Cleanroom Gowning Programs Compliant With EU GMP Annex 1
By Crystal M. Booth, PSC Biotech
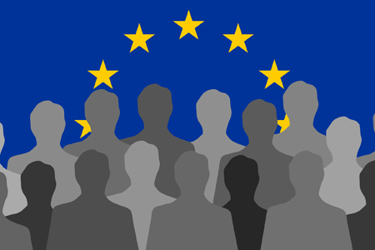
Humans are the primary source of contamination in cleanrooms. Cleanrooms are designed to aid in the protection of the items being manufactured from environmental contaminants as much as possible. To protect the items being manufactured from human contamination, special gowning requirements and gowning qualification guidelines are necessary.
This is part 2 of a two-part article. Part 1 focused on an overview of cleanroom gowning as it pertains to aseptic manufacturing of medicinal products and the updates to gowning requirements in the revised Annex 1 document, The Rules Governing Medicinal Products in the European Union Volume 4 EU Guidelines for Good Manufacturing Practice for Medicinal Products for Human and Veterinary Use, which was published on Aug. 22, 2022. This article focuses on establishing an aseptic personnel gowning qualification program per the Annex.
Establishing A Compliant Aseptic Personnel Gowning Program
For traditional grade B areas, an aseptic gowning qualification program should be established to assess the ability of personnel to maintain the microbial quality of the gown after gowning.1 There are four key components of a compliant aseptic personnel gowning program, as follows:
- Initial training and education (stage 1)
- Gowning training, practice, and observation (stage 2)
- Qualification to enter grade B areas (stage 3)
- Program maintenance (stage 4)
Stage 1: Initial Training and Education
In the aseptic gowning qualification program, the first key component is the initial training and education stage. Training should be performed by qualified personnel. USP <1116> Microbiological Control and Monitoring of Aseptic Processing Environments provides topics that should be addressed; topics can be combined to minimize the number of courses required. The following is a list of topics that should be emphasized during the classroom portion of the gowning training program:2
- Hygiene2
- Microbiology2
- Cleanroom practices2
- Contamination control2
- Aseptic technique2
- Protection of sterile products2
- Potential implications to patients if the product is non-sterile2
- Aseptic clothing and gowning2
- Cleanroom behavior2
- Facility design overview
- Material and personnel flows in and out of cleanrooms
- Cleaning, disinfection/sanitization, and sterilization
- Environmental monitoring
- Personnel monitoring
- Process simulations
The hygiene training course should include the importance of good hygiene, showering, hand washing, not using cosmetics or jewelry, and reporting compromised skin conditions (e.g., flaking skin, sunburn, open wounds, recent tattoos, etc.). It is important that the operators understand the expectations of management regarding good personal hygiene as well as why the expectations are established. Building a good relationship with employees is essential so they will feel comfortable enough to self-report illnesses or conditions that may compromise the manufacturing environment.
General microbiology training based on gowning qualification guidelines should include a general understanding of the different types of microorganisms and their sources. Basic concepts such as not allowing wood or cardboard into the clean areas and cleaning up standing water as soon as possible should be stressed as ways to prevent microbial contamination. Employees need to understand that humans are the primary source of contamination and that their behaviors in the cleanroom could potentially lead to contamination of the product. By learning basic microbiology, employees will be empowered to locate some potential contamination sources themselves and correct the issues before microbial growth gets out of hand.
During the aseptic area clothing and gowning training, operators should learn the concepts behind aseptic gowning, the steps in the gowning process, how to check the gowning supplies for integrity, and the specific gowning requirements needed to access each area of the facility. A key point of focus during this classroom training should include the limitations of the gowning supplies and how the gowning process is critical in protecting the product and environment.
Operators should also be trained in the proper behavior inside the clean area. They should understand the importance of slow and deliberate movements, the importance of spraying their hands with a sanitization agent regularly prior to performing interventions, and the importance of waiting the appropriate contact time. Operators should also learn not to pick up items off the floor because the floor is the dirtiest part of the cleanroom.
Properly designed facilities help control microbial contamination. Training according to gowning qualification guidelines on the basics of facility design should include concepts of airflows, pressure differentials, and the different cleanroom grades. The importance of removing street clothes, changing into cleanroom scrubs, and progressive gowning/sanitization concepts to protect the inner filling grade A/B operations should be stressed during the training. Operators should understand the concept of the facility design moving from the dirtiest areas (uncontrolled environments) to the cleanest areas (grade A environments). Operators should learn the theory of “first air,” high-efficiency particulate air (HEPA filters), room air changes, unidirectional flow, and the importance of keeping the return air ducts unobstructed. Some regulatory requirements and information on the grades of cleanrooms to assist with training are in Annex 1 and the FDA’s 21 CFR Part 211.42.
