Implement A Risk-Based Approach To Safely Manufacture HPAPIs
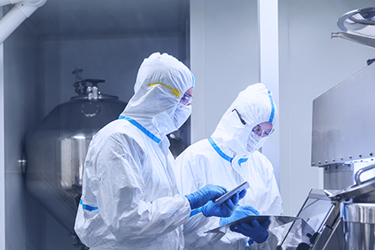
Highly potent active pharmaceutical ingredients (HPAPIs) are becoming increasingly appealing as therapeutic vehicles for a number of indications, including cancer. As drug manufacturers look to start producing HPAPIs with higher frequency, they must also consider the obstacles associated with scaling these highly potent chemicals. Some leaders in the industry are opting to implement risk-based approaches that leverage occupational exposure banding (OEB) assessments to designate how much exposure to an HPAPI is acceptable for personnel, known as the occupational exposure limit (OEL). OEB protocols can help companies build stronger, more effective containment strategies to protect employees.
In a recent webinar hosted by Ajinomoto Bio-Pharma Services, Karel Vervisch, Manager of Research and Development, provided his expert insight into how to implement a risk-based OEB strategy across an HPAPI manufacturing life cycle. Below, he answers webinar attendee questions about Aji Bio-Pharma’s in-house workflows for handling different OEB levels and reducing risk.
Q: How much experience do you have with continuous flow for HPAPIs?
Karel: We have more than 20 years of experience developing highly potent products, toxic products, and toxic gases in a continuous flow manner, both in lab and pilots as well as in production. Therefore, we have extensive professional experience and a knowledgeable team with the expertise needed to manage a range of highly potent products by using continuous flow.
Q: Could you please highlight your capabilities for handling hazardous reactions?
Karel: For hazardous reactions, we have a team on-site who performs all process safety tests. We will classify reactions from 1 to 5. If we have reaction class 5 hazards, we will most likely use continuous flow, in which we can better control the exothermicity of the mixture. In our approach, we want to see how hazardous it is. We ask ourselves: is it explosive; is there a lot of gas coming out; is it toxic; and what are the limits?
Because each situation is different, it should be looked at on a case-by-case basis. We have experience with cyanides, azides, HPAPIs, and diazomethane. We pride ourselves on our safety assessments which allow us to adequately manage these types of chemistries.
Q: Could you talk about the differences in design between your sites with different OEB capabilities?
Karel: First, we always want to work as closely to the product as possible to limit the chance of exposure. If working with an HPAPI, we try to work in closed conditions or as closed as possible. When it comes to OEB4 and OEB5, we work more compartmentalized, which means we have installed corridors and airlocks with positive and negative pressure. This will ensure that in case of an incident with the release of product in the production area, all dust is kept in the room due to the negative pressure. Design-wise, that’s the difference between OEB3 and OEB5: using an airlock cell as well as fixed containment and closed offloading when charging and discharging products [within the cell].
Q: What about micronization capabilities? Do you have milling equipment that accommodates OEB5?
Karel: Yes, we’re one of the few CDMOs that have the milling equipment necessary for HPAPIs to ensure safety. The micronization equipment at our Wetteren facility is fully operational and able to cope with OEB5.
Q: Do you run OEB4 and OEB5 on the same line as OEB1 through OEB3?
Karel: We sometimes run OEB3 products on OEB5 equipment but never the other way around; one reason for doing this is that the intermediates formed would remain OEB3 but following the reaction, the changed molecule may now be OEB4 or OEB5. We will calculate the maximum acceptable carryover from an OEB5 onto an OEB3. The only difference is that we have to clean more thoroughly and that the acceptable carryover limits will be much lower. With increased cleaning and a residual amount that is as low as required, it is perfectly possible to run OEB3 and OEB5 in one facility.
To watch the full webinar and Q&A session hosted by Aji Bio-Pharma, please click here.