CPhI Report: For Manufacturing "Process" Or "Quality," It's Statistical Control
By Louis Garguilo, Chief Editor, Outsourced Pharma
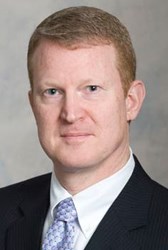
According to a new report entitled CPhI Pharma Insights, pharma needs to drive manufacturing forward, and advancements should come from within companies, not from the outside push of regulatory bodies. Advancements coming from within will lead to lower costs and improved quality. When the advancements are pushed from the outside, they can keep prices high and hurt efficiencies.
The report, based on a cross-section of industry participants in a survey on manufacturing, is a succinct read and analysis of the current state and future needs in this segment of the pharmaceutical industry. What with recent and very publicized quality-related challenges in manufacturing – both at outsourced plants and internal facilities – it would have been surprising if quality hadn’t come out in the survey as the top focus for pharma. Indeed, “improving product quality” was ranked number one.
Interestingly, although this shouldn’t be surprising either, “improving product quality” tied for first with “reducing manufacturing costs.” Take a moment to ponder that: improve quality and reduce costs. Some suggest these factors might be mutually exclusive, at least at the onset of a quality program. Producing a quality product obviously requires some investment. In the CPhI report, Girish Malhotra, panel member and President at EPCOT International, addresses this. “However, the drive to cut corners without proper processes in place has been the cause of some quality issues that have been surfacing across the industry.”
This shouldn’t be about cutting corners. What resonates most for us in the report is this focus on the need for “proper processes.” Specifically, those surveyed reported the tool they will most employ to affect “continuous improvement” is Statistical Process Control. Readers of our recent article in Outsourced Pharma know we discussed just such an application to the pharmaceutical industry’s manufacturing challenges via the thoughts of Edward W. Deming, an evangelist of Statistical Quality Control.
Which of the following tools are you using for continuous improvement? (CPhI Pharm Insights; April 2014)
Other interesting findings in the CPhI Pharma Insight survey – which included brand-name pharma, contract API, generics, ingredients and other manufacturers – is that the outsourcing of manufacturing will continue to play a major and growing role in the pharmaceutical industry. According to the report, “41% said that they are outsourcing more of their manufacturing to other organizations.” This corroborates other surveys and ample anecdotal evidence suggesting contract development and manufacturing continues to be a healthy and growing business sector. Overall, 70% of those in the survey said they were “investing in manufacturing this year.”
Summing up the key ingredients of the report as we see it, we have (1) the recognition that quality improvement and reducing manufacturing costs are the most important goals to organizations; (2) more planned outsourcing, (3) more money (investment), and finally (4) a move to “statistical process control” as a major tool to make it all work out. Sounds like we need to get back to Deming for a moment.
Statistical Process and Quality Control
After publishing our recent article mentioning Dr. Deming, consultant John Hunter contacted Outsourced Pharma via Twitter (@curiouscat_com) to inform us that The Deming Management Method and Statistical Quality Control are indeed alive and well, and are being applied to quality management around the world. In the CPhI report, Malhotra seems to channel Dr. Deming as he continues his statement above: If “companies had the complete command of the (manufacturing) process from inception, quality might not become an issue and overall costs would be lowered.”
In fact, statistical process control and capability analysis (ranking second as a tool of continuous improvement in the accompanying chart) and the correct application of both should successfully bind the goals of gaining quality and reducing production costs. If pursued correctly, this is the path. The concern is who leads the company down this road of quality and cost improvement. Herein lies the Deming caution.
Deming says management – not workers, equipment or even the unknowables, which by the way tend to be more influential than that which is known about a process – is the key to the success of statistical controls for the improvement of quality and raising of profitability. Issues arise when there is a lack of control, which can be thought of as allowing influences that negatively impact on the ability of the process to maintain a “steady state.” Ultimately, those controls are a function of management at all levels.
Nary a word about management appears in the CPhI report. That may not be cause for concern on its own, but in light of this discussion, certainly worth noting. Deming called for the enlistment of all managers in a “System of Profound Knowledge.” One part of that knowledge is in the “appreciation of a system” by gaining a holistic understanding of the overall processes involving suppliers, producers, and ultimately customers before utilizing any statistical analysis to affect change.
The CPhI report specifically queried manufacturers on whether they “Test all raw materials sourced to your facility?” Eighty-nine percent said yes and 11% said no. The report takes this as a negative response for the cause of quality. This might be a rash assessment. The survey group was broad, and while those performing production under cGMP and regulated conditions must undertake sampling upon receipt (we won’t get into sampling methodology here, although the report does), it is not needed in all cases. Deming would agree, and take it one step further: Limit the number of suppliers (he suggested go with one!) of your materials, work with them side-by-side as a full partner on the continuous improvement of their product and processes; show them the effects that in-spec but minor deviations can have on final product.
On this same item regarding producer-supplier relationships, the report opines “11% of respondents stated they do not test all incoming raw materials sourced to their facilities, despite almost half of all respondents claiming they connect with suppliers weekly.” The positive and the negative in this statement might be taken in reverse. In light of our immediate discussion it could be asked: Why aren’t even half of the producers in closer contact with their suppliers?
Finally, if anyone is wondering, the opportunity to utilize this thought-provoking CPhI report to follow up on the Deming article of a few weeks ago served well, but we’ll now leave Dr. Deming for others to discuss. Happy reading of both sources.