3 Building Blocks Of Organizational Agility For Pharmaceutical Manufacturing
By Hector M. Samper and Wolfram Mueller
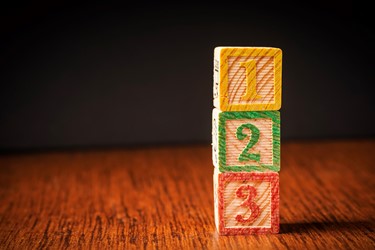
In Part 1 of this series we looked at why agility is so important to pharmaceutical manufacturers and their contract manufacturing and development organizations (CDMOs) and is key to reaching the next productivity level of project management. In this section, we dig deeper into the details of the building blocks of an Agile approach and the methods that can be used to achieve it.
Management Philosophies Essential For Agility
Any organization is as fast as its slowest process. If the focus is on increasing the speed of the agile teams while ignoring the rest of the organization, most likely it will create friction and prevent the organization from moving at an overall accelerated speed. It can be an ongoing struggle, and it can become a limiting factor to scaling agile in parts of the organization that are not organized in an agile way.
What is necessary to create an agile organization and shift the paradigm without interrupting the running of the business? The best way is to integrate the best practices of already existing and proven concepts and add smaller ingredients that make them all work perfectly together.
An agile model can be built on four management philosophies1 designed to adopt a new way of thinking or a mind-set based on agile values and principles. This mind-set or philosophy provides guidance not only to a holistic approach but also to the overall effectiveness of agile practices. These philosophies are:
- Theory of Constraints (TOC)
- Critical Chain Project Management (CCPM)
- TameFlow Approach
- Management 4.0
These management practices also offer methods, tools, and techniques to set up automated processes, standardized templates, and repeatable workflows, while providing a proven concept on how to transform the organization. In this article, we will cover the first three philosophies; the fourth philosophy, Management 4.0, will be the focus of the next (and final) article in this series.
Theory Of Constraints
The Theory of Constraints focuses on identifying the one factor that hinders a process, project, or company, resulting in delay or obstruction. In a project team environment, it is about identifying and managing the constraints of the project organization to improve the project cycle management by continuously striving to mitigate or eliminate the limiting factors. This is accomplished through:
- Simple guides to identify the constraint in complex systems
- Focusing on optimal flow through the constraint — quarantines optimal output
- Simple resource management and work-in-process control — abolish local optimization
- Simple robust planning and execution tools — focus on improving the lead time in each project
- Process of ongoing improvement — focus on improving the lead time for all further projects
The result of TOC is to ultimately optimize the output of the overall system by focusing on the constraint of the organization and subordinating everything under the need of the constraint.
The study A Review of Goldratt’s Theory of Constraints (TOC) — lessons from the international literature,2 conducted by Steven J. Balderstone and Victoria J. Mabin, states that organizations that implement TOC can achieve:
- Lead times: Mean reductions of 69%
- Due date performance: Mean improvements of 60%
- Revenue/throughput: Mean increases of 68%
This report was based on the collection of quantitative data across 77 companies on the application of TOC. The types of organizations covered by these cases varied from giant multinational corporations to industry leaders in the aerospace, apparel, automotive, electronics, furniture, semiconductor, steel, and heavy engineering industries, most of them focused on the manufacturing operations of each organization.
Newer testimonials3,4 indicate that TOC is more of a catalyst that brings all the long-standing invested efforts in Lean, Six Sigma, Agile, and leadership to work.
Critical Chain Project Management (CCPM)
This method emphasizes project execution to ensure that the goals of the projects are delivered as planned. It also provides a shining path to guide everyone’s decisions so that local optimization is avoided and everyone contributes to the overall goal — in less time, at lower cost, and without compromise.
CCPM helps keep the resources (people, equipment, physical space) required to execute project tasks on track. Critical chain derives from the Theory of Constraints based on methods and algorithms that focus on task order and rigid operational priority. CCPM has been credited with achieving projects with 25 percent to 50 percent shorter lead times than the traditional methods (i.e., CPM, PET, GANTT, etc.).
The main idea of CCPM is to remove the individual security of each task and allocate them at the end of the project. This security is called project buffer. It is used to assess the performance of the project. All project management is done by comparing the timely progress of the project with the buffer consumption — the fever curves (see Figure 1). When tasks are delayed, evident activities that are impacting more on the buffer consumption and actions in these activities bring focus to good management, increasing the chances of success in meeting the project objectives. It’s a powerful closed-loop corrective driver, as everyone is focused on regaining buffer mean lead times.
Figure 1: Fever Curve
The fever curve shows graphically the percentage of progress on the x-axis over time on the critical chain and the percentage of buffer consumption on the y-axis. Each dot shows the status of the project after a week or month — depending on the duration of the project. If the buffer consumption is higher than the progress, the curve goes into red and the team and organization must collaborate to come up with ideas to recover from the red to the yellow zone.
The aggregation of individual buffers from each work package at the end offers another big advantage. This aggregation of buffers is like an aggregation of risk insurances; hence, it is more unlikely that all risks occur in a worst-case scenario. So, by aggregating the buffers (insurances), it is possible to cut the overall buffer without losing security. Depending on the situation, and in combination with applying TOC on the portfolio level, this allows cutting the buffer by 30 to 50 percent.
Key elements include:
- Daily transparent project status – shown as the fever curve.
- Focus on measures to regain lost buffer – signals that show everyone where to focus to help (cooperation wins).
- Clear operating priorities for all based on buffer status – top management, project managers, resource managers.
The result is a highly flexible resource allocation and a sole focus on reducing the lead time of all activities in the critical chain of the projects.
