Best Practices For Handling Potent APIs
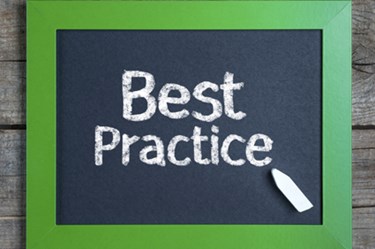
By Dr. Mike Battrum, Head of Engineering, Aesica Pharmaceuticals
In recent years, an increasing number of pharmaceuticals and intermediates have been developed that fall into the category of potent materials. In this context, ‘potent’ describes substances that have an Occupational Exposure Limit (OEL) between 0.03 and 10 μg/m3 when measured on an eight-hour time weighted average — a level that a healthy worker could safely inhale up to 40 hours a week over a working lifetime. These substances are often categorised as Safebridge Category 3.1
“Materials”, meanwhile, are defined as dry or partially dry powders that have the potential to become airborne as dusts and could therefore be inhaled by unprotected employees and be absorbed through the lungs or mucous membranes.
It is the legal responsibility of employers to provide a safe and healthy working environment, which, in practice, means ensuring that employees are not subjected to concentrations of substances above the OEL. The facilities, equipment, and operational procedures for handling potent materials on a commercial scale must therefore be designed, constructed, and proven to be safe before manufacture can commence.
The fundamental basis of design is to provide primary protective equipment (PrPE) that is fully contained and prevents human contact with potent materials. That equipment should also be located in a facility that provides secondary containment to ensure that airborne particles cannot reach the outside world should the equipment fail.
PrPE
The open handling of powder is expressly prohibited for potent materials. Therefore, contained systems must be used. The choice of contained system will depend on a containment performance target which is less than or equal to the OEL. This performance target must be given to an equipment vendor when specifying equipment. Different pieces of equipment offer different containment performance, and knowledge of equipment capabilities is required when selecting equipment for a given purpose and potent material.
The handling or manufacture of potent materials will invariably centre around a piece of process equipment in which dry powders are created or processed. Typical examples are filter dryers, mills, dryers and blenders, granulators, tablet presses, and capsule fillers. Other types of equipment that have a lower, but still quantifiable, risk include blister packers, coaters, and tablet bottle fillers.
For all of these equipment types, it is essential to examine two key factors during the design phase: how leak tight the equipment is and under what pressure it will operate; and how materials are transferred in and out of the equipment.
In most cases, equipment for handling potent materials should be operated under negative pressure. When setting up the machinery, it is important to examine all possible leak points to ensure that powder leakage cannot occur. Typical areas where leakage may occur include mechanical seals, extraction vents, and access panels. Technical advances like gas-tight mechanical seals and inflatable door seals warrant serious consideration.
The weak points in any piece of process equipment are the systems for transferring powder into and out of the unit. Barrier isolators are the most common equipment for contained handling of potent materials. Isolators can be stand-alone, fully enclosing the necessary production equipment, or they can be integrated with other process units. Operator access is usually via glove ports that are located in positions that allow the greatest ease of operation.
Isolators can be either fixed-wall or flexible-walled. The former are robust pieces of equipment, usually made of stainless steel, and they are frequently integrated with other process units in use. Hard-walled isolators are convenient in API environments where potential damage is a factor. However, they are difficult to operate with only average visibility.
Flexible-walled isolators are frequently mobile stand-alone units, and they usually have stainless steel bases and tubular frames. A number of different types of plastic are available to suit different situations. They are generally easier to operate and have excellent visibility.
Both types can be operated either at atmospheric pressure or under negative pressure (at least -30 Pa). Negative pressure isolators deliver much better containment performance. Isolators should be supplied with fresh air via a single HEPA filter to guard against reverse flow and exhaust via two HEPA filters placed in series to mitigate against filter failure.
Split butterfly valves (SBVs) are another common method of transferring solids from a fixed contained unit to another mobile unit. Examples include transfer from an isolator (fixed) to a stainless steel container (mobile), and from a stainless steel container (mobile) to reactors (fixed) or tablet presses (fixed).
Usually an SBV is constructed with a passive half, which is connected to the mobile unit, and an active half, which is connected to the fixed unit. There are many types of valves available from simple manual valves to fully automated valves integrated with face extraction systems. Each is designed to achieve a desired containment performance.
Bespoke glove bags are often required for very specific containment applications. Known installations include cartridge filter change bags and bags for access to cone mill screens. In general, glove bags operate at atmospheric pressure and use small HEPA filters to allow the bag to breathe. Thus, these bags neither inflate nor deflate.
