3 Tips To Get The Best Bang For Your Mock Inspection Buck
By Penelope Przekop, MSQA, RQAP-GCP
Many sponsors and CROs conduct mock inspections to determine organizational inspection and audit readiness. Investing in a regulatory mock inspection demonstrates a serious commitment to patient safety, data integrity, and regulatory compliance. It is also a proactive strategy to safeguard financial health, particularly for startups and companies with sparse pipelines.
Throughout my career, I’ve had the opportunity to identify several common mistakes that cost companies exorbitant amounts of time during mocks. These hinder everyone involved from focusing on gaps that may be more difficult to identify and more damaging if not remediated.
The primary goal of a mock is to identify gaps prior to an actual inspection. Most mocks take place over a three- to five-day period. Don’t waste everyone’s time and company funds wading through issues caused by failing to understand the “no-brainers” outlined below. Addressing these commonly overlooked or little-understood items often sucks up an entire day! Take the time to ensure they are addressed prior to the mock, enabling mock inspectors to use their time on-site more effectively.
The lowest hanging fruit that companies can proactively “pick” (and get out of the way) prior to a mock fall into these buckets:
- People
- Preparation
- Process
Considering these categories, the top three ways to get the best bang for your mock inspection buck are:
1. Put the right people in the right roles.
Select a QA mock facilitator who has the appropriate experience and skill set. This is usually a QA professional with solid, proven experience in the regulatory focus area (e.g., GCP, PV, GMP), including inspection and auditing experience. The facilitator should have an excellent understanding of the company structure, the drug development process, the company’s document management system, and how the key elements dovetail to support the quality system and the clinical development process. This seems to be a common challenge for small to midsize companies as well as larger companies shifting from a focus on manufacturing to clinical development.
Also, be careful to hire QA staff with experience relevant to the company goals. I often see, for example, QA professionals who have many years of GMP experience managing and directing GCP processes and subsequently facilitating GCP-focused mocks and inspections.
Select subject matter experts (SMEs) who can provide the appropriate level of detail during mock interviews. Two common mistakes are bringing in an SME who:
- manages only a specific element of the discussion topic
- has high-level oversight but is not highly experienced in the discussion topic.
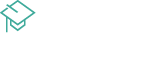
Be Audit ready! Get expert advice directly from Penelope in her webinar:
Mock Regulatory Inspections: How to Get the Best Bang for Your Buck.
This can be avoided by ensuring the mock inspection plan or agenda is fully understood and by selecting SMEs for each topic who can engage in a highly relevant discussion with the inspector.
2. Appropriately prepare your team and documentation.
Companies create any number of strategies to ensure inspection readiness. Many provide direct inspection-readiness training for management and other key SMEs. This includes classroom training on the inspection process, mock interviews, SOP refresher training, and communication tips. Some companies invest in a regulatory mock inspection as an avenue for employee training and identification of gaps.
Don’t make the mistake of using your mock inspection as your only training activity. Having a mock does not mean you should skip inspection-readiness training. While a mock is an excellent training exercise, the more important goal is to identify existing regulatory, process, and documentation gaps.
Provide as much training as possible prior to the mock. This will enable the mock inspector to quickly identify employees who may be more challenged in an inspection. It will also help the company execute the appropriate, industry standard inspection process, saving valuable time. Everyone should know what they are expected to do during an inspection, why it’s important, and how to best execute their tasks.
When selecting and preparing QA staff and SMEs for the mock, remember good communication is not only about what you say or do not say to an inspector. It’s also about listening. Poor listening skills often result in miscommunication that wastes time.
Using a mock to determine if an internally identified gap will go unnoticed is not a good strategy or use of time and money. Management or QA can let the mock inspector know about areas of key concern when planning the mock. Staff involved should proactively prepare documentation, storyboards, and even presentations to address known gaps and be prepared to present the information when asked. This allows the inspector to provide feedback, not only on the gap, but on how you have chosen to address it during a real inspection. Don’t waste time having the inspector find the gap, leading to lengthy discussions on how best to address it during an actual inspection. Instead, give them time to identify gaps you don’t know about!
3. Follow the industry standard inspection process.
Regulatory inspectors are people, too. They develop their own inspection style, yet there are common expectations across the board. If your company doesn’t know what these are, a red flag begins to fly. During a mock, this scenario quickly turns the focus to training rather than gap identification, sucking up valuable time.
Have a presentation ready that includes high-level information on:
- company background
- clinical development process and status
- electronic systems used
- the quality system and QA organization
- vendors used
- inspection history.
Be prepared to provide commonly requested items such as an SOP Index, SOPs that include approval documentation, training records, and staff qualifications. Know where every section of your trial master file (TMF) is and how to obtain requested documents, even if the TMF is spread throughout the globe or a study was conducted five years ago. Have all documentation regarding serious breaches, noncompliance, protocol deviations, monitoring, auditing, etc. at your fingertips regardless of any outsourcing scenario. As the sponsor, you will be required to provide it. Lastly, inform your key vendors of the mock. They may be called to an interview.
Do not assume your company can forego a backroom hub, QA review of requested documents, runner, or scribe during both a mock and real inspection. Even in a small company, one person cannot cover the necessary roles and tasks required for a successful inspection.
In conclusion, depending on your level of experience, you may not take my advice seriously. You may think, “Wow, these things are no-brainers. Why is she telling me this?” Congratulations! You and your company may be on the right path. However, don’t assume that’s the case for everyone and every company. Time is wasted repeatedly on the items discussed above. Proactively closing this gap gives companies more mock inspection bang for their buck on multiple levels.
About The Author:
Penelope Przekop, MSQA, RQAP-GCP, is a quality management systems, assurance, and compliance consultant with 25+ years of experience in pharmaceutical GxP global quality systems with a key focus on clinical development, data management, and pharmacovigilance. Her areas of expertise include quality systems, quality assurance, regulatory compliance, inspection readiness, training, and strategic planning.
Przekop earned a B.S. in biological sciences from Louisiana State University and an M.S. in quality assurance/systems engineering from Kennesaw State University. She has held leadership positions in both Big Pharma and CROs, including Johnson & Johnson, Wyeth Pharmaceuticals, Novartis, and Covance. You can connect with her on LinkedIn.