Key Considerations For cGMP Building Conversions
By Scott Strom, DPR Construction
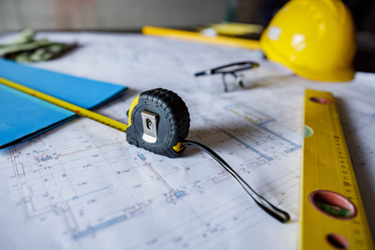
Adjacent to the pandemic boom, the life sciences sector has seen exponential growth in employment, with some of the highest in the country due to accelerated manufacturing demands. The pharmaceutical industry’s funding has reached an all-time high for cell and gene therapy and other related novel therapeutics, such as mRNA-based vaccines and lipid nano particle formulation delivery solutions. This adds to the growth in lab and manufacturing conversions in both traditional life science hubs, such as San Francisco, Raleigh, and Boston, as well as new emerging markets throughout the U.S.
As the life sciences workforce has increased, companies need more space to accommodate them. One emerging option is searching for buildings such as offices and warehouses and converting them into biopharma manufacturing facilities. On paper, this seems like an obvious way to expedite the construction schedule and achieve speed to market goals.
While it seems like building conversions are simply a matter of finding a large enough space to occupy and hiring an architecture, engineering, and construction (AEC) team, not all office/warehouse structures are as easy to convert as many would hope.
Those considering such a conversion can make decisions with greater confidence by taking advantage of lessons learned from the contracting side. Experiences and lessons learned from similar projects help paint a path forward for pharmaceutical manufacturers when looking at converting existing buildings to meet their needs.
Know The Characteristics Of The Ideal Building Candidate
Acknowledging the structure of a building is a key factor when touring possible conversion candidates. When an office building or warehouse facility was initially designed and built, those spaces served different purposes compared to those specifically meant to meet pharmaceutical manufacturing needs. As a result, considerations go well beyond square-footage, and some can even help move the starting blocks down the track.
Wood structures are often not the strongest candidates for manufacturing builds, whereas those made of concrete and steel create an advantage. For cGMP manufacturing conversions, the process will likely be to “build a building within a building,” so high-bay single-story structures with the potential to add a second floor or mezzanine area are the most common type of facility to start with.
Chemical storage requirements for a facility shift the higher you build. As a safety consideration, manufacturing buildings tend to use low-rise structures, because the more floors you have, the fewer chemicals you are allowed to store on the upper floors. The percentage of material allowed decreases the more floors your facility has, so to maximize inventory, it’s preferable to avoid buildings over three stories.
Another building characteristic to keep in mind is roof height and insulation. The standard height parameters necessary to create a walkable ceiling or mezzanine space is roughly 40 feet. This type of manufacturing facility design would generally put a mezzanine over the manufacturing area at about 20 feet, leaving enough room to access the space above the ceiling and place mechanical equipment on this new mezzanine. An existing building with lesser overall height that cannot easily accommodate this approach will lead to a more complex conversion; however, it may still be an ideal candidate using alternative design solutions.
Location considerations for manufacturing conversions are also important. Generally, it is best to avoid suburban and downtown areas, instead focusing largely on industrial areas for greater convenience to essential utilities. When evaluating the utility infrastructure of a building candidate, there should be electrical, water, and sanitary accessibility, as well as a large enough dock space to accommodate trucks and loading.
Keeping an open mind when touring a potential building candidate is important as well because it could open your business up to a lot of possibilities. For example, we recently converted a 1970s suburban, Class B office building with a distinctive H-shape into a 262,000-sq.-ft. flexible, state-of-the-art life science facility that combined research, development, and manufacturing functions in one facility. A key success factor was early collaboration between the owner, designer, and preconstruction team, which established values for each of the building components in the existing facility and fostered a collaborative decision-making approach during site selection. In fact, during this process, the team discovered that the existing building’s joists were inadequate to support the current and future demands of a manufacturing facility. As a result, the second floor in the manufacturing area was removed so a new reinforced steel structure could be inserted to support the existing adjacent floor. This allowed the project team to achieve the required height clearance and a column-free environment for the cleanrooms; provide a platform for the mechanical, electrical, and plumbing (MEP) systems directly on top of the cleanrooms; and support the rooftop MEP systems while staying within the existing building envelope.
Speed To Market Construction Tactics
Once the right building has been selected, the next step in an efficient conversion is understanding the business goals of the facility to decide on which delivery method is best for the project.
When speed to market is a primary objective, collaborative methods like a design-build approach can create the greatest efficiency. Unlocking the most value comes by having key project participants at the table early, working through challenges in the planning room, not in the field.
Consider a design-build arrangement, which means the permitting, design, and construction process is seamless and swift. Other time-saving benefits include simultaneously building the mechanical platform for the air handling units while the cleanrooms are being constructed, then figuring out a way to separate the two spaces to avoid building one on top of the other.
An additional factor to consider when converting within a tight timeframe is choosing whether a traditional field stick-build approach or using a prefabricated option is appropriate for scheduling objectives. Prefabrication is a method with many advantages, but like any other aspect of the process, it needs to be properly evaluated on a project-by-project basis to get the most value. For example, prefab elements often need to be fully designed before the actual manufacturing process begins. This can prevent the overlap of design and construction activities that a stick-built approach can take advantage of. Being able to recognize which option is best for a particular situation is a key milestone for every project.
The equipment procurement process and the ability to source materials early are critical for speed to market conversions as well. Supply chain pressures are acute with the current state of world affairs, becoming a real concern for many construction projects across all industries. Bear in mind, boom markets can also affect supply chains. Don’t assume that when the current wave of pandemic-related disruptions abate that new supply chain challenges won’t arise. When everyone is building, other equipment and materials may feel the squeeze.
Think through the challenge of materials arriving too early and consider securing additional laydown space in an adjacent empty warehouse to store materials as they arrive at the jobsite. You can further accelerate your schedule by eliminating the shop drawing process and instead relying on a detailed virtual building model used to go straight into fabrication. The 2-D information can be exported from the model and put on a set of plans for permitting.
Strong Alignment
Something that is not shared often enough when recognizing what makes a conversion successful is the importance of early trade partner selections and onboarding, which creates benefits for the entire project team. Having the client and all trade partners on board the same day the design process begins is a key factor in the project’s execution and optimizes collaboration throughout a project.
Consider allowing installers to be part of optimizing the design; this may lock in labor needs and assist in procuring equipment early in the schedule. With the right team in place when design begins, it is possible to work around potential challenges, such as site constraints, chemical management, floor loading and vibrations, low floor-to-floor heights, structural loading limitations, and HVAC space considerations.
Ultimately, there are many factors to consider in life science conversion work, but the most important thing to remember is that going in with an understanding of the building's strengths/weaknesses and addressing those issues early on is crucial to the success of the project.
Speed to market pressures are not going away, and with plenty of real estate seemingly ready for conversion, these challenges aren’t either. But with careful consideration of the right factors and a collaborative approach, pharmaceutical manufacturers can move forward with confidence, bringing their products from benchtop to market even faster.
About The Author:
Scott Strom is the life sciences core market leader for DPR Construction, serving customers in the areas of biotechnology, pharmaceuticals, bio-agricultural products, medical devices, and research. His expertise is in project costs and design standards for both lab and manufacturing facilities for both institutional and corporate projects.