A Practical Guide To Defining Priority Data In MES
By BioPhorum
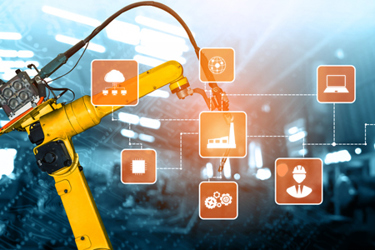
The adoption of automation and digital technology to unlock data potential has become an imperative to tackle pressing business challenges in the pharma/biotech industry encompassing speed, quality, agility, value, and sustainability. In today’s manufacturing industry, data is king, but with so many systems and sources, getting a clear and actionable picture of production can be complex and time-consuming. With the rise of Industry 4.0, manufacturers increasingly rely on data to drive decisions and improve processes. Manufacturing execution systems (MES) play a crucial role in the digitalization of manufacturing operations.
However, the data landscape across the value chain of manufacturing operations is complex and it is difficult to understand what the priority data truly is. MES platforms face the challenge of identifying the critical data that should be prioritized and developing a method for managing and presenting this data in a way that supports efficient and effective manufacturing operations.
A clear understanding of priority data would accelerate the adoption of MES in the industry, as the time and resource consumption to map out these requirements during MES deployment is high.
This article provides a high-level, practical guide to some of the main issues around identifying, defining, and rationalizing the priority data. The focus is on actionable data that will drive informed decisions and improvements. The objective is to empower MES supply partners to provide data more consistently and in line with industry standards such as ANSI/ISA-95.00.01-2010 and to ensure MES users have access to the data they need.
Scope
ANSI/ISA-95.00.03-2013 shows various activity models and flows of data for manufacturing information that enable enterprise control system integration and emphasize good practices in manufacturing operations management. This article focuses specifically on the activity model listed in Section 6 of ANSI/ISA-95.00.03: Production operations management, which lists the production level 1 and 2 functions. Here, it is used as a framework for mapping out the priority data elements required by biomanufacturers in MES. Figure 1 shows production operations management in the MES model, inspired by the activity model in Section 6 of ISA-95.00.03.
Figure 1: Production Operations Management In The MES Model
Benefits Of A Practical Guide On Priority Data
The biggest challenges to MES adoption include complexity, capital investment, risk, and time-to-value. While this attempt to identify, define, and rationalize priority data will provide a practical guide to biomanufacturers and MES supply partners, it also will lead toward building industry standards.
The benefits to biomanufacturers include:
- Reduced cost and faster implementation timelines: Connectivity and integration are less resource-intensive and more cost-effective, enhancing the time-to-value from the investment in MES deployment. As a result, MES adoption is much simpler across the enterprise.
- Better quality decisions and outputs: Biomanufacturers can focus on actionable data that drives decisions and improvements.
- Reduced time to implement new technology: Defining priority data simplifies the integration with other systems or tools, promoting interoperability and resulting in easier setup in IT infrastructure.
The benefits to MES supply partners include:
- Reduced development time: Supply partners have a better understanding of what the priority data is (versus the “nice to have” and bespoke), leading to better quality systems being designed and increased speed in the design stages.
- Increased speed to market: Road map development is clearer and end user priorities are more visible.
- Improved quality of the systems: Specifications are clearer for priority data, so consistency across supply partner systems and industry is increased. This creates consistency downstream in terms of data availability, which increases the quality of all systems.
Use Cases For The Priority Data
Effective management and definition of priority data in MES are pivotal in addressing many business challenges in biomanufacturing across the current value chain. Relevant use cases include, but are not limited to:
- real-time monitoring and visualization of the batch progression/insight into production progress
- insights into the status of production order management
- monitoring production yield and other performance metrics.
The ANSI/ISA-95 production operations management activity model shows the relationships between activities. This article follows the same structure and uses the same terminology. Table 1 lists the stakeholder teams and outlines the information available to them.
Table 1: Activity Model Stakeholders
Each of the activities in Table 1 forms a separate section below (sample tables are included, many others are available). The data and descriptions listed represent an overall industry consensus. The identified priority data is a starting point that may be revised based on feedback from industry practitioners. Prioritization of data for MES will be a necessary step to realize the value and benefits of BioPharma 4.0, an extension of Industry 4.0.
Chapter 1: Product Definition Management
This focuses on the management and maintenance of information related to the products being manufactured. It includes all the information needed to define, design, and produce a product throughout its life cycle. Identification, acquisition, and analysis of priority data from the scope of production definition management will ensure manufacturing efficiency, quality within the design space, compliance, and adaptability, ultimately contributing to the success of the entire production process. Table 2 shows some example information that should be configured in an MES that can be used by stakeholders or adjacent systems.
Table 2: Example Information Used For The Production Recipe
Chapter 2: Production Resource Management
The goal of production resource management is to ensure the correct resources are available at the correct time and in the correct quantity and condition. Within production resource management, the priority data requirements needed for production capability, resource capability, and resource availability are mapped separately. Identifying priority data across production capability, resource capability, and resource availability will help biomanufacturers optimize resource use, enhance production planning, and increase efficiency and cost-effectiveness in biomanufacturing processes. It provides real-time visibility into the resource status, allowing quick adaptability to changing conditions and reducing production disruptions. Not all MES will have the same information, e.g., the master data may come from another source, such as enterprise resource planning systems. However, this data is still considered priority data in the MES.
Production Capability
This refers to the ability of a manufacturing system to produce the desired quantities of products at specified quality levels within a defined time frame. It encompasses various aspects of production, including the capacity to meet production orders, achieve production schedules, and maintain product quality (see Table 3).