Analogous to these are continuous liners used for the transfer of items for disposal. Items are placed into the liner, which is then sealed using a twist-tie-cut method to preserve containment. This can be carried out using special crimping tools.
At some stage in the process cycle, it will be necessary to clean the containment equipment. This may be at the end of each batch, at the end of a multiple number of batches, or at the conclusion of a campaign. Whatever the reason for cleaning, the containment equipment must be designed so that the appropriate cleaning methodology can be carried out. The main three stages of cleaning are wash-in-place (WIP), wiping down, and dismantling.
An automatic clean-in-place (CIP), or WIP system, is always preferred as the first phase of any cleaning process, as it should reduce gross contamination down to an acceptably low level. CIP and WIP systems are of greatest use in equipment where the internal components of the equipment can be deluged with water or other appropriate detergents and solvents. In the case of SBVs, many suppliers provide special wash attachments that dock to the passive or active part of an SBV and enable retractable spray balls to penetrate past the valve so that internal areas can be washed.
The second phase, particularly for isolators, is to pass in wet wipes so that internal surfaces can be cleaned manually via the access gloves. Thus containment is maintained while cleaning operations are in progress. It is important in the design phase to ensure that all surfaces can be reached using the glove ports.
In some cases, it may make sense to have specialist cleaning tools within the isolator. In cases where the next phase is the dismantling of equipment, it may be sensible to carry out swab tests to confirm the cleanliness of equipment and therefore ensure the continued safety of operators.
The final phase is often the dismantling of component parts for intensive mechanical cleaning. However, in the case of plastic containment devices, it may be simpler just to dispose of the item and fit a new one.
Secondary containment
PrPE is only part of an overall solution for the handling of potent materials. While correctly designed, operated, and maintained primary equipment should protect operating staff, there is always a risk that the systems may fail or be operated incorrectly. Contamination at these low levels cannot be seen nor detected, and, therefore, it is incumbent on employers to ensure that any possible contamination cannot exit the building in which the potent material is being handled. This is known as secondary protection.
Facilities designed for the manufacture or handling of potent materials should follow clear guidelines:
- Except for emergency exits, there should be at least two rooms between the room in which the manufacture and handling takes place and the outside world
- The room in which the manufacture and handling takes place should be at a negative pressure in relation to an adjacent room
- Operators should enter via an airlock that is at a higher pressure relative to the rest of the facility and exit the facility via a decontamination room.
- Raw materials should enter via an airlock that is at a higher pressure relative to the rest of the facility
- Product packaging must be cleaned before it can be transferred from the facility via an airlock that is at a higher pressure relative to the rest of the facility.
- Entry and exit airlocks for materials and personnel should be interlocked so that people and materials only enter or exit in the correct direction
- Access to the area should be restricted to those trained to work in the facility
.
Figure 1 shows a diagram of the simplest possible facility that meets the guidelines and illustrates typical material, personnel flows, and air pressure regimes. It is recognised, however, that all facilities are different and may be subject to different influences based on the complexity of the process. This means that a number of factors should be taken into consideration, such as:
- Personal Protective Equipment (PPE): What work-wear and protective equipment is required? Where will storage and changing take place?
- How will people be decontaminated?
- How will decontaminated PPE be disposed of?
- How will all waste materials be made safe before they can be removed from the area?
- Will in-process testing be required? Where will testing take place – inside or outside the facility?
- How will documentation be handled?
- Where will emergency exits be located, and how will they be sealed?
- How will liquid effluent (wastewater) be handled?
Performance testing
It is vital to prove the efficacy of containment equipment by testing with surrogate powders before use on potent materials. This enables any issues or problems with the containment equipment to be resolved before potent materials are introduced. A methodology for the testing is provided in the ISPE Good Practice Guide.3
Testing is usually carried out over three runs of normal operation using a version of the operating procedure for the equipment, staying as close as possible to the intended operation. Sample analysis can take as long as two weeks before results are available, so time should be included in the project plan to evaluate the results.
Note that sample “blanks” are often submitted to test the efficiency of the analytical laboratory. It is wise to ensure full training of the equipment in previous phases of commissioning, as containment performance can often be operator-dependent. Indeed, a well-trained operator will operate equipment to meet its design criteria. Performance testing should be repeated after the first and second years of operation, thus providing three data points against which to fully evaluate the containment performance of the PrPE systems.
References:
1. Chemistry Today, March/April 2006, 24 (2)
2. www.niroinc.com/pharma_systems/hicoflex.asp
3. ISPE Good Practice Guide ‘Assessing the Particulate Containment Performance of Pharmaceutical Equipment’, ISBN 1-931879-89-3