Building In Boulder – A Biotech Finds A Manufacturing Base

By Louis Garguilo, Chief Editor, Outsourced Pharma
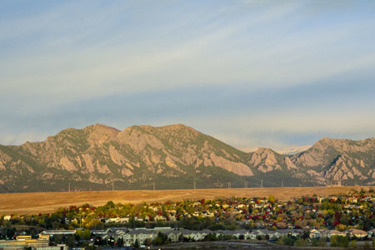
In part one, with two of the four Umoja Biopharma cofounders, we noted the company is an intriguing mix of sponsor/service provider, outsourcer/builder, and platform/technology promulgator – primarily within the cell-therapy space.
In that earlier piece, we unpacked much of the strategy involved – a multifaceted business model that while intriguing, is not so dissimilar to some of the evolving models Outsourced Pharma readers may be a part of.
If any of you have thoughts of building internal development and manufacturing facilities, this is a segment of our discussion to focus on.
And focus is an issue here: many pieces to an organization can put employees in many minds. However, CEO Andrew Scharenberg fights may assertion of diffused focus, and makes the organization’s business objectives clear:
UB-VV200 is Umoja’s lead therapeutic candidate which aims to generate lasting remission for patients with gynecologic cancers by harnessing the synergy of the company’s technology platforms (UB-VV200 anticipates IND clearance by Q4 2023).
Nonetheless, Scharenberg adds, considering the current stage of the company, and taking into account economic conditions making it difficult to raise additive capital, “understanding you have technology valuable to others, and how you can partner that technology as a source of programs and assistance to other developers, has to be part of any platform-company strategy.”
Under his guidance, Umoja is building a state-of-their-art lentiviral development and manufacturing facility. Earlier, we spoke about why Umoja has decided to build. Here Crisman tells us what such a facility entails, and how it took shape where it did.
Rocky Mountain High-Tech
“We chose Boulder strategically,” Crisman says. “Everything's an equation to me as an engineer. Looking at where to build, the cost, and then the right talent to actually run a facility.”
When Umoja started looking around the U.S. – “South San Francisco, Seattle, Boston, kind of the top tiers” – Crisman found the skilled workers and the knowledge were present, but so is a high turnover rate, it’s expensive to build, “and really expensive to operate there.”
The better option for an advanced development and manufacturing facility for next generation therapeutics – and a company creating its own technology platforms – turns out to be in a scenic small town called Louisville, in Boulder County, Colorado.
“Fantastic little town,” says Crisman from an energetic coffee shop in the town. “It's a great place to live and work.” We’ll find out why that’s particularly important in a moment.
Umoja is partially building out an existing shell of a ~150,000 square-foot facility within Louisville's Colorado Technology Center. The location will eventually house labs, offices, and most importantly, a manufacturing space for lentiviral vector production. The first manufacturing run of clinical material for UB-VV200 is expected to commence the second half of this year.
Umoja already had lab space in Boulder that’s helping facilitate the set-up of their new processes for clinical applications in the new facility.
Regarding the size of the facility, an important lesson:
“We strategically chose a space larger than we needed for our initial clinical needs, because in my experience, I've only ever run out of space,” says Crisman.
“We're bullish on our platforms and our products, and plan for success. We've decided to maintain half of it as a shell for future clinical or commercial needs, and the other half is being fully built out for clinical-phase GMP manufacturing.”
The original facility was utilized as a storage warehouse for the large technology park that houses it. “Available biotech space was non-existent, so we decided to move forward with a shell space” says Crisman. A new developer that was looking to expand into biotech entered the park as part of a development package within the Boulder County area.
“They started asking if they could use it for more than a warehouse, just as we started looking for options about two and a half years ago,” explains Crisman. “We entered conversations with these new park owners, and worked together to build out a high-tech, high-quality lentiviral manufacturing facility.”
Today, that facility is called The Colorado Laboratory & Innovative Manufacturing Building (The CLIMB), and Crisman’s explanation leads to some questions – starting with the workforce and logistics.
Nice Place, But The Workforce?
Crisman tells me when I ask that there is “hidden talent here,” in terms of workers who have experience operating and running a GMP manufacturing facility.
He paints a much brighter picture than many other executives I’ve spoken to over the past two years or so regarding hiring.
“Recruiting has been fantastic,” he says, “perhaps enhanced by people looking at various living options in the past few years.”
“Quality of life, sunshine, and cost of living is a bonus for recruiting and maintaining workers."
The skilled worker pool is helped, he says by the strong academic presence of the University of Colorado, and Colorado School of Mines, "right out our backdoor,” he says. Additionally, “the University of Colorado Anschutz Medical Campus has done an incredible job at building out a cell-and-gene therapy center of excellence that has attracted top talent in the research space.”
All that currently adds up to a facility with 40 employees and rising.
Regarding transportation and related logistics, Crisman says, “That was all part of the equation.” The facility is “right off a toll road with zero traffic to the Denver International Airport. Roughly about a 30-minute drive.”
He adds the facilities are centrally located in the U.S. – “a two-and-a-half-hour flight anywhere we need to be to deliver the technology. Especially advantageous for autologous products.”
So location for its internal development and manufacturing was a key in many regards for Umoja. But we aren’t quite finished with our discussion. In a final part, Crisman will provide some solid advice for when instead of building, you are locating CDMOs who can serve as your external partners.