Not Particularly For A Pandemic, But The Supply Chain Was Ready

By Louis Garguilo, Chief Editor, Outsourced Pharma
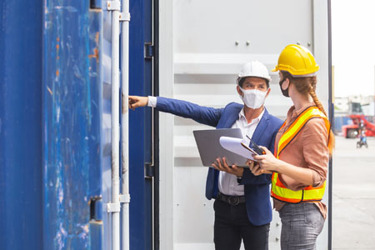
“First off, there's a lot more interest in supply chain. Supply chains used to be the thing no one talked about or thought about much, like the offensive lineman in football. You're only noticed when you're caught holding on a touchdown play. Most of the time, it's been kind of the invisible giant in the room.”
“But now you have consumers, governments, senior management – they all have interests in supply chain. Even things that are typically viewed as commodity items or ancillary supplies. We really needed to take a deeper look at those, because we realized that's all it took to cause issues.”
-- Ken Kent, Senior Vice President, Chemical Development and Manufacturing Operations, Gilead Sciences
Perhaps none better at connecting those (ongoing) efforts with future actions than a discussion at Virtual DCAT Week 2021 (July 12 -16). (DCAT is the Drug, Chemical & Associated Technologies Association.)
Titled Manufacturing and Supply - Lessons Learned from the Pandemic, the discussion featured
Remo Colarusso, Vice President, Janssen Supply Chain, Johnson & Johnson, and Ken Kent, Senior Vice President, Chemical Development and Manufacturing Operations, Gilead Sciences.
It Didn’t Commence With COVID
“We overcame a lot of the border closings and transportation issues we encountered, and were able to leverage our existing supply chain and risk management practices despite the new challenges.”
Nonetheless, going forward, he’ll more rigorously learn of the risk management plans at partners and suppliers for all his products.
What's evident a year later, Colarusso says, is any single component needed for your product can severely impact the entire production – particularly “when you are trying to move at a thousand miles an hour,” as the industry was in getting vaccines developed, approved, manufactured, and distributed.
“If it's a $2.49 piece of specialty tubing you need now, and the supplier is out, no matter what price you offer, they just don't have it,” he said.
“And when we started to see these issues pop up, particularly in the consumables – the single-use disposables and other technology items – it wasn’t even the first-tier suppliers. It was their suppliers having trouble supplying them, which made them have trouble supplying us.
“While the difficulty is how far to go before it becomes a law of limiting returns, we clearly found out we needed to broaden our scope to not only the primary suppliers and partners, but also to their primary suppliers and partners, in order to get a better feeling for the resiliency that we truly have.”
Kent agreed: Gilead fared as well as could be expected, because of how they operated prior to the pandemic.
“It was about preparation,” said Kent. “No one was ready for a pandemic, but when it comes to supply, we're always thinking about what could go wrong, because things do go wrong in manufacturing.
“Having those ‘What if’ scenarios upfront in your mind, and actually having mitigations for those possible events, is key.
“We'd always thought there could be EHS issues [Environmental, Health and Safety], or maybe some sort of government intervention when trade wars are happening, or even natural disasters.
“Having that mindset gave us a playbook to go to that allowed our supply chains to be resilient and robust. I think that was our number one tool.”
Kent also suggested how to fully consider “component risk”:
“It was amazing. Every component product that touched your product, every disposable, consumable, they were all under pressure. Things you would never even anticipate.
“Early on in the pandemic, for example, carbon dioxide was in shortage because it's a by-product of the fuel industry. We use that in processing. So simple things like that can trip you up.
“It made us look a lot deeper into our supply chains. We found issues with disposable filters, even some types of ink for the labels we needed for standard items. It was a real lesson: it only takes one small disturbance in the supply chain to cause huge damage.
“Knowing where these components are used in all your products, and used for other customers in other industries as well, is important. We saw a slowdown in different industries that shifted supply chains and caused shortages where we'd never seen them before.
“Normally, there's just ubiquitous supply, and you are such a small buyer of that supply. It was always there; suddenly it wasn't.”
Pandemic Partnerships
Colarusso said the overall challenge for quickly developing a coronavirus vaccine – for the world – was daunting.
“You just sit there and go, how in the world do you do this?” he said.
His answer: You commit to taking financial risks.
“You'd never take risks with the product,” said Colarusso. “Always safety advocacy drives the program, but in terms of being able to take financial risks, and for example, signing multimillion-dollar contracts with suppliers and CDMOs, even though there may not be a product in the end.
That's acceptable, he says, “because we're committed to trying to make a difference. That's really the kind of thinking much more around than ever before. With all our partners as well. The collaboration was unbelievable – at a level I'd never seen it at in my whole career. Everyone wanted to help and jump in the efforts.”
“We all sort of held hands together and said, ‘[business-wise] this is going to be risky. We understand that risk. Let's just tackle it together.”
Kent added his thoughts to the coordination found at suppliers and CDMOs.
The lessons of the pandemic, he said, “didn't really change our ideas of insourcing versus outsourcing. It did make us ensure we understood our partners – and ourselves – deeply, because it doesn't take much to cause a disruption in supply chain.
“I would say the focus has been more about looking beyond just insourcing versus outsourcing, but the entire supply chain end-to-end.”
-------------
DCAT is a not-for-profit, corporate member-supported, and volunteer-led global business development association for companies engaged in the Bio/Pharmaceutical manufacturing value chain.