A Life Cycle Management Approach To Developing A Supply Chain Strategy
By Carla Reed, president, New Creed LLC
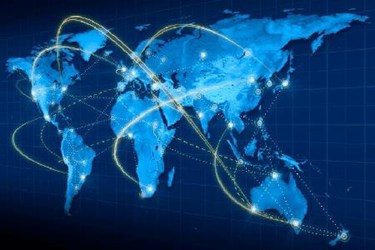
There is always a lot of discussion and debate related to the challenges faced by companies within the industry broadly described as life sciences. Price pressure for mature pharmaceutical products, shortage of supply for critical vaccines and other life-saving compounds, pipeline management for promising molecules and therapies — the list goes on. There are many proposed approaches to address these challenges, all with a common thread: Adopting a life cycle management approach will assist in identifying risk factors and constraints and provide structure and control, with a clearly defined methodology to identify and mitigate risk.
Pharmaceutical manufacturing is a very structured process, with well-accepted concepts like quality by design (QbD) and chemistry, manufacturing, and controls (CMC) embedded into standard ways of working. However, in a global environment where different manufacturing processes increasingly take place in different physical and geographic locations, there is one more consideration: The supply chain-related processes need to be considered as part of the true product life cycle.
For mature products, where there is a history of stability data for transportation, storage, and distribution, supply chain variability is less of a problem. However, for new molecules and compounds that are evolving from discovery through the phases prior to commercialization, logistics and distribution are in many cases an afterthought. A snapshot across a life cycle illustrates a variety of links in the value chain, all of which are connected by logistics activities, as seen in Figure 1.
Figure 1: Supply chain-related risks across the product lifecycle
As is apparent from the chart above, there are many risk factors that could impact the security of raw materials, components, and, ultimately, finished pharmaceutical and biologic products. This challenge is further complicated by the fact that product development is a long and complex process, with different organizations engaged at different stages across a product’s life cycle.
Most organizations have a structured approach to the transfer of products from one location to another, either as part of product development, ramp-up to commercialization, or extension of production capabilities from one facility to another. In most cases, the focus is on the chemistry and production requirements. Taking a broader view to include risk factors related to surety of supply for all materials and components, including packaging, labels, and related literature, will provide a more robust risk assessment approach.
Figure 2: Supply chain risk assessment for life cycle management
It is important to develop a supply chain strategy concurrent with the product development and commercialization cycle — a strategy that takes into consideration risk factors, likelihood, and impact. This makes it possible to recalibrate processes in a proactive manner versus remediation in the event of a supply disruption.
Key Considerations In Developing A Supply Chain Strategy
Any supply chain strategy should give consideration to operational factors that could impact the flow of goods, materials, and supplies across the product life cycle.
Procurement Relationships
During product development, a variety of raw materials and compounds are sourced, in many cases from a sole source. During the product development life cycle, these sourcing relationships become critical; therefore, it is imperative to ensure that suppliers, in particular small and specialized suppliers, are able to meet increased demand once a product is approved and commercial production is initiated.
The different functional structures of development organizations and commercial manufacturing environments, where there are different processes, procedures, and stakeholders, raise additional concerns. After commercialization, there is increased pressure to recover investment in the new product. The focus changes from approval to profitability and all factors that impact margins. Production efficiencies and yield are a high priority, but so are the costs of raw materials, components, and packaging, all of which impact the overall unit cost. Procurement personnel are compensated and rewarded commensurate with their success in reducing the total cost of goods; in many cases this can result in changes in suppliers, supply location, packaging configuration, transportation mode, and routing. These are all factors that could have a negative impact on the quality and efficacy of the material or product being procured, stored, and distributed.
Manufacturing Environment
Successful technology transfer — whether from a laboratory environment to manufacturing within a single site or to a network of internal and external manufacturing locations — is a major risk factor normally addressed by a cross-functional team of experts. Biologic manufacturing facilities that take advantage of disposable technologies, such as bioreactors, bags, tubing, and storage devices, need to evaluate the risk factors related to these disposable units, with a focus on leachables and extractables.
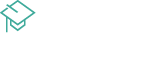
Lower your risk of issues when performing a technology transfer. Attend the webinar:
Improving Product Quality During Technical Transfer – Minimizing Risk, Maximizing Results
Manufacturing Components
Disposable components used in biotech manufacturing normally comprise both flexible and rigid components. Protecting these items during storage, handling, and transportation requires designing appropriate packaging. Considerations include the folding of flexible items such as tubing, as well as providing protection for rigid components that could be damaged. In addition, the design should consider the removal of disposable components in a sterile environment, and the related installation by users, who, in many cases, are wearing protective clothing and gloves.
