Moving Your QMS Beyond (Current And Future) Regulatory Expectations: A 7-Step Process
By Paola Murphy And Sheila Gwizdak, Halloran Consulting Group
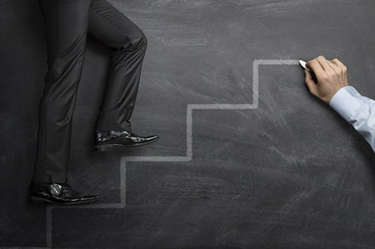
Currently, sponsors running clinical trials have established quality management system (QMS) frameworks inclusive of organizational structure, processes, and procedures on the following premise: The QMS helps maintain a company’s compliance to regulations, ultimately with the hopes of ensuring patient safety, product quality, clinical responsibility, and data integrity. However, under the new QMS requirements triggered by changing regulations such as ICH E6 R2, EU Clinical Trial Regulations (CTR), EU Medical Device Regulation (MDR), General Data Protection Regulation (GDPR), and rapid growth in innovation, this oversight and process management framework is no longer sufficient. A new QMS should be built to support the following objectives:
- Real-time identification of emerging opportunities to innovate while managing risk to patient safety and data integrity
- Established metrics and immediate data availability to ensure quality and address any emerging risks and potential quality issues in real time
- Focus on high-value activities that increase efficiency while ensuring patient safety and data integrity
- A culture of data literacy, learning, and continuous improvement
Regulators are now looking for companies to measure outcomes from their processes with feedback loops for continuous improvement, whereas in the past the focus was on measuring compliance to a set of procedures. It will be difficult for companies to fulfill the new and future regulatory requirements and expectations without taking a much more comprehensive approach. A mature QMS framework has these components working together:
- Technology (for transparency and access to data, which means being able to aggregate data across all sources and vendors)
- Processes (to ensure there are defined processes to assess, share, and communicate key data triggers for immediate action, and that drive changes back into the processes for continuous improvements)
- People via appropriate organizational and governance models (to ensure the organization has appropriate oversight and skill sets to ensure data-driven decisions are being made)
Those striving to take advantage of this time are positioning themselves as leaders in the industry. What several companies do not yet realize is that having a state-of-the-art QMS allows you to not just have a compliant quality system. It also provides real-time data access up and down the organization, efficient processes working together in the most effective way, and continuous improvement mechanisms across the entire organization to easily adapt to changes in regulations and internal and external industry shifts.
There are a few ways to look at this, and they start with having the end in mind. Where are you now in the QMS maturity model, and where do you want to be one year from now and three years from now? Depending on where you sit and your cultural or organizational constraints, this journey can happen at different speeds, but the process remains the same:
1. Build a strong business case for your executives and organization (competitive benchmarks, quantitative and qualitative benefits). Utilize external resources available (e.g., http://www.transceleratebiopharmainc.com) to gather the data needed to build the business case. A preliminary assessment of where you are and where you want to be may be required before you complete this step and communication during this time is critical to start getting the organization comfortable with the need for change.
2. Assess where you want to be. Take your time to perform this assessment and talk about the “art of the possible” using your external benchmark data and insights. What does a mature, optimized QMS look like, and how far are you from this? How far can you push change up and down the organization? How quickly can you get there? Be bold in defining your future vision, but balance this with what can be achieved in a realistic timeframe.
3. Design solutions that feed into an implementation plan incorporating organizational, process, and technology streams. This is where many companies fall short, retreating back to building silos for implementation or not seeing this as a cross-functional initiative touching several different parts of the organization, a transformation for the organization. There are specific tactics that can be employed to make this as efficient as possible including taking a comprehensive 360-degree approach to process evaluations and identifying critical organizational, process, metrics, and technology needs in one step. All stakeholders should think about and span all three of these verticals, organizational, process, and technology.
4. Define your change management strategy. This effort cannot be underestimated, as it is critical to get the organization aligned in seeing this as a big change moving the organization to a new way of thinking. Why now? Why is this important? How does it impact me? What will I see at the end of all this? Communication tactics up and down the organization are carefully thought through. Who are your change resistors that you need to get onboard? What level of information do you need to share and when? What training is needed to get the organization baselined to regulatory shifts and gain the new skills required?
5. Execute the implementation plan in a thoughtful way that allows specific streams to build off each other and aid in pushing specific change management strategies. This too is an art form in that you have to appreciate the resourcing constraints and also the company’s cultural norms. For example, in some companies that need to move quickly through the changes or aggressively pursue innovations, you can push to advance change by tackling creation of new organizational and governance models first before the processes are revamped. But in other cases where change resistance is huge, this may be a recipe for disaster! Stakeholders may need to feel comfortable with where the tactical processes are going before leaping into strategic organizational change discussions.
6. Understand where you will pilot the change. Are you going to ease them into the changes for specific study transitions? Will you test the process first in a sequenced approach? Measure, revise, and retest? What are the pros and cons? What technology constraints are keeping you from rolling out the changes?
7. Understand what post-implementation hyper-care may be needed to continue to measure and share successes. Manage change control processes so folks do not revert.
If you get this right, you could position your organization to work smarter and faster, outperforming your competition with leading clinical trials practices and innovative solutions. The most successful companies have jumpstarted their QMS journey by continuing to push innovation and are implementing foundational technology platforms that enable seamless data aggregation and reporting across the various data sources. Regardless of where you start, don’t be left behind your competition by ignoring your QMS and where you need to be headed.
About The Authors:
Paola Murphy, managing director, joined Halloran Consulting Group in 2010. She has over 20 years of life sciences experience focused in the following areas: clinical development and operations, strategy, due diligence and integrations, quality systems, medical safety, continuous improvement and change management. Murphy works with life sciences companies driving global, cross-functional continuous improvement initiatives with a focus on ensuring compliance and operational excellence. She is Regulatory Affairs Certified (RAC) by Regulatory Affairs Professionals Society. She earned an M.P.H. in epidemiology and biostatistics at Boston University School of Public Health and a B.S. in biology at Providence College.
Sheila Gwizdak, principal consultant at Halloran Consulting Group has over 25 years of experience in the biotechnology and pharmaceutical industry. Her career has focused on quality, process improvement, and training including the execution of corporate and department-level quality assurance initiatives such as SOP development, compliance, gap analyses and remediation, inspection readiness, audits, and training. Gwizdak also has specific experience in inspection readiness activities (FDA, EMA, MHRA, and PMDA) including storyboard development, coaching, and conducting mock inspections. Before joining Halloran, she held a series of progressive positions in clinical quality, operations, and training, where she supported the development and implementation of a quality management frameworks that included the standardization of procedures, systems, training, and processes.