Making FMEA More Robust With HACCP
By Mark Durivage, Quality Systems Compliance LLC
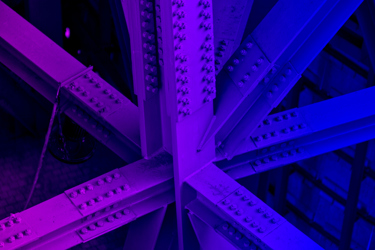
Failure mode and effects analysis (FMEA) risk priority number (RPN) scores and criticality analysis (CA) have traditionally been used to quantify risks for users, designs, and processes. However, the risks associated due to contamination are often not fully documented with traditional FMEA techniques.
To complement FMEA, companies sometimes utilize hazard analysis critical control point (HACCP), a risk management technique borrowed from the food industry, to consider the physical, chemical, biological, radiological, and allergenic contaminants that could be encountered during the inspection, processing, packaging, handling, storage, and distribution of pharmaceuticals, medical devices, cosmetics, tissues, and biologics.
FMEA Review
FMEA helps quantify and prioritize risk using severity, occurrence, and detection scores that are multiplied to produce the RPN. Criticality/severity (S) is a measure of the seriousness of the possible consequences of a hazard. Probability of occurrence (O) is the likelihood that a cause will occur and that it will induce the detrimental consequences of the associated hazard. Detection (D) is the probability that control (design, in-process, inspection, alert/warning) will eliminate, mitigate, or catch the defect. The RPN output of an FMEA is a relative risk score for each failure mode, which is used to rank the failure modes on a relative risk basis.
In addition to the RPN analysis, a CA assessment must also be conducted. The CA is the analysis of the severity and probability of occurrence.
An alternative to the RPN and CA is the use of action priority tables (APTs), which assign one of three suggested rankings to each action based upon the S, O, and D values. The APT rankings are as follows:
- High Priority – The FMEA team must identify appropriate actions or improve the prevention or detection controls or reduce the probability of occurrence.
- Medium Priority – The FMEA team should identify an appropriate action or improve the prevention or detection controls or reduce the probability of occurrence.
- Low Priority – The FMEA team could improve upon the prevention and detection rankings or reduce the probability of occurrence.
APTs are generally easier to use, do not require a calculation (eliminating the validation of a spreadsheet), and provide a single simple table reference to determine the appropriate level of action.
Hazard Analysis Critical Control Point (HACCP)
HACCP is a systematic approach to the identification, evaluation, and control of hazards. It was originally developed by NASA to prevent food poisoning of astronauts and is based on a set of principles and defined terms. Applied to pharmaceuticals, medical devices, cosmetics, tissues, and biologics, HACCP is used to control and monitor product hazards originating during inspection, processing, packaging, handling, storage, and distribution.
The core of HACCP consists of the following seven principles:
- Conduct hazard analysis and identify preventive measures
- Determine the critical control points
- Establish critical limits
- Monitor each critical control point
- Establish corrective actions
- Establish verification procedures
- Establish record keeping and documentation procedures
The foundation of a HACCP system is documented in a quality management system (QMS) that includes a prerequisite program to support the HACCP system. The prerequisites will vary by industry, facility, and scope of operations but will generally include the following:
Facilities
Is the company’s facility located, constructed, and maintained according to sanitary design principles? Does the company ensure linear product flow control to minimize contamination and cross contamination from raw materials to finished goods?
Supplier Control
Does the company control its purchasing processes to ensure purchased or otherwise acquired products, processes, and services conform to specified purchasing information? The type and extent of control applied to the suppliers and services is dependent upon their effect on subsequent realization processes and their output. Has the company established criteria for selecting, monitoring, and reevaluating suppliers? Is supplier performance in meeting requirements for the purchased product or services monitored?
Specifications
Has the company established written specifications for raw materials, packaging materials, semi-finished goods, and finished goods? Do purchasing documents contain information describing the product and/or services to be purchased?