Product Packaging And Protection
During the transition from clinical trials to commercialization there are additional factors related to the dispensing unit and format. In many cases, product managers are responsible for the packaging specification and design, based on dispensing unit, marketing initiatives, and promotions. The focus is on the primary packaging, labeling, and literature. In the case of biologics, the subject of leachables and extractables at the unit level should be addressed. In addition, it is important to consider any protective packaging that may be required for storage and distribution, especially for products and materials that are sensitive to environmental variations.
Approaches To Address Challenges Early In The Product Life Cycle
The most effective approach to addressing supply chain-related issues is to establish a cross-functional team to evaluate all the constituents and stakeholders across the product life cycle. The links in the life sciences supply chain network should be identified, with task level and functional process flows mapped to represent a holistic model. Typical links and functions within this extended network include, but are not limited to:
- Sourcing of materials and services (inbound activities)
- Manufacturing and production (primary manufacturing, secondary manufacturing, contract/toll manufacturers)
- Delivery/logistics and distribution (outbound activities)
Figure 3: Multiple activities prior to commercialization of pharmaceutical, biopharmaceutical, and other life sciences products
Borrowing A Chapter From Compliance Guidelines
Pharmaceutical manufacturing operations are subject to inspections by regulatory agencies. The focus of these inspections is on practices, processes, and procedures to confirm that adequate systems and controls are in place to ensure that the product is produced and packaged appropriately. This safeguards product integrity, quality, and efficacy and ensures that the product is intact when it reaches the patient. Extensions of good manufacturing practices (cGMPs) include guidelines and recommendations for best practices for storage and distribution — commonly known as good distribution practices (cGDPs). When conducting inspections, regulators are looking for the same level of quality and control for internal business practices and external supply chain processes. Guidance documents have been written and published by regulatory authorities, pharmacopeias, scientific organizations, and trade associations, as well as communities of packaging companies and transportation providers that service the life sciences industry. These guidelines should be consulted, adopting best practices in supply chain-related processes.
An excellent guideline has been developed by the USP. Chapter <1079> Good Storage and Distribution Practices for Drug Products describes practices to ensure that drug products (medicines) reach the end user (practitioners and patient/consumers) with their quality intact.
Figure 4: Conceptual good distribution practices structure
Product realization (see Figure 5 below) is part of an ICH Q10 life cycle model that describes the process of developing an active ingredient, the finished product, and the associated manufacturing activities. The objective is to establish a consistent and predictable process that will ensure that a high-quality product can be manufactured.
Figure 5: ICH Q10 lifecycle quality management
Steps To Ensure A Predictable Supply Process
As an extension of — and consistent with — this approach, the supply chain strategy should be developed to ensure a consistent and predictable supply process, integrating activities and outcomes of all participants, to include suppliers and/or producers of raw materials, intermediates, APIs, drug product, and associated packaging materials.
Step 1: Conduct risk assessment by taking a structured approach to look at the risk factors, likelihood, and impact.
- Involve cross-functional entities to ensure that all factors are taken into consideration
- Look at each of the key phases across the product life cycle
- Do a “what if” scenario analysis – evaluate things that could impact the ability of supplier to supply
- Evaluate the impact of changes in packaging based on different configurations of ingredients – API, environmental conditions, related factors
- Develop cause and effect (fishbone) models
- Evaluate cause and effect – root cause and analysis
- Formalize into process models
Step 2: Develop a mitigation strategy and approach.
Using the baseline from the root cause analysis, look at risk factors, contributing negative activities and constraints, and approaches to reduce risk or remediate in the event of a supply disruption.
Table 1: Summary of Key Risks and Mitigation Approaches
Each of these stages in the product life cycle is subject to potential issues that need to be planned for, such as changes in source of supply, variations in transportation plans or mode of transportation, and exposure to environmental hazards. Regulatory requirements are also subject to change, and nothing should be left to chance. It is therefore appropriate to review supply chain models for critical materials and products to ensure that nothing has changed that could impact the flow of goods, information, and related documentation.
Conclusion
Supply chain management and control includes the participation of many different entities and stakeholders. Adopting a life cycle management approach and developing holistic process models is one of the best ways to identify each of the critical links in the chain of custody. The inclusion of both internal and external stakeholders in initial and subsequent reviews will facilitate the development of a robust framework for supply chain capability and control.
About The Author:
Carla Reed is a supply chain professional with more than 20 years of experience in supplier engagement, manufacturing, emerging market development, outsourcing, global trade, regulatory compliance, storage, and distribution. Her firm, New Creed LLC, provides change leadership to facilitate sustainable solutions, providing hands-on experience in all aspects of supply chain operations. You can email her at carla@newcreed.com