Evolution Of Large-Scale Chromatography Column Packing
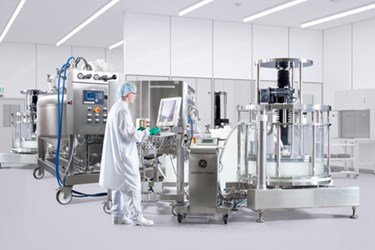
By Joakim Lundkvist, Cytiva
The biopharmaceutical market has become more industrialized and keeps expanding globally, both in volume and in a variety of products. There is continuous pressure to improve the efficiency and productivity of large-scale manufacturing by using breakthrough purification technologies. Chromatography has always played a crucial role in the purification of biologics. It has constantly evolved, and methods and capabilities have improved to reflect the industry requirements. This article gives an overview of how experience, innovation, and dialogue with customers led to the development of a platform that has revolutionized the economics of large-scale chromatography column packing.
Get unlimited access to:
Enter your credentials below to log in. Not yet a member of Outsourced Pharma? Subscribe today.