How To Catalyze & Sustain Continuous Improvement In Pharmaceutical Operations
By Peiyi Ko, Ph.D.; Peter Calcott, Ph.D.; Martin Stein, D.Sc.
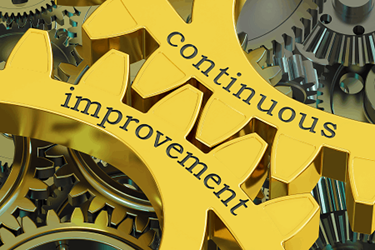
The (bio)pharma industry bears the burden of redundant processes and high cost of goods sold. While other industries have learned from the principles of quality and statistical control methodology, pharma has been slow on the uptake. Competition is increasing from abroad, generic drugs, biosimilars, and other sectors. And, our archaic healthcare system is potentially on the move to catch up with the rest of the developed world, so the time is right. Still, the industry is struggling to move forward with ICH (International Council on Harmonisation) Q8-12. As we suggested in our previous article, both technological and organizational capacities are important for these large-scale initiatives.1 Here we’ll further the discussion on tactic designs that utilize collaboration tools to facilitate Kaizen/continuous improvement in quality management systems (QMSs).
Return On Investment Rationale
To establish structure and function more in line with the principles of true quality, we start with challenging the classic paradigm that has quality, cost, and time as competing elements for all projects or operations: If you want quality, it takes time and costs money. If you want it cheap and quick, quality is lost. However, there may be better ways to reach business goals, e.g., improving QMS to reduce waste from quality failures (rejected products) and negative consequences such as investigations, corrective and preventive actions (CAPA), complaints, and recalls. We can balance costs of poor quality with investments in prevention and appraisal. Companies need to analyze the loss of money from internal and external failures. Two British Standards Institution guides provide basis to establish generic economic models for this type of calculation.2,3
External failure is a much greater loss and has hidden costs. One example from a pharmaceutical company was that a simple recall of a small product (with low annual sales) resulted in a loss of over three years of profits. Analysis of where money is spent is also necessary. When that is known, how effective each spend is in terms of ROI can be assessed. Allocate resources appropriately to the various cost centers, and be ruthless to get value for money: First, eliminate external failures, which are expensive and bad for the company’s reputation Second, eliminate internal failures. Internal failures are not just decreased productivity; there are other costs including investigations (often hundreds of labor hours), implementation of CAPAs, and expensive change controls. One example is a change control to substitute a new supplier for an excipient with estimated savings in the tens of thousands of dollars per year. However, the cost to implement was estimated to yield a payback period of 15 years. This was clearly too long. And if the investigation does not identify the major contributing factors, the costs escalate. Third, shore-up prevention investment until you can decrease appraisal investment. If the prevention strategy is not right, its ROI is decreased. So companies have to invest in more after the appraisal to catch the problem after it has happened.
Thinking long-term, companies can also invest in knowledge management and use it to facilitate continuous improvement. In one case, social technologies were used to create an energized network that improved knowledge flow and therefore improved KPIs such as right first time, spending, product supply, people capability, and employee engagement: the global KM network located a spare turret in Singapore within one business day to replace a damaged one for a key product in the U.K. It saved $3 million and 20 weeks in the short-term and enhanced credibility and relationships with partners in the long-run.4,5
In the context of QbD, the knowledge-creation base is broad: (1) considering the outcomes of exploratory and clinical development studies for product development, (2) taking inputs from technology-transfer activities to inform process, control strategy, and process validation, which form the backbone for continued product and process improvement, (3) identifying and evaluating improvement opportunities from pharmaceutical quality systems, and (4) utilizing commercial manufacturing knowledge for continual product improvement and continuing product assessment such as complaint handling and stability in case of product discontinuation.6
Among the vast territory that could be tackled, we think lab data workflow and continued process verification (CPV), or stage 3 validation, could be fruitful for continuous improvement. Allotrope Foundation has put efforts into establishing open document and metadata standards to be incorporated in the instrument software framework, which can improve data processing efficiency and reduce data integrity issues due to human errors.7 CPV provides ongoing inputs to enhance QbD and life cycle management to improve control and lower failure rates.8 There is opportunity for Big Data analytics deployment, especially for legacy products’ risk assessments, where customer complaints and failure investigations need to be included in addition to more quantitative analysis of process capability, complaint trends, and historical causes of discards9
Seeking KPIs For Knowledge Management
Herwig et al. provided a comprehensive review of recent approaches and major gaps and opportunities for efficient and effective knowledge management (KM), which is thought to be the necessary precursor to successful QbD implementation by the industry.10 The importance of a data-driven approach to management has long been illustrated by Edward Deming’s quote, “If you can’t measure it, you can’t manage it.” Still, there are many “unmeasurable things” worth attempting to improve by developing indicative measures. Similarly, there’s a need for effective KM indicators to assess QbD readiness of a company regardless of the approaches.10 In addition to reporting quality metrics proposed by the FDA (e.g., lot acceptance rate, invalidated OOS rate, recall events, and total and critical complaint rates), some metrics for consideration as KPIs for evaluating KM investment are process compliance improvement (e.g. right first time, [recurring] deviation rate), issue resolution time, and reduced (re-)training needs. These are related to how knowledge management improves customer satisfaction.11 In pursuit of leading indicators, quality culture is hard to measure yet desirable, and teamwork is an important part of the quality culture.12 Some measurements for “soft” issues can be considered as indicators for a broader scope of assessment. Examples are self-assessment tools and software that help translate strategic planning to several organizational layers and provide customizable dashboards for KPI tracking.
