How To Integrate Continued Process Verification & Annual Product Review For Biologics
By BioPhorum
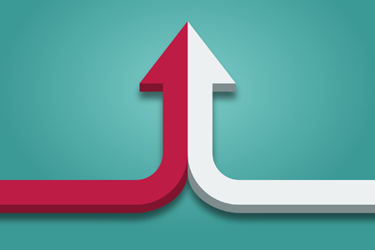
Evaluating the health of biologics manufacturing processes has evolved since it began more than a decade ago. Current practice is described in the 2011 FDA guideline Process Validation: General Principles and Practices and in the 2012 European Medicines Agency (EMA) Guideline on Process Validation and is now commonly known as continued process verification (CPV).
The FDA and EMA guidance emphasized the importance of pharmaceutical manufacturers using CPV as an integral part of their process validation life cycle to provide ongoing assurance that the process is a tool for identifying opportunities for continuous improvement.
CPV requirements are similar to those for evaluating the quality standards that determine the need for changes to manufacturing or control procedures as part of the annual product review (APR) report. However, while many companies have modeled their CPV reporting on the APR reporting process, irrespective of good manufacturing practices (GMP), often they have not fully integrated the two processes, leading to inefficiencies. Also, many companies have not yet taken advantage of the opportunity that a fully validated CPV informatics system provides to further streamline the reporting processes. Current CPV practice varies among companies for various reasons, e.g., the level of process knowledge acquired before engaging in process validation activities and the use of automated vs. manual data acquisition.
To determine the different levels of maturity of CPV and APR practices across the pharmaceutical industry, BioPhorum surveyed 15 member companies. The main findings were:
- All companies write formal reports to summarize the findings of the CPV program and many write multiple CPV/APR reports each year.
- 60% use an informatics system to provide most of the data, charts, and statistical analysis included in the CPV reports. The remaining data is generated manually.
- 40% still use manual methods to create full CPV reports.
- Only 50% have aligned the review period of their CPV to that of their APR. However, more than 75% referenced the most recent CPV report as part of their APR report.
- More than 50% have at least some difference in the scope of parameters covered by CPV and APR, with CPV generally including more parameters.
- Organizationally, the CPV workflow is typically managed by manufacturing and/or process development functions, while the APR is managed by the quality unit.
These findings reveal opportunities for improving the efficiency of CPV reporting practices and generating the associated sections of the APR report.
Using information gathered in the survey, we mapped the common workflows for CPV and APR activities across most companies surveyed. We found that workflows are duplicated as the CPV and APR reporting periods are not aligned and/or CPV reports can cover shorter review periods than the APR. Most data acquisition activities use manual data entry systems, although independent, semi-automated data acquisition systems are sometimes used in manufacturing. Quality events (manufacturing or quality control deviations/investigations) are generated manually during manufacturing and testing activities. However, the APR workflows are not integrated to leverage information from CPV workflows.
Future State Of CPV And APR Business Practice (The Next Five To 10 Years)
There is a future state that could maximize the benefits of the CPV process. With the availability of automated facilities, a digital strategy, deployment of process analytical technologies, and well-characterized processes, future manufacturing platforms should be based on continued online monitoring of parameters and product attributes. This approach, together with the implementation of integrated manufacturing execution systems, increases process oversight and enables the proactive identification of signals.
Documentation supporting process control and trending could be automatically generated to support both CPV and APR requirements. Also, CPV and APR reports should be synchronized to maximize resources, especially when signals identified are corrected in real time (or near real time), either by triggering an external intervention request, traceable within the quality or the business system, or by a feedback loop control.
Future CPV business processes could be tailored to mitigate known risks by monitoring the parameters, which would create immediate benefits for manufacturing control. For some companies and/or legacy products (where almost all process and product data are manually monitored and trended without any validated informative systems and risk assessment), the emphasis should be on identifying and categorizing process robustness indicators. This should use comprehensive risk assessments or failure mode effect analysis that uses process knowledge gained from ongoing commercial experience. This risk-based approach helps increase the program efficiency by reducing noise and prioritizing the response.
