Integrating Quality Processes And Documentation After A Merger
By Aaron Chio and Sydney Daniels, Clarkston Consulting
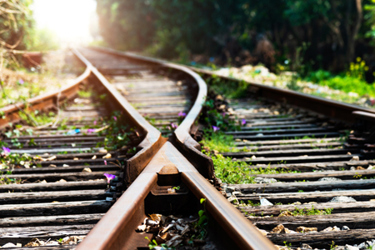
As life sciences organizations undergo transformational changes, such as merger & acquisition activities, one key principle stands out: boost operational efficiencies while ensuring that there are minimal disruptions to patients and the business. Essential to achieving this delicate balance is having the right documentation in place. This includes a holistic view of quality management systems (QMS) and corresponding standard operating procedures (SOPs), which must detail how quality is incorporated into the transition process.
In this piece, we’ll explore what quality leadership should consider throughout a merger to ensure the right quality processes and documentation are implemented.
Transition Plan
To ensure readiness on Day 1, a transition plan should be rapidly developed to direct the company staff and contractors on how to conduct day-to-day operations and support business continuity while undergoing the change and until the new and harmonized QMS and procedures are in place. The transition plan also can serve as an explanatory document for regulatory authorities on how quality principles were incorporated during the transition. For example, the transition plan may describe role equivalents across the legacy companies, how system access will be expanded, timelines and considerations, and how quality metrics will be collected and monitored. The plan should include how the company will maintain oversight and control of vendors through the transition. It should also document how significant events, including quality events, product complaints, and recall and recovery, will be managed.
Change Control
In parallel, a change control must be initiated per the ICH Q10 Guideline1 before Day 1 to ensure that there are no unintended consequences of the change and that all necessary actions are completed in a controlled and timely manner. A change control includes actions such as updating contact lists, product labels, and distribution licenses, identifying who is responsible, and the timeline for completion. Often, the master change control references secondary change controls for system or SOP changes.
Process and Procedure Harmonization
To make the integration seamless, leaders may want to embark on an organization-wide process and procedure harmonization project as part of the overall integration strategy. A single set of SOPs outlines the business processes of the new organization and helps to deliver on the operational efficiencies promised by the merger. SOPs are the backbone of a mature quality organization,2 and they give clear guidance on how processes must be executed, contributing to operational consistency and high product quality for patients. Developing effective SOPs can be a time-consuming affair for any organization; however, integrated companies face a unique set of challenges as employees must navigate new responsibilities, teams, and ways of working.
To undertake a successful SOP project, leaders should consider taking the following steps.
Step 1
First, ensure that employees understand their new roles and that the responsibilities of each GxP function are clearly defined. The delineation between functions is needed to determine who is the appropriate owner of each SOP and which stakeholders should be involved in the process. After aligning on department names and overall responsibilities, cross-functional leaders should then align to a single set of named roles and responsibilities to be used across the SOPs. Within each procedure, a brief summary of the relevant roles and responsibilities should be included. Using role names rather than job titles is recommended, as job titles are likely to change as the organization evolves. Ultimately, aligning on a single set of role names increases the consistency between SOPs and makes it easier for users to understand who is responsible for what. Prior to approval, all stakeholders should be given an opportunity to review the SOP to ensure their group can comply with the procedure.
Step 2
Next, each function should clearly define the scope of its procedures to eliminate the issue of conflicting SOPs. Without a single source of truth, compliance with procedures can be challenging or even impossible, which poses a regulatory risk. If a single process is described in more than one SOP, it is more likely that those SOPs will conflict. Since processes are not conducted in silos, it can be challenging to identify where one procedure should stop and another should begin.
Before drafting SOPs, it can help to conduct process mapping to identify how related processes interact to clearly define the scope of the procedure and to ensure there is organizational alignment on the overall process taking place. Especially for organizations undergoing a merger, business process mapping3 is highly advisable, as disjointed communication between employees from different legacy groups and multiple former ways of completing processes are common challenges. Reaching an agreement on a process flow before drafting an SOP minimizes rework and ensures all stakeholders are adequately represented. Within the procedure, redundancy may be avoided by cross-referencing other SOPs and creating in-text references, where needed. This not only streamlines procedures but also creates a cohesive procedural framework and maintains the integrity of the SOPs.
Step 3
Before any drafting can begin, the quality assurance leadership team must also establish an instructive SOP template and guidelines for writing SOPs. These are essential to ensure drafted SOPs contain the required sections and are written in a similar style and detail level. The guidelines should make a distinction between all types of procedures and supporting documents.
Effective SOPs should also provide sufficient details for a trained person to perform the procedure consistently. SOPs should include the “who, what, where, and when” of the process using language that is direct and easily understandable. If SOPs are difficult to understand, the business processes established within may not be consistently executed. SOPs should be arranged chronologically and clearly identify where outcomes are documented or stored. By following such writing principles, users should be able to grasp the processes of the unified organization quicker and more effectively.
Ensuring SOP Harmonization Post-Integration
Embarking on an SOP harmonization project following a biopharma or biotech merger requires meticulous planning, effective project management, and active involvement from the team. Allowing stakeholders to contribute to the development of new procedures not only ensures a smoother transition but also fosters buy-in and acceptance of the new way of operating, which is crucial for effective change management.
While drafting effective SOPs may be a time-consuming process, the result is streamlined operations, improved compliance, and enhanced efficiency, making it a worthwhile endeavor for the success of the merged entity. Through collaborative efforts and a commitment to excellence, the harmonization of SOPs sets the stage for a cohesive and successful future.
References
- International Conference on Harmonisation. ICH Harmonised Tripartite Guideline: Pharmaceutical Quality System Q10. https://database.ich.org/sites/default/files/Q10%20Guideline.pdf
- Shockey, S. (2021, December 27). SOP Best Practices to Strengthen SOP Maturity. Clarkston Consulting. https://clarkstonconsulting.com/insights/sop-best-practices
- Shockey, S. (2023, November 3). Five Steps for Process Mapping in Quality. Clarkston Consulting. https://clarkstonconsulting.com/insights/steps-for-process-mapping-in-quality/
About The Authors:
Aaron Chio is an associate partner at Clarkston Consulting with more than 15 years of experience working with Fortune 500 consumer products, retail, and life sciences organizations. He has extensive experience guiding senior executives across functional, business unit, and enterprisewide business transformations to shape corporate strategy, drive operational improvements, and evolve technology capabilities to accelerate and capture value creation. Chio is an economist with an MBA from the Questrom School of Business at Boston University with concentrations in strategy and marketing. He has received executive education from the UCLA Anderson School of Management and the Tecnologico de Monterrey in Mexico.
Sydney Daniels is an associate consultant, business analyst, and technical writer at Clarkston Consulting, specializing in the life sciences industry. In her role, she works with biopharma organizations undergoing organizational shifts, guiding them through project planning, process harmonization, and drafting of key GxP documentation. She is passionate about establishing efficient, quality by design processes. Prior to joining Clarkston, Daniels worked in non-clinical neuroscience research. She holds a B.S. in neuroscience and economics from the University of Kentucky.