Design For “Quantitative Kaizen:” Measure And Standardize Before Analyze
The first step to improving knowledge management could be improving the consistency of glossaries. Business glossaries are useful in initiatives such as application development and repository clean-up. It’s thought that a master data management (MDM) program won’t even work or scale unless the resulting business glossary of terms across the MDM hub (and its data model), the business applications, and data warehouse in which the information assets are being governed are reconciled and well-governed.13 Having good metadata for data governance is the foundation for knowledge management, and striving for consistency in business and technological glossaries is essential for that.
There are four common stages to performing Big Data analytics: define goals, collect and prepare data, build a model and evaluate, and deploy.14 Software like Alteryx can be used to design (Big) Data workflow with less IT expertise so that the underlying data pipelines can be streamlined by users closer to the business end.
There is also the opportunity to analyze qualitative data often ignored in the process of creating standardized databases. For example, Toyota Management System utilizes three voices for feedback: the voice of the customer, the voice of the employee, and the voice of the process. Customer feedback can be obtained from various sources including customer service calls. With technological advancements, this approach may be augmented by cognitive search, which integrate features such as search engine, artificial intelligence/machine learning, and natural language processing that convert text into statistical information.15 In pharmaceutical manufacturing, these can be elements of a product-quality-complaint management system to be able to detect new side effects being discussed by patients (i.e. voice of customer) within regulatory time limits for reporting.15 Unmet needs can lead to new product innovations. Problems can lead to knowledge assets, including patentable new processes. This will help deliver the power of “positive quality.” A knowledge management system that identifies hidden knowledge assets could also be a potential spin-off from the auditing process. Technology is moving rapidly and enabling the deployment of algorithms and analyses that support the creation of a quality-systems science applications.
Just like the accounting process, quality metrics/KPIs should be audited. A great deal of energy and effort has been expended in training and certification, but the systematic management of quality continues to suffer from a lack of consistency and ambiguity. Therefore, the quality process and continuous improvement systems could benefit from an overall audit called Kaizenomics, which standardizes terms and data utilized.16 By taking advantage of these ideas, companies will help offset the costs of eliminating negative quality and provide for renewed interest in making the quality process deliver positive ROI. Too often company executives are reluctant to invest in the quality process because the initial costs are visible and the benefits are not easily identifiable.
Design For “Qualitative Kaizen:” Technology-Facilitated Collaboration And Alignment
Soft issues are critical for successful, complex project delivery.17 Data integrity throughout the drug development life cycle is emphasized by the FDA and other international organizations and critical to the quality of knowledge derived from the data. Technology is only part of the picture; human factors and corporate culture play important roles, too. At the operator level, better classification of human errors helps provide better alignment of corrective action. Some root causes of failures (e.g., non-conformances in production, packaging, quality control sampling and testing, documentation, and validation) have system precursors and managerial elements to improve that cannot be addressed by training human operators alone. This perspective is beneficial for improving effectiveness of corrective actions. Extensive use of teamwork and a robust employee-suggestion system enable management to continuously improve and monitor performance at three levels: practice, program, and policy. In addition to identifying benefits from the elimination of gaps at these levels, these teams can be challenged on an ongoing basis to innovate for attaining quality objectives. Teams utilizing cross-functional, multiple rounds of critiques and an iterative process of refinement become an engine of change and the basis for culture management that enables strategic adaptation to change.18 Carefully guided collaboration creates a shadow organization where job descriptions and the organizational chart are less important than the organization’s objectives and strategies. Teams can enable an organization to become more innovative since risk is diffused and new initiatives are encouraged.
