The "Build Strategy" Behind Shire's Plasma Manufacturing Center

By Louis Garguilo, Chief Editor, Outsourced Pharma
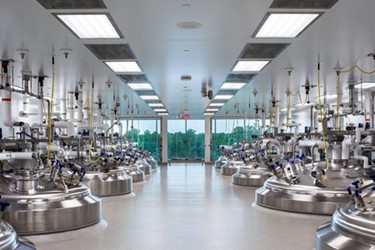
Among other accolades and well documented in these pages, Shire is a proficient drug development and manufacturing outsourcing organization.
So why is the recent excitement from Shire about a large facility “build,” instead of an external services “buy”?
We’re talking about the recent press release announcing the FDA approved Shire’s first submission from its new plasma manufacturing facility, located near Covington, Georgia.
Matt Walker, EVP of Technical Operations, was gracious enough to detail for Outsourced Pharma readers why Shire built this internal capacity, and how they settled on a location east of Atlanta.
Building Details
Shire’s new plasma manufacturing facility originally broke ground in 2012. The estimated overall cost to completion (including equipment) is between $1.5 billion and $2 billion. This state-of-the-art facility occupies more than 1 million square feet. It is set within a business park of about 1,600 acres.
The selection process for the plasma facility was actually undertaken by Baxter, who had investigated locations both outside and inside the U.S. Baxter spun off its bioscience business as Baxalta in 2015, and Shire acquired Baxalta – and the Covington site, as it is known – the following year. The new facility is less than an hour east of Atlanta.
“Some biotech people think there’s not much industry there,’” says Walker, who joined Shire in 2016 after a successful career at Pfizer. “But you might be surprised. It’s become a part of the large-molecule biologics infrastructure, and a growing biologics network and ecosystem, particularly if we look at the broader Atlanta area. And obviously you need land to develop a project of this magnitude. There’s quite a bit of land in that region.”
State incentives can nudge the site-selection process as well.
“There were incentives provided by the state of Georgia that were part of the Baxter decision-making process. Of course Georgia was competing with large-molecule centers like Boston or Research Triangle Park, or on the West Coast,” says Walker.
This was a “pure greenfield location,” with all the necessary utilities and permitting. The site itself came about as a result of four Georgia counties teaming up through a Joint Development Authority. The original intent of the JDA appears to have been to attract advanced manufacturing, but Walker mentions one of Shire’s newest neighbors will be Facebook, also building a large facility there.
Of equal importance to the location selection was the agreement by the state of Georgia to build a comprehensive training center across the street from Shire’s facility.
“We’ve used that extensively,” says Walker. “Many of our manufacturing employees have gone through training at the center. This is a successful model they’ve used in Georgia in different locations with different industries.” We’ll go deeper into this subject specifically in a follow up article with Walker.
Covington Comes On Line
The FDA approved Shire’s first submission from the Covington plasma manufacturing facility for the production of GAMMAGARD LIQUID [Immune Globulin (IG) Infusion (Human)], a replacement therapy for primary humoral immunodeficiency (PI). The Covington facility will add approximately 30% capacity to Shire’s internal plasma manufacturing network once fully operational.
The Covington facility is “vertically-integrated,” says Walker, including a crucial testing center, which was part of the vision for building the facility.
“The fractionation, purification, and filling processes for IG are all done there,” he explains. Also ready for operation once further FDA approval comes is the fractionation and purification for albumin. The eventual production of FLEXBUMIN products will happen at a sister facility in Round Lake, IL.
Besides the two most prominent proteins typically extracted from plasma – IG and albumin – there are a number of other products that potentially come from a liter of plasma. “You can either design your facility to capture many additional proteins, or to capture specifically IG and albumin,” explains Walker. “The Covington site is focused specifically on the latter.”
Walker also makes clear the facility was designed for future expansions. And the overall Covington site plan allows for the build out of additional facilities.
“It’s exciting to finally get to a point where we’ve got FDA approval, and we can begin to release commercial products from the facility,” he adds.
The Shire Strategy
Shire highly leverages external supply for its small-molecule product lines. The biologics side of the business has been more of a mix of internal capability for drug substance, and externally provided drug product. That has changed a bit, says Walker.
When Shire and Baxalta combined in June of 2016, the new entity initiated a manufacturing network assessment. Walker said it was a typical exercise of these sorts, including forecasting of future demand requirements, making sure the right capacity was in place, analyzing utilization, as well as other factors.
“We focused on what core capabilities we believe we have that provide an internal advantage, versus leveraging contract manufacturers,” recalls Walker. “That’s when we solidified this decision around vertical integration. Clearly, this is how the overall plasma industry has been organized for many years, so I wouldn’t say we came up with some groundbreaking revolution.
“But the reality is,” he continues, “there is an art and science to plasma manufacturing and plasma supply. What we found was that we have deep capabilities built over many decades. We looked at that, and at the fact our primary focus was our biologics network and large molecules.”
Two-thirds of Shire’s current pipeline is in fact in the large-molecule space. According to Walker, the company is keen on moving forward with the internal building of “a deep capability from process development all the way through life-cycle management, supply chains, you name it.”
All along, then, it has been these specific technologies and capabilities as the drivers for a vertically integrated plasma business. “Biologics and plasma are two areas where we believe having internal capability differentiates us in the marketplace,” says Walker.
Nonetheless, outsourcing is indeed in Shire’s DNA, and today rarely any segment of the entire biopharma industry operates wholly intact internally.
“It’s not as if we’ve made a decision that every single thing will be made internally,” adds Walker. “We still have third-party providers in the plasma business. We still have third party providers in the biologics space. But predominantly, those two spaces are internally focused.”
--------------
Editor’s Note: In a follow up to this article, we’ll again talk to Matt Walker, EVP of Technical Operations, about the workforce for Shire’s Covington, Georgia-based plasma manufacturing facility.