Responding To Regulatory Inspection Observations: Do's and Don'ts
By Martin Lush, VP of Health Sciences, NSF International
It’s Friday, it’s late, and you are just leaving for the weekend. The inspection you hosted two weeks ago remains a painful memory. The exit meeting didn’t go well — five major observations, all relating to your quality system. When your boss enters your office, you know it’s not to wish you a good weekend. She looks stressed, anxious, and keen to off-load a big problem …
“We’ve received the regulator’s audit report. We now have one critical and seven majors, and we have 15 days to respond in writing. Our license to operate is at risk. Cancel your weekend. I need the draft response by Tuesday.”
First Steps
Acknowledge receipt of the report immediately. Be respectful and polite, never defensive. Keep this immediate communication short and to the point. Commit to providing a comprehensive response within the expected time frame. Emphasize your total commitment to fixing the underlying causes and to addressing any immediate risks … and then leave for the weekend! This is not a frivolous point. So many responses are written by people who are tired, stressed, and just not thinking straight. Take time to think before putting pen to paper.
Get Back To Basics — Your Primary Objective
In writing the audit report, the regulator is (subconsciously) expressing one or two emotions: fear over patient safety and/or lack of trust and confidence in your company. Your primary objective is to remove both.
Fear: The auditor’s primary objective is to safeguard public health. A damaging audit report means they have concerns about your company’s ability to manufacture products that are safe, efficacious, and of the right quality. This may be due to specific observations or just a feeling that systems, procedures, or practices are not in a state of control.
Lack of trust and confidence: Poor inspections quickly erode trust and confidence between the regulator and your company. The relationship between company and agency has been badly damaged. Remember, auditors are human! Although good auditors base conclusions on facts, emotions will play an important role in how they perceive your company, your leadership, and your quality culture. This is not a precise process, and cultural differences can often sabotage good intent. These cultural differences can easily lead to miscommunication and misunderstanding that then create the feeling of distrust. If you did any of the following during an inspection, you have eroded the most crucial element of any successful inspection, trust:
- Not answering questions clearly
- Not providing documents quickly or using delaying tactics in general
- Attempting to justify bad practices using risk assessment
- Appearing to hide bad data
- Lack of transparency
- Putting barriers in front of the inspector
- Management answering all of the questions
So, when responding to regulatory criticism, remember:
- Your primary objective is to rebuild trust and remove fear. Don’t just focus on providing data and information.
- Accept that rebuilding trust and removing fear takes time, often years. Be consistent and genuine in your messaging. Don’t attempt to fake it.
- Even if you feel you have been treated poorly or misunderstood, or the inspector was just having a bad day, remember: The perception of the inspector is reality, particularly when it’s in writing. Companies that feel victimized or unfairly treated often respond emotionally, making the situation worse.
Before writing to the regulators, remember the essentials:
- Avoid the victim mind-set. Whether you like it or not, inspector perception is reality.
- Focus on rebuilding the relationship by re-establishing trust and removing fear. Recognize this will take time.
- Speed is of the essence. Make clear the actions you will take immediately to protect patient safety. Explain why some products and markets are at risk and others are not.
- Don’t just rely on written words. Phone calls and face-to-face meetings are better.
- Choose your words carefully. If you were misunderstood once, it can happen again.
- Less is more. Make sure your response is easy to understand and navigate. Regulators are busy people.
- Make sure your response is credible and that the resources and financial investment required will be made available. Fixing big problems without investment is not credible. Attempting to fix problems with the same thinking that created them will not be well-received.
- And, finally, make sure you convey the support and active engagement of your senior leadership. After all, they are ultimately responsible.
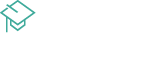
Avoid Observations! Prepare for a successful audit with FDA by attending Michael Hamrell’s webinar:
FDA GMP Inspections- Proven Prep & Survival Techniques
August 29, 2017 | 1:00-2:30PM EDT
Never:
- Openly disagree with the auditor’s findings.
- State that you’ve been audited by other regulatory agencies that gave you a clean bill of health.
- Just respond to single observations and ignore the big picture
- Treat the symptoms, not the cause. If you find yourself including statements such as “SOP rewritten,” “policy document updated,” or “retraining completed,” rip it up and start again.
- Attempt to justify bad practices by using risk assessment, validation, or spurious statistical methods. This is not a time for smoke and mirrors.
- Over-promise and under deliver.
- Be anything other than truthful and sincere.
Drafting Your Response: Down To The Specifics
Now that we have covered the foundations of a good written response, here is a simple step-by-step guide to walk you through the process.
Step 1: Have the right mind-set.
Mind-set dictates not just our thoughts, but also our actions. So:
- Get rid of the victim mentality quickly.
- Focus on meeting the emotional needs of the regulator. Rebuild trust and remove fear in actions, not just words.
Step 2: Ask yourself, “Is the observation factually correct?”
Or has there been some misunderstanding or miscommunication between you and the regulator? View this from the auditor’s perspective, not yours. Acknowledge any potential misunderstanding by providing facts and data. Accept responsibility for not conveying these clearly during the inspection. Remember, the effectiveness of communication is measured by the response you get. If there has been any misunderstanding, it’s your fault, not the inspector’s.
Step 3: Acknowledge each observation.
Accept the validity of all observations you feel are justified. However, if you don’t agree with the observation or criticism, say so. Defend your position based on good science, good regulatory practice, and common sense. For example, one of our clients was cited for “insufficient detail” in an SOP covering gowning procedures. The auditor felt the three-page SOP with eight photos and very few words was not detailed enough to ensure consistency of practice. The company rejected the validity of the observation by providing:
- a copy of the comprehensive education program that supported the SOP
- gowning validation data demonstrating excellent consistency in practice
- exit monitoring data showing excellent levels of aseptic practice in the manufacturing area
- the latest research on cognitive overload, emphasizing that pictures are better than words and less is more when it comes to instructional details
- links to webinars and resources on human error and the art and science of simplification.
Step 4: Complete a far-reaching risk assessment.
This must address:
- potential severity of harm
- probability of occurrence
- likelihood of detection/non-detection.
The scope of the risk assessment is vital. When did this issue first occur? How many batches are involved? Remember, these deficiencies probably extend to other plants in your network. Do not limit your risk assessment and CAPA (corrective action preventive action) plan to the plant in question or just to the specific observation in question.
Step 5: Perform immediate risk mitigation (correction).
What steps will you take immediately to mitigate risk? Who will do what, and by when? What are your milestones and measures?
- Stop manufacturing?
- Quarantine product?
- Recall product?
- Replace equipment?
How will short-term corrective actions be monitored and measured for effectiveness? What resources will be dedicated to successful implementation?
Step 6: Identify the error chain: What caused this to happen? Why didn’t you pick up on this and fix it?
A detailed review of all of the contributing factors (error chain) that led to the deficiency is essential. Take, for example, failure to set the correct specification for environmental monitoring. The questions the regulatory agency want answered include:
- Why did your own internal surveillance systems fail to pick this up?
- Self-inspection program
- QA
- Corporate audit
- Deviation and CAPA system
- Plant reviews