Applying human factors and human-centered design methodologies to leverage data analytics and Web-based technologies for cross-functional teamwork can, arguably, improve project performance and sustain a quality initiative. Capturing and depicting system elements and interactions through a system-mapping tool such as cognitive work analysis (CWA) can help clarify the complex system states and inform the construction and evaluation of data models.19 This analysis can help members of an organization understand how their work contributes to organizational success and failure, how decisions are made, and how they relate to each other across the organization, thus enabling more effective knowledge generation and sharing. This also applies to data collection across the supply chain to achieve knowledge-based risk management, which has its own challenges and is greatly facilitated through the recent advancement of cloud-based quality management systems and track-and-trace technologies. Regardless, stakeholder engagement is the key. On the human side, best practices can be designed for disseminating and sustaining the methodology within the team and across the organization.20 The objective should be to empower internal subject matter experts to create, capture, and share knowledge for problem solving without IT experts.21
One way to facilitate collaboration and alignment is to apply user-centered activities to aid defining stakeholder-relevant goals and user interface (e.g., quality-management-system dashboards that take appropriate level of management visibility into account). High-level usability requirements clarify user needs, provide explicit user-oriented goals for development, identify requirements for data and business processes, and warn of potential problems/risks. Exploring human-system interaction design alternatives early reduces system blindness that could lead to costly implementation failure. These communications also help define project goals, gain buy-in, manage scope and expectations, and keep alternatives in mind. It is also important to improve meetings (virtual or in person), which are commonly inefficient.22 It can be from lack of effective preparation, failing to agree during, and missing follow-through after. We need to better align stakeholders’ interests before establishing common goals. To help anchor the numerous discussions on the highest-level goals (e.g., implementing QbD), there needs to be a medium that can engage stakeholders, facilitate discussions, and catalyze actions. If customized well, software platform tools from companies like Atlassian can coordinate stakeholders and leverage knowledge for better managing projects.
Conclusion
We would like to emphasize the importance of establishing a sensible ROI scenario based on real and consistent measurements to help build a business case for appraisal and preventative investments to address external and internal failures. We proposed a systematic change management process for effective continuous improvement, specifically built around glossary standardization that could inform metadata for data governance. We hope companies can harness the power of positive quality to create enthusiasm for process improvements and generate new thinking about innovation and the value of knowledge assets that are hidden in the discussions of teams and customer feedback. We also recommend leveraging data analytics and web-based technologies to facilitate meetings, communication, and cross-functional teamwork to improve project performance and sustain a quality initiative within the company.
References:
- Ko, P., & Calcott, P. (2017). Rethinking Knowledge Management & Data-Driven Risk Management For Quality By Design. Retrieved from Pharmaceutical Online: https://www.pharmaceuticalonline.com/doc/rethinking-knowledge-management-data-driven-risk-management-for-quality-by-design-0001
- British Standards Institution. (1990). BS 6143-2:1990 Guide to the economics of quality - Part 2: Prevention, appraisal and failure model.
- British Standards Institution. (1992). BS 6143-2: 1992 Guide to the economics of quality - Part I: Process cost model.
- Lipa, M., & Guenard, R. (2014). A practical approach to managing knowledge: Making knowledge flow in Merck's manufacturing division. Retrieved from Office of the Chief Knowledge Officer, NASA: https://km.nasa.gov/wp-content/wp-content/uploads/sites/3/2015/01/3-Merck-Knowledge-2020-Presentation.pdf
- Lipa, M., Bruno, S., Gunard, R., & Thien, M. (2013). A practical approach to managing knowledge - a case study of the evolution of knowledge management (KM) at Merk. Pharmaceutical Engineering, 33(6), 91-104.
- Pramod, K., Tahir, M. A., Charoo, N. A., Ansari, S. H., & Ali, J. (2016). Pharmaceutical product development: A quality by design approach. International Journal of Pharmaceutical Investigation, 6(3), 129-138.
- Colsman, W., & Uphill, R. (2015). A portable data format for laboratory data. Retrieved from Scientific Computing World: https://www.scientific-computing.com/feature/portable-data-format-laboratory-data
- Alsmeyer, D., & Pazhayattil, A. (2014). A Case for Stage 3 Continued Process Verification. Retrieved from Pharmaceutical Manufacturing: http://www.pharmamanufacturing.com/articles/2014/stage3-continued-process-verification/
- Ball, C., Gampfer, J., Grunkemeier, J., Roche, M., Laenan, L., Baker, D., . . . McNay, J. (2014). Continued Process Verification: An Industry Position Paper with Example Plan. BioPhorum Operations Group.
- Herwig, C., Garcia-Aponte, O., Golabgir, A., & Rathore, A. S. (2015). Knowledge management in the QbD paradigm: manufacturing of biotech therapeutics. Trends in Biotechnology, 33(7), 381-387.
