Purifying Plasmid DNA Using A Modern Chromatography Resin
By Janice Charlesworth, Downstream Processing Leader, Cobra Biologics; Tony Hitchcock, Technical Director, Cobra Biologics; Hazel Tharia, Head of Technical Co-ordination, Cobra Biologics; Henrik Ihre, Global Strategic Customer Relations Director, Cytiva; and Åsa Hagner McWhirter, Senior Application Scientist, Cytiva
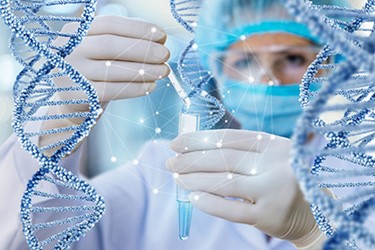
The rapid growth of the cell and gene therapy market is creating exciting opportunities in the advanced therapy sector. The ability to use the unique capabilities of RNA and DNA viruses to deliver functional genes in place of defective ones has led to the pursuit and development of a substantial number of cell and gene therapies. The vehicle for the delivery of these therapies is the viral vector, with adeno-associated viruses (AAV) being the most notable ones, as they have proven to be safe in humans while also exhibiting low immunogenicity.
AAV and lentiviral vectors are commonly produced through transfection with plasmid DNA containing the gene of interest. As products progress through clinical phases, there is a greater need for scalable plasmid DNA production, which must first be manufactured and purified in a GMP facility or high-quality plasmid DNA production areas. This has led to pressure on manufacturers to create the capacity and resources essential to meeting the rising demand for high quality plasmid DNA. CDMO Cobra Biologics recognized the need to address its own plasmid DNA capacity constraints for the rapidly increasing demand for viral vector production by not only increasing physical capacity but also by reexamining the purification process currently being used. Working with Cytiva, the companies developed a next-generation chromatography resin for the purification of plasmid DNA to reduce development costs and increase the manufacturing capacity through increased plasmid batch size and facility throughput. The resin was developed based on Cobra’s need but made available as product for others to order.
Supplier and bio-manufacturer relationships are often treated as transactional ones; yet, through this collaboration, Cobra and Cytiva were able to combine their expertise and experience and create a solution to address this manufacturing constraint. Their success demonstrates that mutual benefits can be achieved when suppliers and manufacturers work together to advance innovation and usher in a new era of drug development.
Get unlimited access to:
Enter your credentials below to log in. Not yet a member of Outsourced Pharma? Subscribe today.