4 Concepts For Supply Chains And Your Good Supply Practices (GSPs)

By Louis Garguilo, Chief Editor, Outsourced Pharma
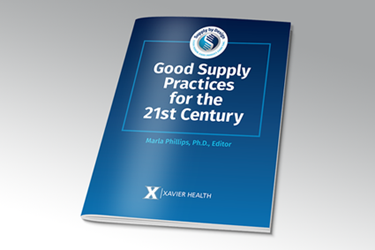
The full “Good Supply Practices for the 21st Century” research report is out – 150-plus pages of supply-chain guidance. Many of us have anticipated for years this grand finale, spearheaded by Xavier Health.
Back in 2015, I wrote this of what became a 6-year process to get to the bottom of how the pharma industry can improve its supply chain and partnerships:
“It’s like a scene from a Brothers Grimm folk tale. One late afternoon at an industry conference, a cross section of biopharmaceutical leaders gather in a room to take a hard look into a large mirror. It reflects that they — not their suppliers or service providers, as was assumed — are culpable for, and thus can control, many of the product reliability problems in their supply chains.”
Since that self-revelation, an eclectic group including from Abbott, Boston Scientific, Cook, Eli Lilly, the FDA, Johnson & Johnson, Kroger, Merck, P&G, Patheon, Shire and Takeda, methodically worked on making this industry analysis both comprehensive in scope, and a practical blueprint for any biotech or pharma with a supply chain.
The Fantastic Four
According to Marla Phillips, Director, Xavier Health, in the Executive Summary to the newly released report:
“Based upon the discovery that the true root cause of supply chain failure starts internally within the buyer’s organization, Xavier Health led a team of FDA officials, pharmaceutical professionals, medical device professionals and supplier representatives from 2012 – 2018 to develop four new supply chain concepts that significantly improve supply chain performance for companies of all sizes and complexity.”
Those “concepts” are embodied in Good Supply Practices (GSPs) that set out and govern supply-chain behaviors. According to the report, “The Good Supply Practices (GSPs) establish a holistic approach to sourcing and supply chain operations that supports patient and business success by reducing risk to internal and external stakeholders throughout the total product lifecycle.” (The GSPs are listed below.)
Four New Concepts
Here the concepts as described in the report.
(1) Supply-by-Design (SbD): The Good Supply Practices in their entirety are grounded in the concept of Supply-by-Design, which protects product quality through an intentional design of the supply chain and minimizes unexpected risk by taking actions commensurate with the need. Each solution provided in the Good Supply Practices is a way in which to execute Supply-by-Design.
(2) Cross-Functional Alignment: Gaining internal alignment (i.e. true alignment, not siloed hand-offs) across diverse competing priorities will increase the assurance of patient and business success. The GSPs provide a practical approach to identifying and addressing conflict goals, which is critical to achieving alignment.
(3) Self-Qualification: If companies are causing or could prevent all supply chain failure, then the questions must be: “How qualified are we to be in this relationship? What risks does this create? How can the risks be mitigated?”, which takes companies beyond the one-dimensional approach of supplier qualification.
(4) Relationship Risk Mapping: Since all relationships involve more than one entity, then only the overlay of strengths and weaknesses from all entities involved will create an understanding of total relationship risk and enable the company to mitigate weaknesses from both sides. In some cases, different products or processes from the same supplier can create different risks.
The GSPs themselves are summarized as:
- Setting the Foundation
- Cross-Functional Team Formation
- Self-Qualification
- Knowledge Management
- Supply Chain Risk Management
- Internal Alignment
- Material Requirements
- Supplier Requirements
- Single Source vs. Multi-Source
- Communication Strategy
- External Alignment
- Supplier Engagement
- Holistic Supplier Qualification
- Relationship Risk Mapping
- Lifecycle Management
According to Jack S Solomon, Head of Supply Chain Services, Core Risks Ltd., and one of the reports three “GSP Co-Leaders” (along with above-mentioned Phillips, Director, Xavier Health, Xavier University, and Troy Fugate, Vice President, Operations, Compliance Insight):
“Feedback from early adopters of the Good Supply Practices (GSPs) supports the expectations that adherence to the guidelines will improve compliance, improve profit, reduce risks to patients and the business, and can improve speed to filing/market, as well as many other benefits.
“These GSPs provide for improved and defendable prioritization, and reduced cost related to Supplier relationships based on holistic review of a broader information pool. Everything starts with the right people in the team, by exchanging and using the correct information for creating a product and services. Driven by the market and the customer.”
The importance of this collaborative report should be obvious.
For example, according to the website, drugwatch, “On average, about 4,500 drugs and devices are pulled from U.S. shelves each year.” Stericycle Expert Solutions reported that in Q2 2019, “19.5% of pharmaceutical recalls were due to failed specs.” And Medical Tracking Solutions states on its website: “Costs of a single non-routine quality event, like a major recall, have been as high as $600 million in medical device companies.”
So if you didn’t know, the stakes are high and failures not rare enough. Concepts culled from best practices – or new practices to some – should benefit the industry, and of course patients.
One For The Road
If I were to select one of the four concepts identified above to focus on – and it’s a difficult choice because readers will know all are worth a deeper dive – it would be the initial, Supply-by-Design (SbD).
Nowadays, it seems any “by design” label catches the collective biopharma fancy (see here for an example on organizational design and data integrity.) This one should, too.
Illustrated in the top section of Figure 1.1 below, today’s supply chains are still mostly developed through a “series of disjointed silo-ed hand-offs,” which then require “exhaustive resources to mitigate supplier and material failures,” says the report.
“Conversely, an intentional supply-by-design (SbD) approach is taken through the GSP processes that is accomplished through cross-functional alignment on material and supplier requirements, which results in reduced failure, cost and risk. This right-first-time approach through cross-functional alignment is a key differentiator of the GSP work.”
Figure 1.1: Comparison of Supply Chain Development Model Effectiveness
Solomon further explains the findings:
“The team’s research suggests that many companies have robust procedures on file, and many companies have Missions and Visions that indicate the leaders believe these procedures are being followed. However, conflicting goals are impeding alignment, and companies are paying the price. Therefore, the first step is to establish teams and reach alignment.”
That alignment on a “holistic view of impact” includes:
- Patient safety and efficacy
- Quality and compliance
- Product availability
- Business impact
- Employee safety
- Environment/public
Outsourced Pharma readers who’d like to set down and then put their GSPs in motion, practice the core concepts that surround that effort, and align both internally and externally for a more successful supply-chain experience, might want to look over this well-worth-the-wait report.