Creative Outsourcing Strategies, But Fill-Finish Still A Concern

By Louis Garguilo, Chief Editor, Outsourced Pharma
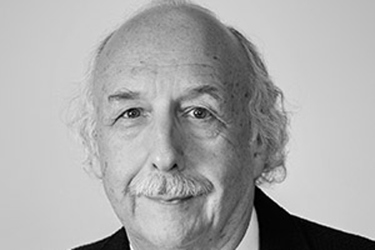
Thomas Rademacher, Emeritus Professor at University College London (UCL), historic biotech entrepreneur, and co-founder and CEO of Emergex Vaccines, a biotech whose T cell platform is “the next step forward from mRNA vaccines,” knows a lot about strategic and tactical outsourcing.
Nonetheless, in October of 2022, Emergex purchased a facility from the former Zosano Pharma Corporation (located in Fremont, California) to capture specific technologies and a mid-sized manufacturing platform.
That purchase adds to both the specialized small-scale equipment already utilized at Emergex's modest development labs in the U.K., where the biotech is headquartered, and is part of Rademacher's aforementioned strategic outsourcing – at a single CDMO, and a number of specialized fill-finish service providers (more on this below).
Mix And Match
Rademacher, as he tends to do, backs us up before we get to our main subject of this final editorial in our series (earlier editorials are listed below).
His most intensified focus at this moment is on staffing and integrating the newly acquired facility for the development of Emergex’s novel microneedle-delivered, T cell-priming vaccines. “That will be our commercial manufacturing facility,” Rademacher says.
Then regarding the development that has already propelled his proprietary platform around the world (see part one and part two), he particularly points to his still sub-40-employee organization having purchased and utilized “these fantastic SteriCUBES [multi-tray sterilization system],” providing internal manufacturing capability up through Phase I and II.”
And as earlier reported, Emergex outsources today to a single CDMO, Ardena, employing its Holland-based facilities. There’s a defined objective to this relationship.
“We needed to get somebody trained in the manufacturing tech-transfer process, and that can do Phase III and commercial manufacturing if in fact we don't get it going ourselves, or if we move quickly into a Phase III and need capacity fast.”
“We need a backstop; they have actually made a couple of our clinical batches.”
And with that laid down as sufficient segue, Rademacher moves us to a discussion on sterile fill-finish, all of which he outsources.
Excuse My Nomenclature
For a brief moment, Rademacher and I talk past each other. He mentions other external production partners.
So you do utilize other CDMOs besides Ardina? I ask for clarification.
“No, those others are fill-and-finish facilities and specialists,” he replies.
Broadly speaking, I kind of count fill-finish facilities as CDMOs.
“Well, we count them very differently,” retorts the entrepreneur-professor.
“We provide drug product, and they provide all fill-and-finish support.”
That support, he says, has included locations in the U.K., Scotland, and California, among others.
“As you know,” he adds, “there was a huge shortage of fill-and-finish during the COVID years,” a major holdup impacting various activities. In an attempt at mitigation, Emergex spread itself out at a number of facilities. Rademacher says that strategy ended up working quite nicely.
“These different sites have to maintain our vials for quite a long period of time, and we can always go in and utilize those, so it's quite nice.”
The direct catalyst to the spreading out of facilities, though, was not so pleasant.
“We did so, I have to say, because we've been bumped by fill-finish service providers.”
And like so many others, he has been forced to book production dates many months ahead of time.
“It’s like a big game you play,” Rademacher says, “because there aren’t many providers that want to make the smaller number of vials we require for a Phase I or II project.”
“Many facilities are looking for a Moderna-like contract, if you know what I mean. We have actually been bumped the day before we were scheduled to start production. A new customer came in with a bigger checkbook, it appears. I won’t name the service provider, although it is well-known.
“The delay was six weeks. However," he adds, "my team has been smart about how to handle this.”
The broader application here for readers is first, fill-finish bottlenecks continue to linger, particularly for smaller biotechs, and especially for the growing number of vaccine start-ups and developers since COVID disrupted the demand-supply balance (and also set folks into a more frenzied vaccine-development mode).
As these pages have documented, along with their frustration at times, vaccine sponsors today attempt to mitigate fill-finish challenges with outsourcing strategies such as:
- utilizing right-sized and various facilities;
- relationship building;
- laying down pre-production payments;
- having one's own house in order to ensure you are a good customer.
(Having a nation build a mammoth fill-finish facility to handle your needs may be quite a unique solution, as we saw in earlier editorials.)
But as for the CDMOs – make that fill-and-finish specialists – they insist that delays, if they occur, have been condensed.
Perhaps.
But we’ll continue to document for and with readers the veracity of those claims.
Microneedle Needed Dedication
Finally, as we leave this multi-editorial journey with Professor Rademacher, and I look over past installments, I feel I’ve not done an adequate job of describing the production facility Emergex purchased last year, which feeds those fill-finish partners.
Emergex bought the 55,000 square-foot Zosano facility in California because the T cell vaccine technology Emergex is developing is based on microneedle delivery.
“So we are also device-associated,” says Rademacher. (Currently, Emergex employs “hollow microneedles,” purchased from NanoPass in Israel, but Rademacher is also currently looking for a U.S. supplier).
Zosano had created a way to put an Emergex vaccine on a dry patch, “and that's why actually we took them over,” Rademacher says.
“Basically, we want to administer all our vaccines as dry patches. Eventually, we will move completely away from liquid administration to dry-patch administration. We are fortunate in being able to keep the original founder of Zosano, and other key staff."
He adds, "Put it this way: they all love being there."
“Originally, we were set up to do drug delivery on the patches – intended for treatment of migraines and things like that. But it needed to be repurposed, because if you follow the vaccine world, we are moving into these skin immunizations.”
He makes sure I understand he is specifically talking about “epidermal, not even to the dermis.”
For vaccines to work like the ones Emergex develops, they must be administered to the epidermal skin layer, "like at 300 microns." Zosano had the technology to do that, and "that technology is actually more applicable to vaccine delivery than it was to drug delivery."
"So we're very fortunate, I have to say,” concludes Rademacher.
Ultimately fortunate, we'll say, if he can fit together all the pieces that make up the Emergex strategies, applied in the broadest of global terms, and in so doing advancing the entire vaccine industry.
---------------
Also read:
Vaccine Manufacture From The U.K. to Brazil And Saudi Arabia