Does Single-use Seem Daunting? Try Starting With Standard Assemblies
By Thomas Erdenberger, Arlington Bio-Process Consulting
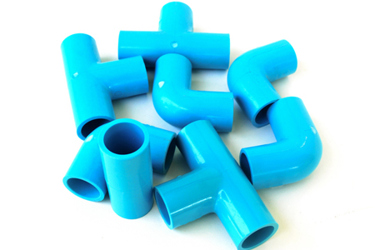
Single use technologies (SUT) have transformed biopharmaceutical manufacturing and have allowed us to make lifesaving medicines more quickly, consistently, and at lower cost with reduced quality and contamination risks. The benefits of single-use are well known now.
Recently, one of the more important discussions about SUT has centered on standardization. The concepts of industry standards for supplier quality and compliance, material selection, biocompatibility, and leachables and extractables testing have all been described. Then there are the end user’s material quality and compliance standards and operational and use standards. Many Bioprocess Online articles (search “single-use”) go through these requirements. These requirements are needed to maintain a high level of product quality and so that end users can construct formal quality risk assessments as the product moves toward late-phase clinical and commercial manufacture.
What else do we mean by “standards?” Some believe it should be about standards for the physical SUT components, as in shapes and sizes, connectivity, and integration.
These days, so many firms supply our industry with excellent systems that perform the same functions, such as bioreactors, mixing, TFF filtration, and chromatography (to name a few), with such unique SUT componentry that you’ll never see any real interchangeability (without major end-user modifications, i.e., “MacGyvering”). The instrumentation and PAT technologies have progressed to such an extent that it is difficult to decide the best technology to use in our processes.
The Sneaky ‘Vendor Lock-in’ Phenomenon
Revenue from hardware is one thing for a supplier, but the longer-term revenue stream is from the specialized and unique consumables required to use them. Whatever SUT system you buy, you can become locked into a unique set of consumables from a single supplier — a phenomenon called, appropriately enough, “vendor lock-in.”
A supplier may want you to buy all your SUTs exclusively from them to secure your supply chain. They may be pretty good with supply and lead times under normal conditions, but no manufacturer is an island. The pandemic taught us that supply chain disruption can be devastating to an effective drug-making operation. Risks for supply, quality, higher costs, and convenience are all factors that should be considered.
Some suppliers will have standard configurations for their products, but these are seldom configured for universal integration with other suppliers’ systems. In companies with multiple facilities or operational silos, colleagues can step on each other’s toes with orders for custom or even identical consumables from the same suppliers and create disruptions, inconveniences, redundancies, and higher costs. How can we reduce some of these risks?
Others have written that keeping things simple is a good strategy, while being conscious of when specialized or unique SUTs are not necessary.
Why Single-use Assemblies Make Sense For Beginners
If you want to take advantage of SUT and make the most of it with standardized componentry, one avenue is to start with a close look at some standard assemblies. They’re a straightforward and practical way to begin integrating SUT into your processes.
Below, I describe a modular SUT approach with some simple assemblies that can be arranged and connected to fit most any process. The wye, tee, cross, and pigtail can be found as part of any unique SUT you might discover. Inline filter assemblies are especially useful for maintaining aseptic conditions and can use most any preferred capsule filter(s). With these simple assemblies, a fully closed aseptic process system can be constructed.
The beauty of using these standard SUT components is that you can create virtually any configuration for any process, batch, fed batch, or continuous. You can make these in several tubing/connector sizes as you find use for. There are now many aseptic connection devices to choose from. Tubing welding can be a preferred fully validated method of strong connections, but these add time for assembly. These standard assemblies are especially useful for a multiproduct suite or facility because a specific configuration can be assembled based on an SOP for a given process. Only operator training and capturing lot numbers is necessary.
For example:
- Using a wye and a filter assembly, you can construct an infinite number of filters in parallel or in series for media, buffers, and processes.
- You can configure a manifold with an infinite number of ports using tees or crosses (or both).
- You can connect jumpers of one length (or two) to create any transfer line.
- You can use a sample assembly to configure sample points at any point in the process.
It is important that the choice of aseptic connectors is conserved throughout the assemblies (genderless). If you are faced with differing connectors on a unique process system assembly (depending on the supplier), adapters can be constructed using the unique connection device and your standard connector, or a pigtail can be used as a bridge using a tubing welder provided weldable tubing (TPE) is used.
There are other important advantages to such an approach. From a supply perspective, these can be commoditized and sent to bid from preferred suppliers with primary and backup supplies since these can be made by most any SUT supplier today in the same or similar materials of construction and components. The risk of supply interruption is reduced and can lower material costs.
For a multiproduct/multi-facility operation, this approach could offer centralization of in-house ordering, warehousing, and distribution for much greater efficiency and reduction of waste. No stepping on each other’s toes, leading to long lead times. Inventory and just-in-time (JIT) warehousing for a given process saves space and, since the quality and release specifications can be made the same throughout the operation, assemblies can be distributed across the entire operation as needed, thus reducing the overall QC and QA efforts, saving more money and achieving consistent high quality.
About The Author:
Thomas Erdenberger has more than three decades of experience as a biotechnologist in industrial and biopharmaceutical manufacturing. During his career, he has focused on areas such as process development and optimization, tech transfer, and technology development. He was an early advocate of single-use technology and worked on the supplier side as an inventor and manufacturer of SUT. He’s the founder and principal of Arlington Bio-Process Consulting. Find him on LinkedIn and reach him at thomas.erdenberger@arlingtonbio.com.