Production Equipment
Does the company ensure all equipment is constructed, installed, qualified, and validated according to sanitary design principles?
Maintenance
Has the company established a preventive and corrective maintenance program? Are records of preventive and corrective maintenance maintained?
Calibration
Has the company established a calibration program, and does it maintain records of calibration activities?
Cleaning and Sanitation
Has the company established procedures and schedules for cleaning and sanitizing the equipment and the facility? Are records of cleaning and sanitation activities are maintained?
Personal Hygiene
Does the company ensure employees and other persons who enter the manufacturing plant follow the requirements for personal hygiene?
Training
Does the company ensure employees receive documented training in personal hygiene, GMPs, personal safety, and their role in the HACCP program?
Receiving, Storage, and Shipping
Does the company ensure raw materials and packaging materials are inspected prior to release for use? Does the company ensure raw materials, packaging materials, semi-finished goods, and finished goods are stored under sanitary conditions and proper environmental conditions, such as temperature and humidity, to assure their safety and prevent contamination and cross contamination?
Traceability and Recall
Does the company ensure raw materials, semi-finished goods, and finished goods are lot controlled? Has the company established a recall system so that rapid and complete tracing and recalls can be done when a product retrieval is necessary?
Pest Control
Has the company established a program for the management of pests (insects, rodents, birds, and other vermin) to prevent contamination and cross contamination of raw materials, semi-finished goods, and finished goods?
Critical Control Point (CCP) Determination
To determine if a control point in a process is critical (a CCP), a decision must be made whether a physical, chemical, biological, radiological, or allergenic source of contamination is reasonably possible. If the contaminant is determined to be reasonably possible, is the contaminant effectively controlled by the prerequisite program? If the prerequisite program does control the contaminant, then the point is considered a control point (CP). If the prerequisite program does not address the contaminant, the point is considered a CCP, which requires additional mitigation to ensure the potential source of contamination is properly mitigated and monitored.
Conclusion
It may be time to consider augmenting your risk management tool kit with HACCP to help your organization identify and mitigate physical, chemical, biological, radiological, and allergenic sources of contamination that could be encountered during the inspection, processing, packaging, handling, storage, and distribution of pharmaceuticals, medical devices, cosmetics, tissues, and biologics.
I cannot emphasize enough the importance of establishing documented procedures to manage the tools and methods used. Best practice includes providing rationales for your organization’s use of risk management tools and activities. The requirements and risk management tools presented in this article can and should be utilized based upon industry practice, guidance documents, and regulatory requirements.
References:
- FMEA Handbook 1st Ed, 2019, Automotive Industry Group (AIAG) and the Verband der Automobilindustrie (VDA), Southfield, MI.
- https://www.pharmaceuticalonline.com/doc/is-it-time-to-say-goodbye-to-fmea-risk-priority-number-rpn-scores-0001
- https://www.accessdata.fda.gov/scripts/cdrh/cfdocs/cfcfr/CFRSearch.cfm?CFRPart=120
About the Author:
Mark Allen Durivage is a practitioner, educator, consultant, and author. He is managing principal consultant at Quality Systems Compliance LLC, an ASQ Fellow, and an SRE Fellow. Durivage primarily works with companies in the FDA regulated industries (medical devices, human tissue, animal tissue, and pharmaceuticals), focusing on quality management system implementation, integration, updates, and training. Additionally, he provides internal and external audit support as well as FDA 483 and warning letter response and remediation services. He earned a BAS in computer aided machining from Siena Heights University and an MS in quality management from Eastern Michigan University. He holds several certifications including CRE, CQE, CQA, CSSBB, RAC (Global), and CTBS. He has written several books available through ASQ Quality Press, published articles in Quality Progress, and is a frequent contributor to Life Science Connect. You can contact him at mark.durivage@qscompliance.com and connect with him on LinkedIn.