The daily status and the fever curve are also key for enhancing cooperation across the project and the company.
It seems strange at first that everyday status is helping and not increasing the overhead, but in practice it is much easier to give a remaining duration status for each work package every day than conducting long and unproductive steering meetings. The daily routine leads to a situation in which flow disruptions are visible immediately and if these are addressed early, it relieves waste and burden for all participants — especially for the suppliers.
The fever curve itself focuses all participants on regaining buffer and allows them to delegate responsibility. Advanced companies have a clear understanding of the cost of delay in cost per day when a project comes in late. These companies hold budget buffer reviews to identify and implement project buffer regaining measures. In a case where the cost of the measure to regain a day of project buffer is lower than the cost of delay, it’s clear that the team can decide on their own — immediately. Team empowerment helps to relieve the steering board and top management from certain decisions and boosts the problem-solving process, so that the overall cost of the project decreases.
TameFlow
TameFlow5 is the equivalent of TOC, but at the team level; it also has its roots in Lean. It brings about breakthrough organizational performance innovation aimed at moving a team’s performance level from ordinary and average to outstanding. Hence, TameFlow is so called because it will act on or “tame” four fundamental flows that are present in an organization: operational, financial, informational, and psychological.3
Key elements are:
- Operations: How well are we delivering?
- increase flow efficiency through a shared understanding of the project business needs and apply the same rules across the team.
- Finance: How much value are we creating?
- focus on financial throughput rather than cost savings.
- Information: How well are we communicating?
- establish effective patterns of communication and interaction by getting the right information to the right place at the right time.
- Psychology: How happy are our people?
- create environmental conditions to cultivate teams with complete control over their situation, even in the face of high risk.
The alignment of the four flows will pull the team in the same direction to produce unanimous understanding and decisions; as a result, it creates a hyper-productive team. Hence, it promotes high integration of owners, suppliers, and stakeholders, iterative fast feedback loops, and adapting granularity of planning and specifications. TameFlow promotes the concept of profit sharing vs. transfer of liability.
On the team level and in the context of agile project management, the TameFlow task board is one of the key elements. The idea behind it is to reduce the work in progress of tasks in a team to its absolute minimum — ideally the number of open (in process and in review) tasks is lower than the number of team members. Once an optimum number of tasks is reached, the flow disruption can easily be identified, and the underlying process problem can be resolved.
An integrated team and task board will lead to breakthrough collaboration and increases in task completion rates of factors of three and higher can be achieved, resulting in lead time reductions of up to 60 percent.
Summary
To bring these methodologies to life, companies have to foster an agile mind-set while adapting and applying the right fit for projects and multi-project environments to bridge the gap between agile and classic culture. In the end, it is not about implementing new methods, it is all about changing the way of working — leading to a new culture.
To be successful, an organization has to change. But is it possible to change people? Part 3 will look at how to change a system so the people within it can change.
References:
- https://www.mckinsey.com/business-functions/organization/our-insights/agile-with-a-capital-a-a-guide-to-the-principles-and-pitfalls-of-agile-development
- https://pdfs.semanticscholar.org/df1d/d3592b42a7b50cb3cee8029ada3f67da6133.pdf
- https://inform.tmforum.org/digital-transformation-and-maturity/2019/04/andre-kriger-cio-telefonica-reveals-mix-critical-chain-lean-agile-techniques-aggressively-double-rate-project-deliveries/
- https://www.infoq.com/presentations/theory-constraints-scale/
- https://tameflow.com/what-is-tameflow/#a-way-to-improve-human-performance
Additional References For Learning And Implementing Agile Practices:
- List and comparison of current vendors of agile CCPM software - https://www.marris-consulting.com/en/points-of-view/critical-chain-project-management-software-solution
- “Hyper-Productive Knowledge Work Performance: The TameFlow Approach and Its Application to Scrum and Kanban (The Tameflow Hyper-productivity),” Steve Tendon and Wolfram Muller, J. Ross Publishing, 2014
- “The CIO's Guide to Breakthrough Project Portfolio Performance: Applying the Best of Critical Chain, Agile, and Lean,” Michael Hannan, Wolfram Müller and Hilbert Robinson, Fortezza Consulting, LLC, 2014
About The Authors:
Hector M. Samper is the principal and strategic advisor at Global Strategic Sourcing Solutions (GSSS), which provides expert advice to the biopharma sector, including strategies to transform and guide cross-functional business/procurement teams to generate maximum value throughout the operations life cycle. He has over 30 years of experience in capital expenditure and manufacturing operations, including indirect spend categories across North America, Europe, and Latin America. His recent experience at Sanofi included creating and leading the Strategic Vendor Management Office for the Global IT function, and heading the North America Operations and CapEx Procurement group. Prior to Sanofi, Samper worked for Amgen, Purdue Pharma, and Merck, where he held roles of increased responsibility in the global engineering, sourcing, and procurement organizations. You can contact him at hmsamper@aol.com.
Wolfram Mueller is principal and expert for agile multi-project management at Consileon Business Consultancy. He is dedicated to speed — either for projects or for changes. He has experience in over 550 agile and classic projects in IT and numerous kinds of mechanical and electronic engineering. The main theme in his work is flow — how to bring organizations to a hyper-productive state. As the author of many books and a well-known speaker, he has inspired companies to do more with less in a very short time. All this led to the invention of BlueDolphin, a community platform for self-organized changes based on the Theory of Constraints (TOC). You can reach him at Wolfram.Mueller@Change-Base.com. For a free, individualized report/benchmark of the symptoms and potential of agile project management in your organization, complete this simple, nine-question survey.