When companies establish a validated informatics system for data trending and risk assessment, it could also be used for their legacy processes. Considering the global digitalization trend, CPV of the future can expect that the entire pool of production data could be assessed in near real time. This would reveal significant interconnections, allowing process parameters to be categorized based on their impact. Your company could then prioritize resources and focus monitoring efforts on key parameters.
Bridging Current And Future States Of CPV And APR Business Practice
Robust, validated informatics systems capable of performing various CPV functions are critical to support the generation of one annual report per product. Systems capable of automated data collection, evaluation, and alert generation help in timely risk assessments and investigations. The real-time data review enabled by implementing digital manufacturing will ensure robust process controls and enhanced business efficiency. Connecting different systems (e.g., electronic batch records) to an automated trending system presents its own challenges that the current industry digital transformation must face. For example, creating data systems to accomplish the CPV tasks may need a significant investment of money and resources. You should evaluate carefully the business needs along with your compliance requirements.
In the period between the current state and the digitally enabled future state, there are some practical solutions that can be used as incremental improvements to help improve the efficiency of the overall CPV program and APR reporting. All changes must be made with the understanding that the new process must follow all cGMP requirements to maintain compliance.
Legacy Processes And Quality Control Labs
To improve the business efficiency of the CPV and APR workflows, it is important to lock historical verified databases in a dedicated data repository. New data coming from paper-based sources can be added to the same database. The data could be connected to analytics systems to enable automatic trending of process parameters. Aligning the timing of generating CPV and APR reports is imperative for efficiency.
Digitally Mature Facilities And Quality Control Labs
Adding an informatics system to pull together the data from these isolated systems can help increase the value obtained from the existing digital investments. However, until an informatics system is deployed, manually extracting data from the isolated systems following a GMP-compliant business process can help bridge the gap. As with legacy processes, aligning the timing for generating CPV and APR reports is key to avoiding duplication and inefficiencies.
Signal Review And Documentation
Transition to a future state could be bridged with a signal review business process. Subject matter experts would make a first assessment of signals, escalating potential violations without waiting for a periodic signal review meeting, which could act as a secondary assessment. The meeting should be attended by subject matter experts, staff from quality assurance and manufacturing operations, and the business owners of the systems managing the trending and CPV programs.
A risk-based assessment of alerts to determine the need for investigations will help prioritize use of resources. To classify the risk of parameters, a standard nine-box risk matrix that evaluates severity and occurrence is sufficient. Using digital quality management systems for documenting investigations is common, and CPV investigations can take advantage of these systems, which can also generate validated reports for use in the APR.
Finally, a centralized online location for CPV reports is required, accessible by APR report authors. Web-based interactive platforms could also provide the location for CPV data trending and statistical analyses that can easily be referenced by APRs.
Regardless of your company’s state of automation and digital transformation, it is important to switch your process monitoring and trending approach from an end-of-campaign mindset to one close to real time to ensure that signals are addressed batch to batch. This is possible by implementing agile and compliant business practices.
Conclusions
CPV and APR practices are key activities to maintain a state of control and identify continuous improvement initiatives. Both practices also represent regulatory requirements/expectations.
CPV and APR workflows are often redundant and disconnected, making both inefficient. Yet, there are opportunities to improve and align both activities. Until digital transformation in manufacturing can leverage real-time data review and optimize efficiencies between the practices, small optimization initiatives can mean significant steps in the right direction.
Using equipment automation and feedback control, implementing validated trending tools, and centralizing trending reports via web-based interactive platforms are the first recommendations for companies that would like to transition toward a fully digital solution.
To read more on this, check out BioPhorum’s recently published Guide to integrating continued process verification (CPV) and annual product review (APR).