Outsource Or Insource? Finding The Sweet Spot
By Nils U. Olsson, Ph.D.
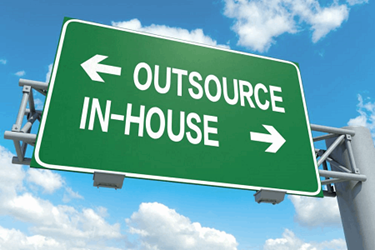
Pharmaceutical companies are constantly evaluating manufacturing strategies for more cost-effective drug development and commercial manufacturing operations. They recognize the need for maximum flexibility and value the opportunity to base outsourcing or insourcing decisions on the ability to deliver the highest quality service rapidly and at the lowest price.
While outsourced manufacturing was a relatively minor part of pharmaceutical companies’ business in the past, it continues to grow in popularity. Recent attention on so-called orphan drugs has strengthened the outsourcing trend, as modest production volumes required for some orphans often make outsourcing an attractive proposition. The emergence of virtually operated pharmaceutical companies has also contributed to the increase in outsourcing since it reduces overhead to a minimum.1 Offshoring API manufacturing to lower-cost countries has further fragmented the outsourcing landscape.
Larger pharmaceutical companies try to find the best balance between in-house manufacturing and outsourcing the production chain. For small emerging companies, however, outsourcing is often the only viable option. There is no perfect balance between outsourced or insourced manufacturing, but this article discusses some perspectives from both sides of the spectrum.
The classic driver for outsourcing manufacturing is that these operations can be conducted without making large capital investments. This allows resources to be focused on the organization’s core competencies and to generate best value. For early stage companies, there could be a benefit to manufacturing initial clinical trial material in-house to build up a good understanding of the process, but the funding for such an undertaking may not be available.
Weigh Options For Control, Oversight
A primary advantage of in-house manufacturing of drug substance or drug product is that it offers many control and oversight advantages. Direct management of a production plant provides the best opportunities to optimize and truly understand the process and to effectively troubleshoot it when problems arise. When development and manufacturing is outsourced to CMOs, some tribal knowledge and process understanding is lost. Failure investigations can become frustrating without personal access to the CMO site and its operators.
In one example, a company developing a biologic large-volume parenteral drug conducted manufacturing, fill finish, secondary packaging, labeling, shipping, and quality control under one roof in a dedicated facility. The site also served as corporate headquarters and housed all business functions. The distance between manufacturing and corporate management was short. When productions failures occurred, information was quickly communicated to upper management, which provided them the opportunity to engage with the operations team. When out of specification (OOS) results occurred, this organization quickly put all hands on deck and conducted investigations expeditiously. The insourcing model provides excellent opportunities to resolve problems quickly while keeping upper management informed and engaged. A big part of this is that manufacturing operators, quality control scientists, and records are readily accessible.
In contrast are OOS investigations at remote CMOs. The problem demands the same quick resolution for the contracting company as in the insourced model, but in this case the investigations are largely managed by the CMO. With electronic communications, documents, pictures, and chromatograms can be shared quickly with the contracting company, but from its perspective, updates on the investigation are never as fast or as frequent as desired. Small organizations also face competition for the CMO’s resources and time. A small company that may not need more than one or two batches per year does not have the same leverage over the CMO as a Big Pharma contractor.
In an example of the difficulties of managing an investigation at a CMO, a virtually operated business relying completely on outsourced manufacturing discovered contamination in a blend of powder. The investigation and search for a root cause relied heavily on the CMO as it was its facility, air handlers, manufacturing equipment, material dispensing areas, quality systems, etc. being used. While the contracting company was actively engaged in the investigation with queries, site visits, and creative ideas, the investigation was in the hands of the CMO. The search for the root cause of contamination took time and led to significant frustration. Once the source of the contamination had been found and rectified it was also difficult to get replacement batches scheduled, as there was competition for manufacturing slots from other companies.
Geographic Considerations
U.S. drug companies often send active pharmaceutical ingredient (API) manufacturing offshore to China or India, while handling drug product manufacturing and fill-finish back at home.
China has been a major supplier of basic chemicals and excipients to the world for some time, and its low cost structure has also made it a large producer of API for the local pharmaceutical industry.2 At present, China is not a major player on the international drug product scene, but that may change in the years to come. There are some top-notch API producers in China, many of which seasoned professionals with long careers in U.S. or European companies. They are now returning to China in large numbers, bringing with them the cGMP and quality mindset expected by the FDA and other regulatory agencies.3
The U.S. fill-finish industry, on the other hand, is more mature than China’s, and thus fill-finish contracts are often awarded to domestic CMOs.
Finding The Right Balance
Pharmaceutical and biotech industries are constantly evaluating these pros and cons of outsourcing to find the sweet spot. The new administration in Washington is encouraging industry to prioritize domestic manufacturing. How that will affect the balance between outsourced and insourced manufacturing in the pharmaceutical industry will be interesting to observe.
References:
- 2016 Nice Insight Contract Research - Preclinical and Clinical Survey (CRO Outsourcing survey) and Nice Insight 2016 Contract Development & Manufacturing Survey (CDMO Outsourcing survey), January 2016.
- Hepeng Jia, “Chinese manufacturers vie for piece of outsourcing pie,” Nature Biotechnology 25, 1337 - 1338, December 2007.
- N.U. Olsson, “E Pluribus Unum. Out of Many, One,” Outsourced Pharma, March 14, 2016.
About The Author:
Nils Olsson, Ph.D., is a biopharmaceutical entrepreneur and consultant to the life science industry with a background in outsourced and insourced manufacturing operations. He can be reached at nuolsson@gmail.com.