COVID-19 No-Fly Zone: A Year And Counting For Biopharma Supply Chains

By Louis Garguilo, Chief Editor, Outsourced Pharma
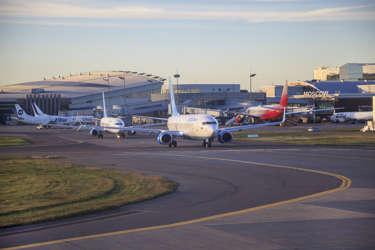
We’ve bought ourselves a year or so of commercial drugs.
Industrywide, a year to 18 months is the elasticity most drug companies have intentionally inserted into supply chains before real – not fears of, but real – shortages of commercial drugs could potentially start to appear. Lean philosophies, just-in-time techniques and CDMO “flexibility” not withstanding, this practice of an elongated “safety stock” remains in play throughout the world.
One industry source told me: “Actually, I don't think anybody has less than a year of finished product warehoused. At the companies I’ve worked, 15 to 18 months was typical for all commercial products.”
We are not talking here about low-cost, low-margin generics, but the name-brand leading medicines of our time.
So that’s a bit of the good news. No pharma company has reported any shortage of their leading medicines to date that we are aware of at this writing.
Less positive: As global (and domestic) flights on commercial airlines are curtailed, also grounded are large amounts of that safety stock of drug substance and product mentioned above.
My reporting has turned up this infrequently discussed fact: Pharma flies product around the world in the cargo hold of the same flights you and I take for our leisure and business.
The immediate challenge facing outsourced and overseas-dependent drug substance (API) and product supply chains is not factory shut downs or production schedules. It is governments and/or your favorite airlines curtailing or outright banning flights to and from countries, such as Italy and Singapore (which along with China, are locations we’ll discuss a bit more momentarily.)
“Right now, the coronavirus situation is more about transportation than manufacture,” says one biopharma executive with a global supply chain for both development and manufacturing.
“Pharmaceutical companies by and large keep at least a year's worth of drug on hand, and start getting nervous when it gets down below six or eight months. For most companies, manufacturing is still a concern down the road.”
Additionally, many companies have intermediates and product stockpiled in different locations. “It depends on the drug and the company philosophy, but for the pharmaceuticals in the U.S. and Europe, there is still some time to figure things out,” this executive told me.
“My first concern is going to be transportation specifically. If this continues for more than a year, then I think it'll be getting products manufactured that will really be in play.”
No-Fly Countries That Matter Most
Human suffering and economic unrest in any country is of equal concern. At the same time, those countries where the coronavirus has immediately taken hold couldn’t be worse for the pharmaceutical industry. We’ve been hit square in the supply chain.
First of course is China. As we all know, many dozens of API manufacturers are located in the greater Wuhan region alone. Our global pharma industry is in many cases dependent on raw materials from China.
Here are two other countries of concern to drug supplies.
Singapore
Biopharma professionals regard coronavirus-restricted Singapore a second country of major consequence in Asia.
Singapore plays an outsized (and often unrecognized) role in international drug supply chains. To name a few big players with production facilities there: Genentech, GSK, Merck, Novartis, Pfizer, and Sanofi-Aventis.
Billions of dollars of pharma product is shipped from Singapore each year to locations such as Switzerland, the Netherlands, and Japan. Singapore also serves as an “entrepot” for collecting, warehousing and re-exporting pharmaceutical imports to locations around the world.
Last week a biopharma execute confided: “I suspect soon it will be difficult to get materials in and out of Singapore. A number of CDMOs as well as pharma companies have huge warehouses there. It serves as a depot for pharma distribution in Asia.”
Italy
One supply chain professional is especially concerned with the COVID-19 outbreak in Italy.
“We have some final product in Italy,” she explained. “This is now a country where flights may be greatly curtailed from its two main airports: Rome and Milan. So how do we get product out?”
“A lot of pharmaceuticals are not transported by cargo planes unless the volume is extremely large, and definitely not by ship because that's just too slow. Much of what my company transports around the world is on passenger planes. For me, the issue is going to be if passenger plane traffic in the world continues to slow down. Freight forwarding could be significantly curtailed quickly.”
Back To China
COVID-19 has brought out a national chorus of “We warned you.”
I along with Outsourced Pharma readers and contributors have previously voiced strong reservations about the lack of pharma manufacturing in the U.S., and supply-chain dependence on China.
Doesn’t this coronavirus outbreak – substantially and in such an unfortunate manner – make our case: We are at unnecessary risk.
Here’s how one professional at a U.S.-based biopharma company expressed it.
“At one level, I agree. But for me, it's diversification more than just get it out of China or bring it to the U.S.
“My entire career in the biotech industry the saying has been, ‘If you're going to build a second manufacturing site or warehouse, put it on a different fault line.’ If there is a large earthquake in the San Francisco Bay area – think the Genentech, Gilead or other facilities that might go down.
“The issue then is not just getting it out of China, but to have manufacturing in different geographies, so that you are effectively mitigating risk. There are risks associated with the U.S. and Europe as well. A few years ago hurricane Maria devastated Puerto Rico and a large manufacturing base for the pharma industry.
“Another example is Japan. If you want to buy an amino acid for making media, two companies there – Kyowa Hakko and Ajinomoto – are by far the largest manufacturers. Now the Kyowa Hakko facility is experiencing issues with the Japan regulatory body. If Japan becomes another country that gets a significant COVID-19 quarantine – not to mention the large pharma companies and CDMOs there – what happens to the global industry?
“So without diminishing the terrible human situation, in some ways the coronavirus is just another example of an inherently fragile supply chain for medicines and support.”
One apparently at risk to commercial aviation.