How To Minimize API Loss: A Case Study In Aseptic Fill/Finish
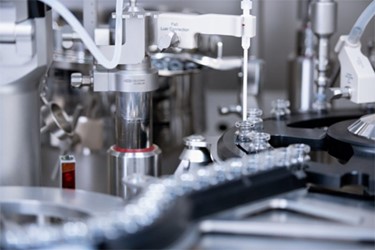
With API (active pharmaceutical ingredient) values continuing to climb as production scales conversely drop, it is time to rethink our aseptic filling processes to minimize API loss. The rise in biologics and personalized medicine has led to APIs with significant upstream production costs, where even the smallest loss of API at the fill/finish stage can waste thousands of dollars and potentially result in a short manufacturing lot. Fortunately, new advances in filling technology offer solutions that minimize lost API. To maximize API volume utilized while also reducing risk, intelligent equipment and process design are key. In this case study, we highlight the choices made by Argonaut Manufacturing Services when designing their recently installed Bausch + Ströbel VarioSys aseptic filling line. With equipment lead times surpassing three years from order to validation, it is critical to design the right high-yield line from the start of your project.
Get unlimited access to:
Enter your credentials below to log in. Not yet a member of Outsourced Pharma? Subscribe today.