Optimization Of Hydrogen Peroxide Decontamination Ensures Reproducible Inactivation Results And High Product Safety
By Kim Jana Kutschan, Maria Jasmin Müller, Katja Pietruska, and Steffen Grune
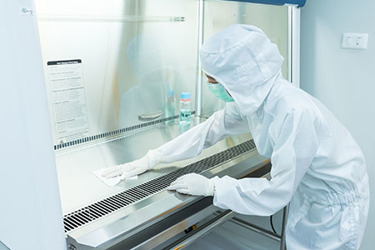
Due to its material compatibility, decomposition into harmless by-products, low explosion risk and broad-spectrum activity against fungi, bacteria, viruses and spores, hydrogen peroxide increasingly replaces alternative decontamination agents for gas processes. Since then, isolators, clean benches, RABS and clean rooms are decontaminated using vaporized hydrogen peroxide.
As a comparatively innovative fumigation technology, hydrogen peroxide decontamination is still not fully understood. Depending on room conditions, special generator systems and the variety of process influencing factors, cycle development appears to be a multi-parameter problem. In particular, the mode of action of fumigation in the gaseous or liquid phase is controversially discussed. While various technologies actively contribute to increasing the water concentration in the fumigated space and enable a so-called wet process, the associated condensation is actively avoided in a dry process. Furthermore, several studies suggests that the inactivation of contaminants such as bacterial spores and viruses by fumigation is different regardless of their resistance to chemical and physical treatments.
Carefully considering every single influencing factor and constant work on optimizing the entire fumigation system is critical. The production of highly critical products such as vaccines, gene therapy and immunotherapy products requires reliable, reproducible and effective decontamination processes.
Get unlimited access to:
Enter your credentials below to log in. Not yet a member of Outsourced Pharma? Subscribe today.