Biosimilars Producer, Alvotech, Finds Opportunities In Iceland
Source: Thermo Fisher Scientific
By Bruce Blau
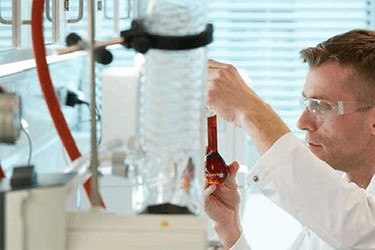
access the Article!
Log In
Get unlimited access to:
Trend and Thought Leadership Articles
Case Studies & White Papers
Extensive Product Database
Members-Only Premium Content
Welcome Back! Please Log In to Continue.
X
Enter your credentials below to log in. Not yet a member of Outsourced Pharma? Subscribe today.
Subscribe to Outsourced Pharma
X
Subscribe to Outsourced Pharma