Table 3: Production Capability
Data is also needed for areas such as resource capability (equipment and personnel) and resource availability (materials and equipment).
Chapter 3: Detailed Production Scheduling
To successfully identify MES order details as data outputs, production scheduling data elements are essential, and priority data needs to be identified and defined accordingly. Production scheduling can involve determining the most efficient order of tasks and operations. It involves considering various factors (including resource, material, and equipment availability) and other parameters such as lead times, production capacity, inventory levels, and delivery dates. The goal of production scheduling is to enhance overall operational efficiency and effectiveness. Table 4 lists the priority data for end users associated with production scheduling in MES.
Table 4: Detail Production Scheduling
Data is also needed for areas such as production orders and production work orders.
Chapter 4: Production Dispatching
This is the collection of activities that manage the flow of production by dispatching production to equipment and personnel. It involves the coordination and control of resources, production work orders, and schedules to ensure the efficient and timely execution of production activities. These data elements play a crucial role in ensuring smooth execution, resource allocation, and tracking of work orders. Production dispatching is a critical function that bridges the gap between enterprise-level planning and shop floor control. It ensures that production operations are conducted efficiently and resources are optimized. Production dispatching involves a production work order dispatch list (see Table 5 for some example information), material dispatch list, equipment dispatch list, and personnel dispatch list.
Table 5: Example Data Used For The Production Work Order Dispatch List
Chapter 5: Production Execution Management
This encompasses the activities and processes that facilitate the effective execution and monitoring of production operations. MES platforms are central hubs for monitoring and managing production progress, equipment status, and performance. Precision, data integrity, and compliance with strict regulatory requirements are crucial. Priority data access to production execution management ensures that work is conducted according to specifications, enables quick responses to exceptions, supports regulatory compliance, and drives operational excellence in manufacturing processes. From the perspective of priority data, production execution management should comprise production progress, equipment status, audit trail information, and batch record exceptions (see Table 6).
Table 6: Production Progress
Data is also needed for areas such as equipment status, audit trail information, and batch record exception.
Chapter 6: Production Data Collection
Data collection captures production counts and quality metrics, providing insights for process improvement and quality control. Analyzing collected data supports data-driven decision-making, quality assurance, and cost-effective production. The primary purpose of production data collection is to capture and record data related to various aspects of the manufacturing process. This data can include information about production quantities, equipment status, and quality metrics (see Table 7). Data is collected from various sources in the manufacturing environment. It can include data from sensors, programmable logic controllers, human-machine interfaces, and other automation and control systems.
Process data originates from sensors, programmable logic controllers, supervisory control and data acquisition systems, historian systems, distributed control systems, and Internet of Things devices, capturing real-time measurements of parameters like temperature and pressure.
Table 7: Process Data
Data is also needed for areas such as quality data, inventory data, equipment status, and production counts.
Chapter 7: Production Tracking
Production tracking aims to provide real-time visibility into the status of manufacturing operations. It involves capturing and monitoring data related to the production process to ensure that products are being manufactured efficiently and comply with quality standards. Production tracking can be divided into three sections: scheduled work, work in progress, and reporting (completed work). An example of scheduled work is shown in Table 8.
Scheduled Work
The goal of tracking scheduled work is to ensure that production plans are on track and that resources are allocated efficiently (see Table 8).
Table 8: Scheduled Work
Data is also needed for areas such as work in progress, report header, recipe parameters list, batch execution history, material consumption list, quality control data list, exception log, electronic signatures list, audit trail, critical process parameters, product serialization, track and trace, quality, and yield.
Chapter 8: Production Performance Analysis
Having data for production performance analysis in an MES is crucial for informed decision-making and driving continuous improvement (see Table 9). By analyzing KPIs such as cycle times, downtime, yield, and efficiency, managers can assess overall performance, identify areas for enhancement, and optimize resource allocation. This leads to improved production efficiency, reduced costs, and the ability to meet business objectives.
Production performance analysis also enables benchmarking against historical data and industry standards, facilitating goal setting and motivating the production team. Real-time monitoring and feedback provided by an MES allows for proactive maintenance, prompts corrective actions, and maintains optimal production levels. With these capabilities, manufacturers can make data-driven decisions, implement process improvements, and achieve higher productivity and profitability.
Table 9: Overall Equipment Effectiveness (OEE) Metrics
Data is also needed for areas such as downtime, cycle time, production throughput, material throughput, production adherence, and changeover time.
Conclusion
The biomanufacturing industry stands at the threshold of a transformative era, where integration of digital technologies like MES is paramount for driving efficiency, agility, and sustainability. However, the complexity surrounding data management and interpretation within MES platforms presents a significant obstacle to realizing its full potential. This article addresses this challenge by proposing a practical guide to identify, define, and rationalize priority data elements within MES, with a specific focus on the biopharmaceutical sector.
The benefits of this standardized approach extend beyond cost reduction and faster implementation timelines for biomanufacturers. It also enables vendors to reduce development time, improve system quality, and gain a competitive edge in the market. With a clearer road map for MES implementation and interoperability, industry can expect accelerated adoption rates, fueling further innovation and growth in biomanufacturing.
The journey toward standardization of priority data is ongoing and iterative. While the identified priority data elements serve as a starting point, continued collaboration and refinement will be essential to adapt to evolving industry needs and technological advancements. By embracing this road map for prioritizing data within MES, the biomanufacturing industry can navigate the complexities of digital transformation with confidence, driving toward enhanced operational efficiency, quality, and, ultimately, patient outcomes.
This article summarizes some of the main points from a recent BioPhorum publication on this topic. To learn more about the additional data points that are required, check out the full paper, Navigating the data maze: a practical guide to defining priority data in MES.