To Thrive In A Highly Regulated Manufacturing Environment, Improve Your Flexibility
By Nero Haralalka, director, TBM Consulting Group
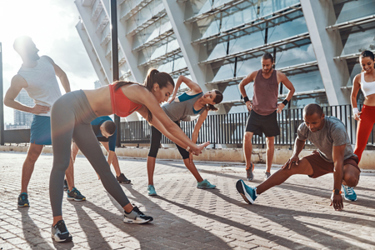
It sounds counterintuitive. After all, the whole point of regulations is to put (often rigid) rules into place to govern manufacturing processes and ultimately protect the integrity, efficacy, and safety of regulated products, such as pharmaceuticals and medical devices.
Clearly, this is a critical goal. The problem is that adherence to regulations often creates a mindset among manufacturing leaders that results in a form of tunnel vision and a reluctance to challenge the status quo. Performance improvement opportunities go overlooked. This can end up hamstringing a manufacturer’s ability to pursue process improvements that lead to breakthroughs in performance that enhance both the top and bottom line. And it can jeopardize a manufacturer’s ability to respond to changes and challenges in the industry as they arise.
Disruption Is An Ever-present Possibility
The current situation with phenylephrine as an ingredient in over-the-counter drugs is a case in point. With CVS already pulling certain products from its shelves and the potential for other retailers to follow suit, demand is taking a hit. Should the FDA decide to declassify the ingredient and remove it from the over-the-counter monograph, the operational and financial implications for the manufacturers of those products being pulled (Sudafed, for example) will be enormous, with wide-reaching impact on facilities, warehouses, inventories, equipment and tooling, and the overall supply chain.
The pharmaceutical manufacturers best positioned to weather the ensuing fallout from the phenylephrine situation, or from any other potential regulatory issue or industry disruptor on the horizon, are those that have found ways to build flexibility into their processes while continuing to ensure products are manufactured according to stringent specifications. Interestingly, achieving flexibility within a highly regulated environment is very often the result of adopting additional process discipline — the kind that makes manufacturers more efficient and agile as opposed to more rigid and resistant to change.
Agility Allows Manufacturers To Go In A Different Direction When Needed
Creating more agile operations allows leaders to pivot quickly and take advantage of new opportunities when the situation changes either expectedly or unexpectedly. This could mean squeezing out waste and costs from existing processes to minimize the financial impact of a lost product line. It also can lead to developing enhanced capabilities to quote and introduce new products and drive revenue from other sources. And it can position companies to serve customers faster and better to improve timely deliveries, eliminate backlog, optimize inventory, and potentially take share from competitors.
Reducing Changeover Times Is A Great Place To Start
One area where pharmaceutical manufacturers are notoriously reluctant to consider new approaches is in the physical changeover of high-volume production lines. Most companies have complex and highly regulated processes to ensure product quality and regulatory compliance. Almost always, these processes can be dramatically streamlined, primarily through improved coordination between different departments and the application of lean principles like SMED (single minute exchange of die) to eliminate dead time in the process.
Sometimes, better collaboration and lean techniques can cut changeover time by 50% to 75% or more with no effect on product quality. Manufacturers can simultaneously work to execute their batch records in real time instead of pausing production to complete the required regulatory paperwork. Recordkeeping, material verification, and in-process testing are just a few of the steps that can be documented as they are happening on the plant floor.
These efforts enable manufacturers to continue meeting regulations while freeing up significant production capacity and cutting costs. In one example, a manufacturer that implemented physical changeover reduction and real-time batch record processing side-by-side dramatically reduced idle labor time, creating additional capacity with a material margin and labor cost reduction of $3.4 million. In such scenarios, companies become much more agile and able to address backlogs, improve on-time delivery, or take on new product lines to drive growth. This puts them in a much better position both financially and operationally to adjust and respond to external events and influences, such as a major change to the OTC monograph.
