDMO, from any scurrying mice to management and operations.”
-----------
More with Charlie Hoff on CDMO facility management coming up in part two.