Your CDMO And Your Glass Vials: Best Practices For Development

By Louis Garguilo, Chief Editor, Outsourced Pharma
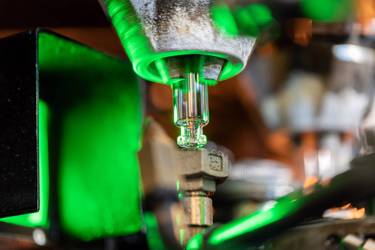
Nowadays, at the mention of “vials,” we all jump to questions surrounding sufficient supplies for COVID-19 vaccines, if and when they arrive.
If that is your immediate interest, you’ll want to read our companion editorial coming out next week; it will include mathematically derived analysis for your consideration.
But thoughts of vials for Outsourced Pharma readers more normally pertain to your own drug develop program needs for these safe containers.
And in the context of your outsourced model, you should also consider best practices for coordinating your vial needs and supplies with your CDMO partners.
For that advice, I decided to ask one of the biggest glass producers in the world.
Basic Glass Formations
Fabian Stocker is Vice President Global Strategy & Innovation - Pharmaceutical Systems, for SCHOTT. Speaking from his office in Mainz, Germany, he starts by saying that unlike for your drugs themselves, raw material sourcing need not be in your risk column when it comes to your glass containers.
For example, widely used borosilicate glass was invented by SCHOTT over 100 years ago, and is produced in fully-owned plants in Brazil, Germany, and India, and says Stocker, “in future in China as well.”
That stream of raw material becomes the tubing – open glass cylinders – that then are cut and shaped into various vials and containers. That cutting and shaping is accomplished at “globally distributed converting plants.”
A segment of SHOTT’s tubing is output for its own clients’ needs, and the other segment shipped to its glass competitors.
Once the glass has become precise geometric vials, they are filled by pharma companies themselves, or at the CDMOs Outsourced Pharma readers select as partners.
Bring In The CDMOs
Let’s begin by stating Big Pharma typically operates its own packaging development departments; they know what packaging they need. If these companies are outsourcing, they normally direct their CDMOs to purchase specific products from specific vendors.
However, for those of you not able to predetermine as precisely, Stocker says a good CDMO can also take on an initial role of trusted advisor in this realm.
The next step, he adds, is for “biotechs and those assisting CDMOs to come to us with ideas, and for our advice. We should form a triangle – drug sponsor, service provider, and glass provider – to determine the most optimal path forward.”
This triumvirate doesn’t simply settle on container/stopper solutions and have the requisite products shipped to the fill-finish site. A close project-management relationship also forms, and can include the glassmaker visiting and working with the scientists and engineers at your CDMO.
“You need to run product qualifications as well as line validations, and ensure the process is running according to regulatory guidelines,” explains Stocker.
“We work closely with the CDMO/fill-finish organization to advise on what might be important for them to focus on. If they are running previously validated processes, it might be as simple as a steady flow of validated packaging. If there are new types of packaging, and new validation testing to be done, we need to stay closely interlinked.”
3 Best Practices
Building on the above, Stocker offers three best practices for Outsourced Pharma readers.
1. Early Glass
Biotechs typically start thinking about packaging design in phase two of product development.
“The best practice would be to initiate that process earlier. Packaging is already involved when you develop the API, when you develop a formulation – the formulation has to be stable with the packaging and not interact.
“Consulting with your packaging partner early on can take out development risks that might relate to a potential interaction between the drug and the container. We have roughly 600 different measurement tools in our pharma analytics division.
“Nobody wants to be approaching launch and realize, ‘Oh no … I have a problem with the packaging.’ Partners can help you understand the metrics and analytical practices, and you should bring that expertise early into the development process.”
2. Project Management
How the biotech, CDMO and vial provider set up project management can be case-by-case, but there are best practices.
“If you have a development project with a drug company and chosen CDMO, you should have a three-way NDA.
“Then you'll generally establish some form of a joint steering group, aligned to ensure all the product-container interfaces are working, and not interfering. This is particularly crucial when we talk about newer packaging, or development of all-new packaging.”
“However, these projects are often very confidential – not only the project but the partners as well. So it's clear we have to honor that confidentiality. Still, as soon as possible, the parties involved should come together as much as possible to ensure the best results in developing the right packaging for the right drug.”
3. Stay Standard
Much of what has preceded adds up to this advice: “Determine you want to work with a standardized container.”
This is a product manufactured according to well-established and proven ISO standards, and “in terms of geometry, are vials that run effectively with the global machine suppliers and on various production lines.”
“Particularly for sterile product,” continues Stocker, “you want vials that offer you a wider option of fill-finish providers, and options for the providers you select.
“We have done specification work on over 50 lines around the world. We advise biotechs and pharma alike to work with the standardized packaging portfolio. Practically speaking, that is in fact an offer of high quality, because we have already done the pre-validation work with the filling supplier.”
Finally, readers should recognize we have not covered the intricacies of stoppers and seals for vaccines. Let it suffice for here to say your glass-vial producer will be a wealth of information for those aspects as well, which can be complicated in their own regard.
“At the end of the day,” concludes Stocker, “biotech and pharma customers want an easy-to-operate system. Glass vial providers try to ease the process to get there.”