Wanted: Multi-Experienced Employees For Outsourcing

By Louis Garguilo, Chief Editor, Outsourced Pharma
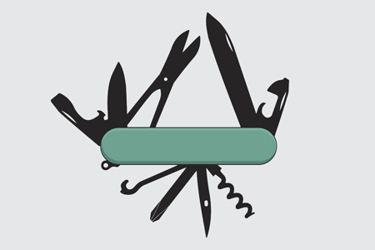
Imagine a single resource supporting your organization’s drug development and manufacturing programs, who is described thus:
“Twenty-five years’ international experience working in positions at Big Pharma and biotechs in process development, technical operations, CMC, supply-chain and lifecycle management, manufacturing sciences and engineering, and all aspects of outsourcing and managing CDMOs. An industry-recognized expert in quality by design (QbD). Accomplishments include successful development and commercial manufacture of small and large molecule products, as well as generics.”
Actually, you’ve just met Jana Spes.
Unfortunately, she isn’t for hire at the moment. After working at companies such as Pfizer, J&J, and Ferring Pharmaceuticals, at the end of 2018 she planted her multifarious flag at Ironwood Pharmaceuticals in Boston.
But she does provide you with some uniquely qualified analysis and guidance on outsourcing and working with CDMOs.
Don’t be surprised if you come away thinking for your next outsourcing operations hire, specialization is out, and the Spes model is in.
A Woman For All Phases
Two industry trends have converged to increase the need for multi-experienced outsourcing professionals.
The embracing of the virtual — or at Big Pharma, streamlined — model for biotechs, while at the same time, CDMOs began to offer a continuously wider variety of services to support those models.
“Did CROs and CMOs have the foresight to anticipate which way outsourcing was heading?” Spes asks.
“Or was it the actual evolving to the virtual model by biotechs, and Big Pharma’s new desire to work with strategic partners, that advanced the industry? We’ll never know who the genius exactly was at the given moment.”
We do know that as a result of these changes, this is happening:
While on the one hand drug development and manufacturing dashes toward narrower and deeper specification (e.g., antibody-drug conjugates [ADCs], monoclonal antibodies [mAbs], cell and gene therapies, personalized medicine, orphan-disease markets, etc.), the actual “art of outsourcing,” as Spes describes it, stands in bleak contrast – it now benefits from a broader brush of experience.
“I’ve been fortunate to gain commercial experience early on, and also have a career on the interface between ‘r’ and ‘d,’ including technical operations and lifecycle management,” she says.
“I can fully understand the end game from the earliest points of a drug program’s departure. And that end game today requires recognizing as early as possible the needs for flexible drug product manufacturing, whether it’s capacity, quality, analytical testing, packaging, supply chain distribution, or lifecycle management.”
She provides an example:
“You discover you need to qualify a second manufacturing partner, because projections indicate your capacity will run out two years after launch. You must identify a CMO and perform a tech transfer. First, this need might have been avoided with more foresight.
“However, based on well-rounded experience, I can now seamlessly translate all of these current and future needs into the required development activities, including understanding who the correct new manufacturing partner should be.
“So, given this broad adoption of the virtual model, and ‘end-to-end development,’ what we call ‘tech ops’ expertise is becoming an amassed group of specialties needed to work with CDMOs effectively.
“And I can tell you there is a huge demand for people with end-to-end experience to match the services at the CDMOs.
“In today’s environment, early decisions you are making are not reversible later. Those analytical, sourcing, and manufacturing strategies will stay with you throughout your filing and launch of the product.”
I ask Spes if there’s been one prevalent piece of advice – an admonition perhaps – she’s adhered to over her career.
“First, on the plus side,” she replies diplomatically, “my current company is quite sophisticated. I think the tide is changing throughout the industry. People understand early on that the products they’re developing are intended for commercial scale, and all their decisions have consequences.
“However, over the years I have seen where a biopharma’s R&D group is strictly focused on their current mission with suppliers. After minor scale-ups, neither they nor their vendors can imagine manufacturing on the required commercial scale. It’s not in their realm of experience.
“So I always advocate breaking down those internal silos, if they exist. And I think both the drug sponsors and service providers are evolving to accomplish this.”
When We Do Specialize
We’ll end this first of two parts with Spes by noting that even multi-experienced professionals tend to acquire particular areas of expertise and focus in their careers.
Quality by Design (QbD) was that specialty for Spes.
QbD can be summarized as a systematic approach to pharma development and manufacturing. Its full detail and implementation, though, are anything but simple. QbD was formally introduced under ICH Q8 Guidance published by the FDA in 2006.
As updated guidance on QbD continued to flow from the agency, Spes was involved with a pharma development team on an early implementation strategy.
It was an early experience of “teaching” QbD strategy that planted her firmly on the path to becoming a recognized leader in the discipline.
“We realized our established service provider in southern Europe had no knowledge or experience with QbD. This was not unusual at the time,” she recalls.
“We began to patiently walk them through the process, considering them as our own team members, and involved them in every aspect of how we were developing our QbD processes.
“Fast forward to some years later, and this CDMO now uses its experience in QbD as a selling point to attract biopharma customers, and hence can provide premium services.
“Now they claim they are best-in-class in QbD tools and experience.”
That sort of “teaching” experience has, in fact, become part of the mosaic of our outsourcing industry, and reminds us again of the importance of multi-talented employees.
If not exactly like Spes, as close as you can get.
-------------
This editorial is revised from the original in Life Science Leader’s 2020 CMO issue.