More Biomanufacturing Workers, Less Paper Work

By Louis Garguilo, Chief Editor, Outsourced Pharma
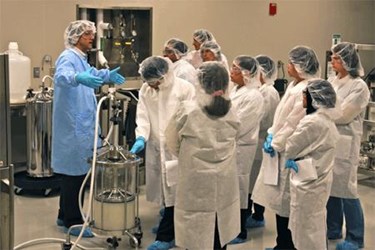
Eight hundred students enrolled in biomanufacturing courses. The number jumps out as I start my conversation with Gary Gilleskie, Ph.D., director of operations for North Carolina State University’s Golden LEAF Biomanufacturing Training and Education Center (BTEC).
He’s not including the hundreds of professionals BTEC (pronounced BeeTech) trains on behalf of biopharma like Biogen, Merck, and Sanofi, and CMOs like KBI Biopharma and Fujifilm Diosynth.
“So you’re disproving the more pervasive notion of too few science and engineering students pursuing careers in biopharma manufacturing?” I ask Gilleskie. “I think so,” he replies, seated in his office just a stone’s throw away from The Research Triangle Park. “The demand for our academic programs – and professional development – is very high.”
The demand for his students, with degrees or certificates in biomanufacturing, is also high. This new workforce ends up at companies with a local presence, like Biogen, Novo Nordisk, and Pfizer, as well as others such as Genentech, Regeneron, and Shire.
Starting this autumn, an additional focus of training at BTEC will be manufacturing execution systems (MES), starting specifically with electronic batch records (EBRs). Industry workers with this training will further nudge biomanufacturing – which has been criticized for lagging other industries –into the age of electronic manufacturing, and advanced management technologies.
It Doesn’t Look Good On Paper
Christian Fortunel, VP at LZ Lifescience, has a lot to do with BTEC’s new focus on EBRs. He worked with Gilleskie to implement his company’s platform in the cGMP facility at the center.
“I started my career at the former Fairchild [the iconic semiconductor company whose members went on to create Intel]. To handle the chemicals and micro- and nano-liter scales of production, our industry started to automate manufacturing systems and record keeping over 20 years ago,” says Fortunel. “So I agree that the biomanufacturing industry is behind in maintaining batch records. Frankly, other industries just don’t use paper that way.”
But biopharma is catching up. Gilleskie confirms that many companies BTEC is working with “already use electronic batch records or are moving in that direction.” Fortunel’s research suggests all of the top 30 pharmaceutical companies have some level of EBR deployment right now.
Will this trend continue, trickling down to mid- and small-sized pharma, and biotechs? How about at more contract development and manufacturing organizations? Perhaps a good place to start is by looking at why biomanufacturing has been slower to embrace electronic records and manufacturing execution systems.
First –for valid reasons – our industry has been hyper-IP protective and data-sharing risk-averse, even as we’ve moved into an accelerated age of development and manufacturing outsourcing (or perhaps partly because of it).
Second, the FDA and other national and regional regulatory agencies have laid down speed bumps in the path to migrating to servers, networks, and clouds.
Third, adding to this historic (negative) bias, today the world finds itself in an era of massive security breaches of government databases, bank records, and proprietary business information of all kinds – with the malfeasance attributed to everyone from agents of the Chinese government to Eastern European lone-wolf hackers. Who actually feels any data is safe online anymore? Is it a good idea today for biomanufacturing – or CMOs – to move data aloft?
Call me a Luddite if you like. But neither you nor I, and of course neither Gilleskie nor Fortunel, have solid answers to security risks. Keeping EBRs on more local networks is one precaution, but for example, in the case of a CMO, this isolation hampers the real-time data sharing with sponsors that is a key attribute of the technology.
Going back to the regulatory aspects, Gilleskie says, “The FDA’s Part 11 compliance is important when you’re implementing this kind of an electronic record.” [CFR Part 11 is within Title 21 of the Code of Federal Regulations, which lay out FDA regulations on electronic records and electronic signatures (ERES).]
Fortunel says that while the FDA may have been a negative factor in EBR implementation in the past, that is changing. He points to the agency’s creation of the Emerging Technology Team, within the Center for Drug Evaluation and Research (CDER).
Gilleskie views these changes and challenges as more reason to ensure his students are offered hands-on experience with EBRs. “This is something they may well have to deal with in their professional life. We’re not only teaching them how to use the technology, but also about the issues in implementing these systems in a highly regulated environment.”
Both Gilleskie and Fortunel think smaller and mid-sized biopharma, as well as service providers, will follow the lead of more established sponsors, particularly because EBRs improve compliance. And, it turns out, another incentive is that paper really is more expensive.
Cloud Cover For Compliance And Costs
“It’s costly foremost because it allows for operator error,” says Fortunel of data-entry in paper-based batch records. “The cost to print the paper, handle documents, process and archive, maintain for 17 years … is just the beginning. There’s also the need for redundant batch-record review. If you look at the number of quality people pharma employs just to review these paper documents, you can go from 10 to 2 professionals by implementing an MES.”
According to Fortunel, MES technology typically shows a return on initial investment in a year or so. Continual cost reductions then come in many flavors.
He mentions the simple task of an operator recording a value outside a specification in a paper batch record. “How often is this not noticed or acted upon in a timely manner?” he asks rhetorically. An EBR entry, on the other hand, immediately creates a deviation, and sends notification to those who need to start an investigation. “This might stop processing and save a batch from failure. Or save the plant from wasting days and money manufacturing a batch that will end up failing.”
Fortunel undertook a study of FDA 483 observations received by biomanufacturers. “One of the biggest observations is just not following procedures,” he says. “An EBR won’t allow that. You have to follow procedures electronically, because it sequences actions for you. In other words, you’re forced into compliance or immediately identified as out of spec.”
Allow me to wrap this up with an anecdote. While finalizing this article, I received an email invitation to attend a training webinar with this description:
“Batch Record Review is a critical part of your operations ... and a global regulatory requirement. Standard Operating Procedures (SOPs), process controls, and deviations all fall under the purview of batch control … If your batch control documents are difficult to read, sloppy or worse — non-existent — then look forward to a litany of sanctions, recalls, and costly delays … Fortunately, there are simple steps you can take to ensure your efforts are efficient and compliant.”
Perhaps those steps should also include having a chat with people like Gilleskie and Fortunel. No electronic system is perfect, or without its own risk profile, but it does appear there will be more workers using a lot less paper in biomanufacturing.
---------
We’ll continue our discussion about students and training in biomanufacturing, in a second article with Gary Gilleskie, Ph.D., director of operations for North Carolina State University’s Golden LEAF Biomanufacturing Training and Education Center (BTEC).