Robotic Pharmaceutical Labeling Cell System: HERMA 211R HC
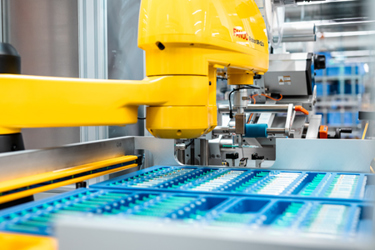
With the robot-assisted labeling cell 211R HC, HERMA shows how challenges in wrap-around labeling of label material can be solved more effectively. Discover the advantages of our HERMA 211R HC labeling solution.
What Makes The 211R HC Labeling Cell So Beneficial?
- The use of robotics optimizes efficiency, due to reduced downtime and consistently high performance over a long period.
- It minimizes operator-based errors, such as those resulting from a loss of concentration during monotonous, repetitive tasks.
- The 211R HC also helps to reduce costs, for example by eliminating time-consuming manual reworking.
- The products are fed in and removed via an innovative drawer system. This enhances process reliability by maintaining a closed system that does not need to be opened during operation. This design ensures products are fed in and removed efficiently, minimizing the risk of errors and contamination.
- The 211R HC labels up to 20 products per minute - and is 25 percent faster than a comparable conventional, semi-automatic labeling machine.
- The integration of robotics allows cost-intensive workers to focus on higher-value activities ensuring better operational continuity even during staff shortages.
- In terms of product security and machine safety: the robotic labeling cell can be programmed to automatically comply with certain labeling regulations and standards.
- For frequently changing products with varying dimensions, optional format parts with a quick-change unit are also available. This feature enables fast and efficient changeovers, reducing machine downtime.
Labeling Cell With Robot - Ideal For Small Batch Sizes And Complex Shaped Products
The labeling cell is specially designed for pharmaceutical products such as small vials, pens, syringes and cartridges. These are usually non-stable and irregularly shaped. In small batch sizes these type of products have usually been labeled by a semi-automatic labeling machines, such as the conventional wrap-around labeler 211 HC. The new labeling cell however, significantly automates this process, enhancing efficiency and precision and thus represents a pioneering labeling solution.
The Development And Functionality Of The 211R HC
The 211R HC is the result of a developmental partnership with Fanuc and Weiss Robotics. With a special emphasis placed on minimizing the footprint, the design incorporates a robot with an ultra-compact base and the world's smallest servo gripper integrated. HERMA collaborate with all leading robotic suppliers and develop solutions for a wide range of labeling applications. Thanks to its innovative design and collaboration with leading robotics providers, the HERMA 211R HC enables seamless integration into existing production lines. This increase in efficiency and high labeling precision make it an ideal solution for the demanding labeling applications of medicines and pharmaceuticals. With the 211R HC, you can optimize your labelling processes while ensuring the safety and quality of your products.
Step 1: Non-labeled products are fed directly into the trays of the closed labeling cell via a drawer. The safety cover does not need to be opened for this. This innovative approach boosts efficiency, increases safety and ensures a smooth workflow.
Step 2: The robot removes the products individually from the tray and places them precisely in the labeling station, which is equipped with a HERMA 500 labeler.
Step 3: The product is rotated in a motor-driven roller prism and the label is dispensed precisely onto the product at the peel-off edge, with or without label product orientation.
Step 4: After the fully automatic labeling process, the robot places the labeled products under a vision system or sensor to check the presence and variable data of the labels.
Step 5: The robot places confirmed products into a designated carton or outer tray. When it is full, it can be easily replaced using the drawer system without interrupting the labeling process.
Step 6: Unconfirmed products are placed in a separate tray.