Facility Design For OSD Continuous Manufacturing
By Allison Cacciatore, executive director, facilities design and engineering, Pharmatech Associates
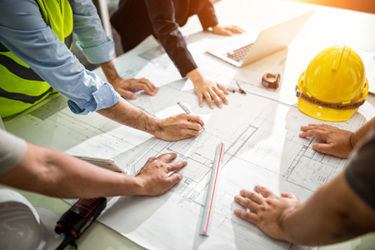
A number of oral solid dosage (OSD) forms are well suited for continuous manufacturing processing. Real-time release, smaller facility footprint, and lower manufacturing costs over the long term are three important factors that contribute to the economic advantage of continuous over batch processing. Continuous manufacturing is beneficial for companies looking to streamline manufacturing operations, but not all types of OSD products are good candidates. This article considers the types of OSD to target and compares new facility construction versus renovation.
Facility design for continuous manufacturing of OSD differs significantly from design of facilities dedicated to batch processing. The primary differences reside within the facility layout, in terms of consolidation of unit operations, utility sizing, and limited manual process involvement, which minimizes the number of required personnel. The reduction in facility complexity, with fewer rooms for individual operations, leads to fewer personnel required to perform maintenance activities. There are specific considerations for scale reduction and speed of processing. Space reduction provides for lower capital expenditures and personnel reduction contributes to lower operating cost.
Facility Footprint
The size and shape of a facility for continuous manufacturing of OSD products provide a footprint that is smaller and more compact than that of traditional batch processing. However, size and shape are dependent upon the technology used. In some cases, primarily for wet granulation processing, the building needs to be taller to accommodate the vertical linear flow of the continuous manufacturing equipment. But, in general, overall square footage is less than in a traditional facility as the unit operations are not segregated and do not require distinct processing suites. In a traditional facility, climatized staging space is required for bins that hold released materials between process steps. Every step requires sampling, a separate batch record, and release before it can move forward for processing. With continuous manufacturing, there are no bins and no waiting, as real-time release (RTR) is accomplished with process analytical technology (PAT).
Unit Operation Impact
During batch processing, all unit operations are performed in different rooms. Typical steps include drying, blending, milling, compression, and coating. Each room contains its own operators and individual room controls.
With continuous manufacturing, the unit operations are no longer segregated. The associated burden of maintaining certification of discrete suites for environmental monitoring is minimized and the procedures that govern processing become streamlined and simplified. During batch production each process step is managed individually, but with the continuous manufacturing process there is one overall batch record and associated documentation instead of many. If the business is interested in feeding the API to the oral solid dose continuously, there still will be a need to release the API in advance of beginning the OSD process. This directly affects the speed of the process and has not historically provided any advantage over being supplied as a batch.
Scale Reduction And Speed of Processing
Typically, there are three methods for production of OSD: roller compaction, direct compression, and wet compression. Roller compaction takes powder and presses it hard between two heavy rollers, producing a fragile ribbon that breaks into flakes that are then sieved until a desired particle size distribution is achieved; those particles are then pressed together to make tablets. With direct compression, material is brought together through several different feeders for the API and various excipients, fed to a blender, then sent directly into the compression machine presses to form tablets. Wet compression contains a set of feeders that can be manually filled or vacuum lifted from drums, pneumatically conveyed to the feeder hopper, then fed into a blending area and then into a twin-screw granulator that produces the wet granules that are fed into a segmented dryer to a treatment unit that mills the product to the correct size. There is an additional blending step, typically with magnesium stearate, before being fed to the compression step.
When continuously manufacturing OSD products, the easiest and most cost-effective choice for processing is direct compression. This method is easier because it provides continuous blending that handles material variation better, making it easier to control the variability of the product. In the development phase, more experiments are possible, making selection of direct compression more easily tailored to the needs of the final product.
If the only option for the product is wet granulation, there is not a tremendous reduction in cost realized as this process translates to a fully vertical process in the continuous manufacturing format. Typically, the facility will need to be very tall (three to four stories) to accommodate the equipment needed. However, if wet granulation is the only option, a greenfield is usually cheaper than renovating an existing facility that might not have the required height or appropriate steel structure to support adding extra stories to accommodate the process.
Personnel Impact
With continuous processing and the elimination of discrete unit operations, the amount of process oversight is reduced. Furthermore, the inclusion of PAT results in automated real-time monitoring of the process that can take place virtually, with less need for human oversight.
Continuous manufacturing facilities are simplified compared to batch facilities. There are fewer rooms for individual operations, leading to fewer maintenance activities required, which minimizes the number of personnel needed from a maintenance perspective.
In general, the cost associated with training personnel on the continuous manufacturing process is high since this knowledge is not commonplace and the number of experienced personnel is limited.
Utilities
HVAC
With continuous, there is a reduced need for HVAC capacity as the process is integrated and the need for separate suites and airlocks is virtually eliminated. The need for climatized staging space for batches is eliminated, too. Cost reduction is realized in capital expenditure as well as in operating and maintenance costs. The unit itself can be much smaller because of the reduced size of the controlled environment and a more cost-effective design that has limited need for personnel access to the manufacturing suite(s).
Equipment Cleaning
A downside for continuous manufacturing is the amount of water and chemicals required for cleaning the equipment, which is more complex than batch processing and does not lend itself to clean-in-place (CIP). Disassembly and manual manipulations of the equipment are required to transport the parts elsewhere for cleaning. Depending on the nature of the product that is being processed, the actual cleaning and changeover time will be affected. If the cleaning process is extremely long, extra sets of change parts can be used to keep the equipment in operation, although these can be costly as this equipment is complex and product-specific. Single-use technology has become prevalent in batch processing but has not made significant inroads into continuous manufacturing yet, although end users are interested in this application. Suppliers have not been able to supply it due to challenges with raw materials since the onset of the pandemic in 2020.
Other Utilities
Steam is not used for continuous manufacturing. Hot air is used for drying during the wet granulation process, but it is handled locally and requires heating. Nitrogen can create issues in the feeding system if it is used as a blanket. Vibration of compression machine equipment can migrate to the feeders. The feeders must be secured to the concrete column of the facility to eliminate harmonics from vibration, which can negatively impact the weigh cells and affect their accuracy.
Build Or Retrofit?
The following table compares and contrasts the advantages of continuous manufacturing in a new facility built from the ground up (greenfield) with the same type of operations in a suitable existing facility and infrastructure (brownfield).
The Case For Continuous Manufacturing
To sum up, the cost-effectiveness of continuous manufacturing is realized through ease of processing, continuous monitoring, and the reduction in manual operations that contribute to a streamlined process and reduced footprint compared to separate unit operations. Manufacturing in this way results in lower operating costs and less product loss throughout the manufacturing process.
About The Author:
Allison Cacciatore is executive director, facilities design and engineering, at Pharmatech Associates. With more than 15 years’ experience in facility design, engineering, and construction management, she has led multimillion-dollar renovation projects from feasibility and conceptual design through licensure for biologic and viral vaccine facilities. She led technical oversight in the startup of a filling line during the 2009 flu pandemic. Additional expertise includes risk-based validation and ASTM E-2500, and she was a consultant to the plastics and specialty chemicals industry. Cacciatore holds an MBA in management and a B.S. in chemical engineering from Lehigh University.