The material and personnel flow program overview should include an introduction on how materials and personnel flow into and out of the clean areas. Training should include the approved methods of transferring materials and the approved pathway for personnel traffic, including the gowning control points. This aseptic gowning qualification program is necessary to keep contamination from the outside world from entering the cleanrooms. Personnel must follow gowning procedures, hygiene requirements, and the established process flows to enter the cleanrooms. Personnel must only enter and exit the cleanroom through dedicated paths to avoid cross contamination.
Material transfer may be performed by using sterilized items prepared using a double-door autoclave, vaporized hydrogen peroxide (VHP)/peracetic acid chamber, dry heat oven, multiple bags, or chemical disinfection. To use the multiple bag transfer method, items can be bagged or covered with several bags/covers equal to one more than the number of increasing classification changes needed and then sterilized. A single bag/cover is removed at each classification change and the final bag or cover remains for the final classification. This transfer process leaves potential contaminants behind in the “dirtier” classified area.
Chemical disinfection can be used before transporting an item into the cleanroom. The item should be disinfected and transitioned into the cleanroom via a material airlock or pass-through. Minimum wet contact time with the disinfectant is required and must be followed. When disinfecting carts for transfer into the cleanrooms, operators should be reminded to focus on cleaning the cart’s wheels.
Differences between cleaning, disinfection/sanitization, and sterilization should also be taught in the classroom. The validation and application of chemical reagents should be reviewed with the operators so that they understand which disinfectants are approved, how long the wet contact time should be administered, and how to properly clean the area.
Employees should also be taught a rudimentary introduction to the importance of environmental monitoring. The fact that microorganisms can travel attached to particles in the air should be stressed. The rationale for the monitoring locations should be discussed, as well as how to conduct personnel monitoring and the importance of the samples. If applicable to the facility, employees should also be introduced to the concept of media fills and aseptic processing.
Other key items to emphasize during the initial training and education stage (stage 1) include:
- The implications to the patient if the product is not sterile. 2
- The importance of good personal hygiene and careful attention to detail in aseptic gowning cannot be overemphasized.3
- Only trained personnel who have completed all three stages of certification should be allowed in the cleanrooms.
- Employees who are sick or have conditions that shed skin (e.g., sunburn or a recent tattoo) should not enter cleanrooms.
- Do not wear jewelry or makeup in the clean areas.
- The primary sources of contamination in cleanrooms are humans.
- Always use good aseptic technique and never break first air.
- Move slowly and deliberately in the cleanrooms.
- Do not shout or talk excessively, as facemasks are not total barriers to microorganisms.
- Leave the cleanroom immediately and replace compromised items (e.g., gloves).
- If something drops on the floor, leave it there. The floor is considered the dirtiest part of the cleanroom.
Stage 2: Gowning, Training, Practice, and Observation
Once an employee has completed all the stage 1 aseptic gowning qualification courses and the documentation has been approved, they may proceed to stage 2, gowning training, practice, and observation. During this stage, the trainer should demonstrate the proper gowning technique to the trainee. The trainee should be able to practice gowning in a safe, non-critical environment. They should be allowed to repeat the training until they feel comfortable with the process.4 During these practice sessions, the personnel should also practice glove sanitization. The gowning training should be performed by an analyst who regularly enters the aseptic cleanroom to ensure that proper gowning techniques are taught and followed.
After the trainee feels ready, the trainer will observe the trainee and ensure they are competent in the aseptic technique. Finally, when both the trainee and trainer feel confident in the trainee’s ability to maintain the quality of the gown during the gowning procedure, the trainee can proceed to stage 3.
Stage 3: Qualification to Enter Grade B Areas
The third key component is the aseptic gowning qualification to enter grade B areas (stage 3). During this stage, the trainee must undergo three successive gowning processes and be evaluated through microbiological sampling.4 Microbial sampling is typically performed using contact plates that are filled with sufficient growth media (usually tryptic soy agar) to provide a convex surface to support the growth of microorganisms. These plates are rolled front to back on the sample area and then incubated for a determined period (typically three to five days at 30 to 35 degrees C).
