Takeda Cut Its PPQ Timeline With beePFS — Here's How
A conversation with Roland Fabris, Takeda in Linz
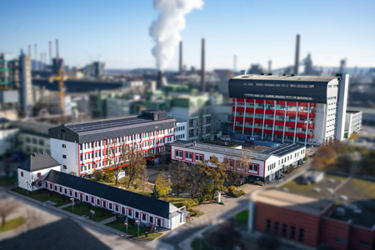
Vedolizumab producer Takeda believed the irritable bowel syndrome drug could reach more patients in a prefilled syringe. It also believed that, despite a global pandemic, it could complete a new filling facility within its Linz, Austria, site faster than the industry standard and still include the latest equipment and training technology.
Takeda completed all process performance qualification (PPQ) runs within 24 months, or 50% faster than standard projects of a similar scope within the company and the industry, according to the company.
ISPE will recognize the companyat the 2024 Facility of the Year Awards (FOYA) Banquet and Awards Celebration at the 2024 ISPE Annual Meeting & Expo in Orlando later this year. Takeda's beePFS project won the FOYA in the Operations — Facility Fit category.
We asked Takeda in Linz Managing Director and Site Head Roland Fabris a few questions about the build to get a better sense of the company's approach and how the team executed on their ambitious goals.
What was entailed in the beePFS project and what led to it?
The beePFS filling line produces a treatment for patients with chronic inflammatory bowel diseases. We knew if we could add a production line of this kind with its capabilities we’d be able to help many more patients around the world. With prefilled syringes, patients benefit from a safer (i.e., prefilled doses) and flexible administration — patients can treat themselves outside a hospital setting under the guidance and oversight of their physician. This was especially critical during the pandemic when we tried to limit hospital treatments to emergency-only visits.
The “bee” in the name is a nod to our worker bee culture at the Linz site. Just like productive bees working in a beehive, everyone was working hard within their roles toward one common goal, which is the patient in this case. At Takeda, our top priorities are patients, our people, and the planet.
This mentality extends beyond the beePFS filling line. For example, the line is in the middle of a chemical park surrounded by tall grass that we used to trim weekly — until we discovered the grass is home to a species of an endangered frog. We adjusted our grounds maintenance to keep the grass tall so the amphibians can survive and reestablish their population. We try to be role models within our industry and beyond.
Can you describe some of the process improvements Takeda in Linz undertook that enabled a 50% reduction in the time to execution compared to standard projects?
The beePFS was part of Takeda's Super-Fast Track WARP Speed program that challenges the industry norm for production line timelines to accelerate development. Post-COVID supply chain challenges were a major motivator behind the construction of beePFS — once built it would strengthen our supply chain resilience in sterile syringe filling. This type of program is important in the wake of important drug discoveries or global health events so that we’re equipped to deliver medicine faster when it matters most.
To put it into perspective, a typical PFS line construction would take around 50 months on average, which is roughly four years. That’s a long time for a patient in need. So, as part of the program, our team members brainstormed what we could do to accelerate the development.
At the end of the day, there was no secret formula but rather a great deal of hard work and intricate coordination. We tried to layer as many processes on top of one another as possible, like developing our plan based on products that had the longest lead time, for example. We empowered our team to make decisions and have a solution-seeking mentality. We held project team meetings every single day for 30 minutes where we would make sure everyone was on the same page, and if they weren’t we’d discuss how to get them there.
A challenging area was coordinating with suppliers because they’re often used to linear timelines, but we were operating in parallel with so many other departments. Communication — and really taking the time to explain our program and approach — was also key here.
Pre-use, post-sterilization integrity testing (PUPSIT) has been a burden for many companies, but Takeda in Linz claims to have integrated it "seamlessly." How?
PUPSIT integration was a new mandate from the Austrian AGES authority (2023) that ensures swift reaction times for sterile filter integrity tests. It’s a crucial validation step. The interesting part about this mandate is that it’s left up to the team to determine how they want to validate — and there are a lot of options. We ultimately went in the single use direction as opposed to using an isolator, as it is more secure for the patient. It wasn’t an easy install, but we passed without issues and we’re very proud of this.
Can you talk about some of the advanced technology Takeda rolled out and the strategy behind choosing it?
If you’re not transforming, you’re falling behind — this is something our team takes very seriously. Through this commitment to innovate, we brought several cutting-edge technologies to beePFS and are always looking to integrate more.
For training, we leveraged augmented reality (AR), which provided a realistic, risk-free environment for our operators. We utilized a manufacturing execution system (MES) and historian system to help release the product faster. Our use of AI, ML, and other automated systems continues to help us collect incredible amounts of data required to be agile, adapt, and improve our processes.
We tried to automate wherever possible due to efficiency, safety, but also sustainability. The filling line is paperless, which simplifies data collection, we installed photovoltaic power systems, we reduced freshwater consumption, and we’re driving down CO2 emissions with optimized transport modes, for instance. In doing this, we can contribute more to patients on every level.
What lessons here are transferrable? In other words, how can the successes with beePFS spin forward to improve execution and timelines in other projects?
Keys here were speed and communication. Pharmaceutical companies don’t always need to tear down and build a new production line from scratch. beePFS is proof you can conserve the shell, retrofit with speed, and renovate existing builds.
Having the right people in the right place was also vital. We prioritized internal development of team members, which is something I’m particularly proud of. We empowered everyone to be a leader and they rose to the occasion. Coming away from this project, it’s clear that beePFS was a success because of the way we worked together, the on-site attitudes, and the mindset of the team. We didn’t work off a playbook.
In short, the construction of the beePFS line showed us what we’re capable of — in a sense, it felt like making Mission Impossible possible.
Editor’s note: Life Science Connect and ISPE are collaborating to explore the winning strategies behind select 2024 FOYA winners. Learn more about the awards.
About The Expert:
Roland Fabris is managing director and site head of Takeda in Linz, Austria. He's worked for the company since 2010. He received his undergraduate degree in mechanical engineering from TU Wien and an MBA from the University of Pittsburgh Katz Graduate School of Business Administration.