- Verint Systems Inc. (2016). Seven steps to build a business case for knowledge management. Retrieved from www.kmworld.com/WhitePapers/KMWhitePaper/Seven-Steps-to-Build-a-Business-Case-for-Knowledge-Management_6893.pdf
- Kieffer, R. (2015). Quality culture and its measurement. Retrieved from Parenteral Drug Association (PDA) News Archive Full story: https://www.pda.org/pda-europe/news-archive/full-story/2015/01/30/quality-culture-and-its-measurement
- White, A. (2014). What a to-do over Business Glossaries! Retrieved from Gartner Blog Network: http://blogs.gartner.com/andrew_white/2014/01/16/what-a-to-do-over-business-glossaries/
- Drury, C. G. (2015). Human factors/ergonomics implications of big data analytics: Chartered Institute of Ergonomics and Human Factors annual lecture. Ergonomics, 58(5), 659-673.
- Jeanrond, H.-J. (2017). Cognitive search brings the power of AI to enterprise search. KMWorld.
- Stein, M. M. (2011). Design of a continuous improvement glossary based audit system. Retrieved from XONITEK Industry News: https://www.xonitek.com/design-of-a-continuous-improvement-glossary-based-audit-system/
- Asvadurov, S., Ellis, M., Brinded, T., Brown, T., Knox, D., & Speering, R. (2017). The art of project leadership: Delivering the world's largest projects. Retrieved from McKinsey& Company Capital Projects & Infrastructure Report: http://www.mckinsey.com/industries/capital-projects-and-infrastructure/our-insights/the-art-of-project-leadership-delivering-the-worlds-largest-projects
- Stein, M. M. (2002). Strategic adaptation to Change: A practical system for achieving breakthrough performance. Journal of Organizational Execellence, 17-24.
- Stanton, N. A., Salmon, P. M., Alker, G. H., & Jenkins, D. P. (2017). Cognitive Work Analysis: Applications, extensions and future directions. Boca Raton, FL: CRC Press, Taylor & Francis Group.
- Szalma, J. L. (2014). On the application of motivation theory to human factors/ergonomics: Motivational design principles for human-technology interaction. Human Factors, 56(8), 1453-1471.
- Risse, M. (2017). 5 questions to ask when evaluating data analytics offerings. Retrieved from Pharmaceutical Manufacturing: http://www.pharmamanufacturing.com/articles/2017/5-questions-to-ask-when-evaluating-data-analytics-offerings/
- Perlow, L. A., Hadley, C. N., & Eun, E. (2017). Stop the meeting madness. Retrieved from Harvard Business Review: https://hbr.org/2017/07/stop-the-meeting-madness
About The Authors:
Peiyi Ko, Ph.D. & CPE (KoCreation Design LLC), applies human-system interaction research and human-centered design to create opportunities for positive changes, catalyzing innovation, and improving project performance by leveraging analytics and facilitating cross-functional collaboration. She has guest lectured at universities and led workshops. Previously she provided human factors/ergonomics consulting as well as software usability analyses and design recommendations at BSI EHS Services and Solutions and the Lawrence Berkeley National Laboratory. She also serves as one of the consulting experts at the Interdisciplinary Center for Healthy Workplaces at UC Berkeley. She obtained her Ph.D. from UC Berkeley in 2012 with additional training from two interdisciplinary certificate programs there: Engineering, Business & Sustainability and Management of Technology. You can reach her at info@kocreationdesign.com.
Peter H. Calcott, Ph.D., is president and CEO of Calcott Consulting LLC, which is focused on delivering solutions to pharmaceutical and biotechnology companies in the areas of corporate strategy, supply chain, quality, clinical development, regulatory affairs, corporate compliance, and enterprise e-solutions. He is also an academic program developer for the University of California, Berkeley in biotechnology and pharmaceutics postgraduate programs. Previously, he was executive VP at PDL BioPharma, where he was responsible for development and implementation of quality and compliance strategy across the corporation. He has held numerous positions in quality and compliance, research and development, regulatory affairs, process development, and manufacturing at pharmaceutical companies including Chiron, Immunex, SmithKline Beecham, and Bayer. He has successfully licensed products in the biologics, drugs, and device sectors on all six continents. Dr. Calcott holds a doctorate in microbial physiology and biochemistry from the University of Sussex in England. You can reach him at peterc@calcott-consulting.com.
Martin Stein, D. Sc., is an experienced management consultant with extensive background as an economist within the public and private sector. He has specialized in strategic implementation and quantitative analysis for decision-making and has consulted with organizations such as Hyundai Motors, Toyota Motor America, General Electric, and the U.S. Departments of Transportation and Defense on a global basis. He has chaired conferences on international economic and business topics in countries such as the United Kingdom, Japan, and Canada for organizations such as the Conference Board. He is listed in Who’s Who in Business and Finance and Who’s Who in America. He has a B.S. and M.A. in economics from the University of Maryland and a doctor of science in applied mathematics and information systems from the UPMC (Paris).