The incubation time, type of media, and incubation temperature are determined during method verification studies. Method verification may consist of performing microbial sampling with the contact plates (also known as RODAC plates: replication organism detection and counting) and then performing growth promotion testing of the media using compendial microorganisms or environmental isolates to prove that the method will support growth of microorganisms if they are present on the media.
Another important factor to consider is that sampling leaves a media residue that needs to be removed to avoid cross contamination. Surfaces and personnel should be monitored after critical operations. 2
Guidance on where to monitor personnel is vague. Sampling is mentioned in multiple documents, with the monitoring emphasis placed on gloved fingers. Recommended location sites for gowning qualification include:
- Gloved fingers1,4
- Face mask1,4
- Forearms1,4
- Chest1,4
- Shoulder4
- Thighs4
- Hood4
- Boots
Regulatory recommendations of limits are listed for gloved fingers.2,3 As previously mentioned, guidance on where to sample personnel on their gowning is vague. Likewise, alert and action levels are not provided in the regulatory documents, except for gloved fingers. Appropriate alert and action levels need to be set for each sample site. These levels should be set based on contamination risk to the product.5 In cases where regulatory documents provide gowning qualification guidelines, risk justification should not be used to exceed the limits provided in regulatory documents.
The revised Annex 1 states that “a risk assessment should evaluate the locations, type and frequency of personnel monitoring based on the activities performed and the proximity to critical zones. Monitoring should include sampling of personnel at periodic intervals during the process. Sampling of personnel should be performed in such a way that it will not compromise the process. Particular consideration should be given to monitoring personnel following involvement in critical interventions (at minimum, gloves, but may require monitoring of areas of gown as applicable to the process) and on each exit from the grade B cleanroom (gloves and gown). Where monitoring of gloves is performed after critical interventions, the outer gloves should be replaced prior to continuation of activity. Where monitoring of gowns is required after critical interventions, the gown should be replaced before further activity in the cleanroom.”2
Annex 1, 2022, also states that “contact plate limits apply to equipment, room and gown surfaces within the grade A and grade B areas. Routine gown monitoring is not normally required for grade C and D areas, depending on their function.2 Any growth in the grade A area should result in an investigation.” 2 In this case, no growth should be recovered in the grade A areas and five colony forming units (CFU) are allowed per contact plate in the grade B areas. 2
Occasionally, personnel may fail to meet personnel monitoring requirements. When this occurs, a thorough investigation should be conducted to assess the impact on the area and product. Personnel may be disqualified from entering cleanrooms under the following circumstances:6
- A negative trend is found on personnel monitoring.
- Associate has exceeded the requalification period.
- After a critical observation (e.g., incorrect or inappropriate behaviors).
- Results of an investigation indicate incorrect/inappropriate aseptic behaviors or a direct root cause to an operator/associate.
- An associate has not entered the area for an extended length of time.
If disqualification occurs, the associate must re-train on gowning procedures and repeat personnel monitoring of three consecutive gowning events. The gowning events must meet the same gowning qualification acceptance criteria as the original gowning qualification. If the associate continues to fail, they may be excluded from the qualification process and other corrective measures may be required (e.g., job reassignment).
Periodically, associates need to requalify on personnel gowning. This is essential in continuing the education of the operators. Periodic requalification can serve as reminders to the associates the importance of their behavior and proper gowning in the cleanroom environments. Annual requalification is normally sufficient for those automated operations where personnel involvement is minimized, and monitoring data indicate environmental control.1 Written procedures should adequately address retraining, requalification, or circumstances of employee reassignment.
Completion of gowning qualification stages 1-3 qualifies associates to enter grade B areas. Any critical operations or interventions into the grade A area cannot be performed until the associate trains on all relevant procedures and has participated in a media fill.
Stage 4: Program Maintenance
A vigilant and responsive personnel monitoring program should be established. Following the completion of the initial aseptic gowning qualification (stages 1-3), associates must be assessed continually to ensure they are maintaining the asepsis of their gowns. Daily (after critical interventions), or in association with each lot, each associate’s gloves should be monitored for microorganism contamination. Other locations on the associates’ gowns should be strategically selected and sampled. Tracking and trending associate performance helps to aid in the maintenance of the program. Depending on personnel performance, disqualification may be warranted.
