Fit From Development To Manufacturing – A Successful rAAV9 Scalability Study In A Suspension Process Using HEK293
By M. Boscher, J. Wagner, S. Petrik, J. Babic, B. Larena Carnio, D. Bitnel, S. Ndonwi, R. Staffler, J. Weizenegger, E. Tsiaousi, C. Mantzoros, T. Kloetzler, M. Magerl, M. Gora, A. Heinlein, S. Henze, C. Zach, S. Ritter, A. Schulze, A. Schulze, A. Schoberth, M. Langhauser, K. Heller, M. Hoerer, and A. Youssef
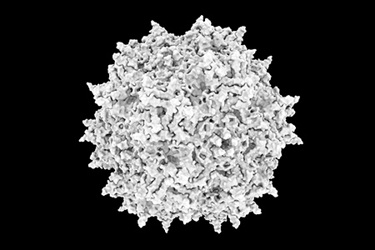
Design of experiment (DoE) approaches in robust scale-down devices, such as small-scale bioreactors, allow for product-specific optimization of modular platform processes with speed and reasonable development costs. However, scaling up to larger bioreactors presents challenges, as maintaining consistent conditions such as mixing time, power input, impeller tip speed, and oxygen transfer rate (OTR) across all scales is not always feasible.
Staying within a single provider's system can be a good starting point, as many systems offer similar vessel height-to-diameter ratios, impellers, baffles, and sparger designs. But, as is often the case with sensitive biological systems, this may not be sufficient. Several process-specific factors, such as mixing time, power input, impeller tip speed, and OTR, cannot be kept constant across all scales, and additional scale-dependent factors—like process parameters and cell seed train volumes—also impact cell performance, yield, and quality.
The goal of this study is to demonstrate the scalability of AAV productivity and the consistency of product quality across different bioreactor scales using Ascend’s AAV manufacturing platform. Critical quality attributes, such as full/empty ratio, residual plasmid, and host cell DNA (HCD) packaging, are largely determined by the design and choice of biological starting materials and the upstream process. Therefore, we consider it essential to scale processes to achieve comparable quality and productivity at all scales to support clients throughout a product's lifecycle. This requires robust, fit-for-purpose analytics for in-depth product characterization. Here, we present AAV batch data from 250 ml to 200 L bioreactor sizes, using proprietary analytical methods to assess both the quantity and quality of the generated material.
Get unlimited access to:
Enter your credentials below to log in. Not yet a member of Outsourced Pharma? Subscribe today.