A Solid Maintenance Plan Keeps Options Open
Freeing up capacity on high-speed, capital-intensive lines can make companies more flexible and responsive, as long as those lines reliably stay up and running. It’s not uncommon for pharmaceutical or biologics manufacturing facilities to operate only a handful of such lines given the extraordinary expense of the equipment. So, properly maintaining the lines is even more paramount to ensuring equipment availability and production.
While the financial implications of equipment problems vary based on the site and complexity of the line, most companies can quantify the cost of an hour of unplanned downtime by adding underutilized labor costs to loss in profit due to reduced or no output from the line. It can amount to thousands of dollars per hour and hundreds of thousands to millions of dollars per year.
Pharmaceutical manufacturers interested in maintenance excellence should start by identifying critical maintenance KPIs and implementing processes for monitoring these metrics. One such metric is overall equipment effectiveness, or OEE, which is the product of uptime, performance, and quality. For world-class companies, uptime is 95% or higher and is a direct reflection of a maintenance excellence approach. Companies that keep tabs on such measures lay the foundation for evolving from a reactive approach to maintenance to a preventive and, ultimately, a predictive maintenance approach that integrates autonomous maintenance capabilities. True maintenance excellence also involves the right leadership commitment as well as the integration of equipment availability and other data to tap into full equipment capacity.
Creating A Problem-Solving Culture Drives Greater Productivity
Exceptional talent is a hallmark of flexible and responsive organizations that can respond well to any type of challenge. Manufacturers can build the capabilities of their people by intentionally establishing a problem-solving culture.
In a problem-solving culture, people at all levels are accountable for performance and empowered to take action to investigate root causes of reoccurring misses and put action plans in place to resolve the inefficiencies before the bottom line takes a big hit. Instead of centralizing decision-making with upper-level supervisors or managers, which delays resolutions, compounds financial losses, and leads to workforce frustration, everyone is involved in continuously course correcting and driving toward daily KPIs and financial targets.
Such a problem-solving environment not only improves productivity with a focus on financial progress and customer satisfaction, it also can go a long way toward employee satisfaction and retention, helping organizations hold onto their best and most motivated people.
Implementing A Formal Management System Sustains Process And Behavioral Changes
Every organization has a management system, or a way in which work gets done, whether it’s formalized or not. On the surface, formalizing processes seems like it would introduce more rigidity into an organization. But the opposite is in fact true.
Indeed, a management system is the key to sustaining the flexibility ushered in by new process efficiencies. A management system aligns daily business activities with a manufacturer’s long-term strategic objectives and cascades goals and KPIs throughout all levels of the organization, ensuring that all stakeholders can make faster and better business decisions that keep the company’s performance on track. In one major pharmaceutical manufacturing operation (one of our clients, though we are not naming the company), the implementation of a management system led to a rapid 17% surge in productivity, allowing the company to completely eliminate its backlog within six months while reducing direct labor cost per unit and slashing inventory by 13%.
When circumstances change or the strategic direction shifts, manufacturers with a well-defined management system in place have the framework to keep everyone aligned around what most matters to the organization’s ongoing success. The organization can more easily respond to needed changes because people are already in the habit of staying focused on the critical KPIs, consistently tracking progress against those indicators, and responding immediately when performance is off track.
Meet Regulations And Financial Progress With A More Flexible Approach
In highly regulated manufacturing environments, the ability to closely adhere to specifications matters. But the ability to adapt quickly when the business environment changes may matter even more. Most manufacturers have tremendous opportunities to build more flexibility into their processes that will improve responsiveness to current and future challenges. The key is creating the kind of process discipline that introduces the efficiency and agility to meet regulations in the most productive and profitable ways.
About The Author:
Nero Haralalka is director, US Consulting, at TBM Consulting Group. He is a Lean Sigma Master Black Belt with 35 years of experience in the areas of operational excellence, product development, statistical modeling (including the use of AI), and root cause problem solving. Haralalka has a master’s degree in mechanical engineering from the Illinois Institute of Technology in Chicago and a B.S. in mechanical engineering from the Birla Institute of Technology in Ranchi, India. He also has AAMI QSR Certification.