In addition to routine personnel monitoring, associates should be requalified on an annual basis. Educational courses on gowning qualification guidelines should be offered at regular intervals so that associates can attend the trainings prior to going over the requalification grace period due date. Electronic training systems that can send reminders and due dates and create gaps for qualifications can aid in reminding associates of their requalification timelines. Annual requalification should include the following.
- Participation in educational refresher courses
- Single successful trial of gowning qualification
- Participation in a successful media fill (as applicable)
It is important that training is not a discrete event, but an ongoing occurrence, within a culture where coaching and feedback are given routinely by experienced personnel.7 Personnel are critical to the maintenance of asepsis in the controlled environment.8 Properly educating and training the personnel according to the gowning qualification guidelines is essential to protect the environment and product from human derived contamination. Even when correctly gowned, employees continue to slough microorganisms.3
Thorough aseptic gowning qualification program is required. Personnel must maintain high standards each time they deal with sterile product. 8 The best way to ensure product safety is through contamination prevention.
Conclusion
A vigilant and responsive personnel monitoring program can be established and gowning qualification acceptance criteria can be explained. There are essentially four key components of a compliant aseptic personnel gowning program for cleanroom entry: initial training and education; gowning training, practice, and observation; qualification to enter the grade B area, in which general growth media touch plates are used to analyze whether the trainee gowned correctly without contaminating the sterile cleanroom gown; and program maintenance, which consists of routine monitoring, requalification, and disqualifications when warranted.
By establishing a robust, compliant gowning program as outlined in this article, adhering to regulatory requirements, clearly defining the gowning qualification acceptance criteria, and following the applicable site procedures, firms may avoid regulatory observations concerning microbial controls in respects to cleanroom gowning.
References
- Guidance for Industry (2004), Sterile Drug Products Produced by Aseptic Processing- Current Good Manufacturing Practice. Pharmaceutical cGMPs. Accessed on October 30, 2022 at https://www.fda.gov/regulatory-information/search-fda-guidance-documents/sterile-drug-products-produced-aseptic-processing-current-good-manufacturing-practice
- Annex 1 (2022), The Rules Governing Medicinal Products in the European Union- EU Guidelines to Good Manufacturing Practice, Medicinal Products for Human and Veterinary Use. Annex 1- Manufacture of Sterile Medicinal Products. European Commission EudraLex, 4.
- United States Pharmacopeia (USP) <1116> Microbiological Evaluation of Cleanrooms and Other Controlled Environments.
- Brandes, R. (2012), Aseptic Processing: Qualification of Personnel. GMP Publishing, 12. Accessed on October 30, 2022 at: https://www.gmp-verlag.de/content/en/gmp-news/gmp-newsletter/gmp-logfile-lead-article/d/1215/qualification-personnel-aseptic-processing-gmp-logfile
- FDA Manual (2015), Food and Drug Administration Compliance Program Guidance Manual Chapter 56- Drug Quality Assurance. Sterile Drug Process Inspections, Program 7356.002A, Accessed on October 31, 2022, at https://www.fda.gov/media/75174/download
- PDA (2022), PDA Technical Report No. 13- Revised 2022: Fundamentals of an Environmental Monitoring Program. PDA, Bethesda, MD.
- Hayes, B. (2015) Managing Aseptic Gowning within Classified Environments. Clean Room Technology, 3. Accessed on October 30, 2022, at: https://cleanroomtechnology.com/news/article_page/Managing_aseptic_gowning_within_
classified_environments/107339 - Pharmaceutical Microbiology Manual (2020), Pharmaceutical Microbiology Manual, Version 02, ORA. 007, 25Aug2020. Accessed on October 30, 2022, at https://www.fda.gov/media/88801/download
About The Author:
Crystal M. Booth, M.M., ASQ-CQE, PMI-PMP is a senior technical director at PSC Biotech and has over 20 years of experience in pharmaceutical microbiology, environmental monitoring, and quality assurance. She obtained her master’s degree in microbiology from North Carolina State University. She is a seasoned, award-winning technical writer and author of Method Development and Validation for the Pharmaceutical Microbiologist. During her career, she has worked in microbiology, consulting, quality assurance, CDMOs, R&D, and quality control laboratories. Booth has developed and validated numerous microbial methods and has worked with many different product types. She also performs cGXP audits, risk assessments, and gap assessments. Booth is the author of the Institute of Validation Technology (IVT) peer reviewed articles Harmonized Microbial Limits Testing Validation Strategies and Antimicrobial Effectiveness Testing Validation Strategies.